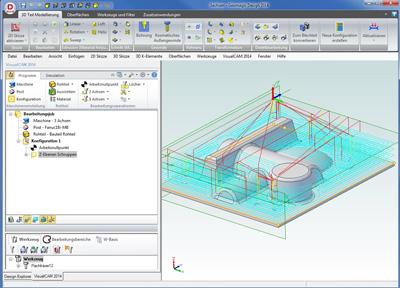
MecSoft Europe GmbH has announced the availability of VisualCAM 2014 for Geomagic, a major version release for MecSoft's integrated CAM solution for 3D Systems' CAD software, Geomagic Design (formerly Alibre).
VisualCAM 2014 for Geomagic includes two CAM modules, MILL and TURN, each of which run integrated inside the Geomagic CAD program and can be bought and licensed independent of each other. The TURN module is a new module that is being introduced with the 2014 release. The MILL module was significantly enhanced and improved in this 2014 release to provide customers with a powerful and complete manufacturing platform.
"This is an important release for MecSoft, in that it features a brand new TURN module and also a greatly improved MILL module. With this new functionality together with the seamless integration inside Geomagic Design, we continue to provide leading edge manufacturing capabilities for Geomagic Design users worldwide," stated Joe Anand, President and CEO of MecSoft Corp.
"We are pleased to offer VisualCAM 2014 for Geomagic in Europe," said Ulrich Oehler, CEO MecSoft Europe. "VisualCAM for Geomagic includes 2-½-, 3-, 4- and 5-axis milling. With this new release turning operations can be performed in the well-known Geomagic user interface. It comes with hundreds of free post-processors as well as a post-processor generator to create user definable post-processors. It is just powerful, easy to use and above all affordable."
Contact Details
Related Glossary Terms
- computer-aided design ( CAD)
computer-aided design ( CAD)
Product-design functions performed with the help of computers and special software.
- computer-aided manufacturing ( CAM)
computer-aided manufacturing ( CAM)
Use of computers to control machining and manufacturing processes.
- gang cutting ( milling)
gang cutting ( milling)
Machining with several cutters mounted on a single arbor, generally for simultaneous cutting.
- milling
milling
Machining operation in which metal or other material is removed by applying power to a rotating cutter. In vertical milling, the cutting tool is mounted vertically on the spindle. In horizontal milling, the cutting tool is mounted horizontally, either directly on the spindle or on an arbor. Horizontal milling is further broken down into conventional milling, where the cutter rotates opposite the direction of feed, or “up” into the workpiece; and climb milling, where the cutter rotates in the direction of feed, or “down” into the workpiece. Milling operations include plane or surface milling, endmilling, facemilling, angle milling, form milling and profiling.
- milling machine ( mill)
milling machine ( mill)
Runs endmills and arbor-mounted milling cutters. Features include a head with a spindle that drives the cutters; a column, knee and table that provide motion in the three Cartesian axes; and a base that supports the components and houses the cutting-fluid pump and reservoir. The work is mounted on the table and fed into the rotating cutter or endmill to accomplish the milling steps; vertical milling machines also feed endmills into the work by means of a spindle-mounted quill. Models range from small manual machines to big bed-type and duplex mills. All take one of three basic forms: vertical, horizontal or convertible horizontal/vertical. Vertical machines may be knee-type (the table is mounted on a knee that can be elevated) or bed-type (the table is securely supported and only moves horizontally). In general, horizontal machines are bigger and more powerful, while vertical machines are lighter but more versatile and easier to set up and operate.
- turning
turning
Workpiece is held in a chuck, mounted on a face plate or secured between centers and rotated while a cutting tool, normally a single-point tool, is fed into it along its periphery or across its end or face. Takes the form of straight turning (cutting along the periphery of the workpiece); taper turning (creating a taper); step turning (turning different-size diameters on the same work); chamfering (beveling an edge or shoulder); facing (cutting on an end); turning threads (usually external but can be internal); roughing (high-volume metal removal); and finishing (final light cuts). Performed on lathes, turning centers, chucking machines, automatic screw machines and similar machines.