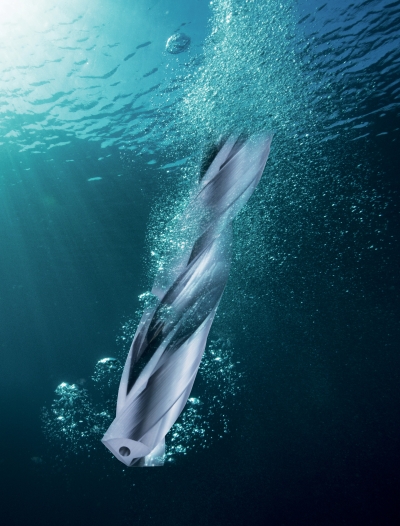
Certain processes and high-performance drills are especially important for guaranteeing reliability and high quality in deep-hole drilling. Tool manufacturer Inovatools supports the metalworking industry in mold and tool construction, in the automotive and supply sectors and in the aerospace industry, for example, with efficient cutting solutions for deep drilling. The new, universal VHM-Deepmax deep-hole drills (15xD to 30xD) completely replace the previous Inovatools range for deep-hole drilling and guarantee effective guidance, fast and reliable removal of chips, a long service life for the tool, and ultimately first-class hole quality even at greater drilling depths thanks to a whole host of design benefits.
From its production site in Bavaria, Inovatools delivers high-quality cutting tools. There, the tool specialists use choice, tough, extremely fine-grain carbides that ensure a long service life and breaking strength for the drills. Tobias Eckerle, product manager at Inovatools, says, “Long-standing business relationships with the raw material suppliers is a prerequisite for the consistent quality of the substrate. Furthermore, the very latest technology for grinding, in-house coating and measuring guarantees high-performance, durable tools with extremely precise grinding, top surface quality and tight tolerances.”
Besides other factors, the high performance of the Deepmax with a drilling diameter of h7 is based on the geometry that has been adapted for this special drilling process and guarantees optimal chip removal for this application. To achieve this, Inovatools relies on a special polishing technique, for example, that makes the specially developed chip grooves with a wide cross-section extremely smooth. The front geometry with a 135° point angle is necessary for optimal centering of the drill, ensures ideal chip-breaking and low cutting forces and supports quiet operation.
Four lands that support and stabilize the drill in the axial direction enable precise and vibration-free drilling with extremely low deviation from center. As a result, Deepmax delivers superb hole quality even with oblique outlets and cross-drilled holes.
The very smooth Varacon high-performance coating that was specially developed for the application aids in fast chip flow and ensures a long tool service life. Eckerle comments, “We are also using a newly developed process for edge preparation in order to optimize and stabilize the cutting edges precisely for the machining challenges of the deep-drilling process. The special design of the Deepmax drills keeps cutting forces low, makes for smooth running, ensures optimum breaking and removal of chips and maximizes service life. No chip removal is necessary right up to 30xD.”
DEEPMAX deep-hole drills demonstrate their performance in comparative tests. When drilling into 42CrMo4 tempering steel (25xD – diameter 3.00), a conventional deep-hole drill on the market reached a tool life of 60 meters with pronounced wear marks, while the Deepmax managed a tool life of 75 meters with normal wear. The comparison with 30xD (diameter 6.00) passed off in similar fashion, with the Deepmax achieving a tool life of 65 meters with normal wear, while a comparison tool managed a tool life of 58 meters with pronounced wear marks.
Inovatools is offering the new Deepmax tools in 15xD, 20xD, 25xD (all up to 12 mm in diameter) and 30xD (up to 10 mm in diameter), which will all be available from stock. Inovatools is also making the centering and pilot drills as well as fiber end mills necessary for creating a precise, preparatory pilot hole available to the user. According to Eckerle, “Deep holes made with our Deepmax tools are set apart by high process reliability and outstanding hole surface quality. If necessary, the user can obtain technical guidance on drilling pilot holes as well as on the use and application-focused cutting parameters of the Deepmax deep-hole drills in a personal consultation, or alternatively, through our Inotech data sheet and Inocut cutting data apps via our website at www.invotaools.eu, for example.”
Contact Details
Related Glossary Terms
- centering
centering
1. Process of locating the center of a workpiece to be mounted on centers. 2. Process of mounting the workpiece concentric to the machine spindle. See centers.
- drilling tool ( drill or drill bit)
drilling tool ( drill or drill bit)
End-cutting tool for drilling. Tool has shank, body and angled face with cutting edges that drill the hole. Drills range in size from “microdrills” a few thousandths of an inch in diameter up to spade drills, which may cut holes several inches in diameter. Drills may have tapered shanks with a driving tang and fit directly into a spindle or adapter, or they may have straight shanks and be chuck-mounted. The rake angle varies with the material drilled. Styles include twist drills, straight-flute drills, half-round and flat drills, oil-hole drills, indexable drills and specials.
- edge preparation
edge preparation
Conditioning of the cutting edge, such as a honing or chamfering, to make it stronger and less susceptible to chipping. A chamfer is a bevel on the tool’s cutting edge; the angle is measured from the cutting face downward and generally varies from 25° to 45°. Honing is the process of rounding or blunting the cutting edge with abrasives, either manually or mechanically.
- grinding
grinding
Machining operation in which material is removed from the workpiece by a powered abrasive wheel, stone, belt, paste, sheet, compound, slurry, etc. Takes various forms: surface grinding (creates flat and/or squared surfaces); cylindrical grinding (for external cylindrical and tapered shapes, fillets, undercuts, etc.); centerless grinding; chamfering; thread and form grinding; tool and cutter grinding; offhand grinding; lapping and polishing (grinding with extremely fine grits to create ultrasmooth surfaces); honing; and disc grinding.
- metalworking
metalworking
Any manufacturing process in which metal is processed or machined such that the workpiece is given a new shape. Broadly defined, the term includes processes such as design and layout, heat-treating, material handling and inspection.
- point angle
point angle
Included angle at the point of a twist drill or similar tool; for general-purpose tools, the point angle is typically 118°.
- polishing
polishing
Abrasive process that improves surface finish and blends contours. Abrasive particles attached to a flexible backing abrade the workpiece.
- tempering
tempering
1. In heat-treatment, reheating hardened steel or hardened cast iron to a given temperature below the eutectoid temperature to decrease hardness and increase toughness. The process also is sometimes applied to normalized steel. 2. In nonferrous alloys and in some ferrous alloys (steels that cannot be hardened by heat-treatment), the hardness and strength produced by mechanical or thermal treatment, or both, and characterized by a certain structure, mechanical properties or reduction in area during cold working.