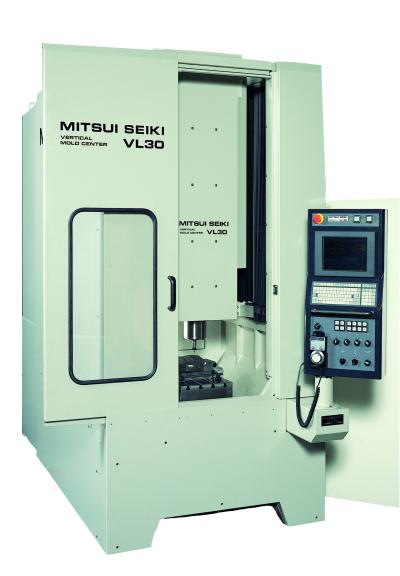
The Mitsui Seiki VL30 Series high-speed vertical machining centers were developed specifically for high-speed / high-precision hard milling of mold components as well as graphite and copper tungsten electrodes. The VL30 Series features high thrust, high-efficiency linear motor drives for the X, Y and Z axes for machining hardened tool steel alloy components. The 5-axis versions use Direct Drive rotary axes for smooth and perfectly controlled complex contouring. Delivering up to 1,574 ipm cutting feed rate with 1G acceleration/deceleration, it provides superior speed and motion control in performing high-speed point milling in multi-axis contouring applications. For accuracy, the precision glass scale feedback system detects 0.1micron increments.
The VL30 line has a proven track record of machining high-precision mold inserts for a wide variety of applications for medical, packaging, industrial, and aerospace applications for demanding manufacturers.The upgraded offerings include advanced features for process automation, work piece and tool handling, and the latest Fanuc 31i-B with i-HMI operator interface making it easier than ever before to realize improved output and profitability. The latest Graphite Package option allows customers to machine completely dry with no risk of electrode contamination or premature machine wear. All versions allow simple integration with robotics and in-process part inspection.
Available in three models, the VL 30-5X five-axis machining center, and VL 30, and larger VL 50 3-axis versions, this series features a 15 hp 50,000 rpm spindle accepting HSK E25 tooling for precise roughing and ultra-fine finishing. An integrated tool changer holds up to 90 tools.
Specifications include 7.9 in. x 11.8 in. x 7.9 in. X, Y, Z axis travels, 11.8 in. x 15.8 in. table size and a compact 53 in. x 128 in. footprint.
Enhanced production features include a 4-point leveling bed, F.E.A. (finite element analysis)-designed main components, hand-scraped castings for excellent machine geometry and superior chip and dust evacuation with a choice of solution to suit most needs.
Contact Details
Related Glossary Terms
- centers
centers
Cone-shaped pins that support a workpiece by one or two ends during machining. The centers fit into holes drilled in the workpiece ends. Centers that turn with the workpiece are called “live” centers; those that do not are called “dead” centers.
- feed
feed
Rate of change of position of the tool as a whole, relative to the workpiece while cutting.
- gang cutting ( milling)
gang cutting ( milling)
Machining with several cutters mounted on a single arbor, generally for simultaneous cutting.
- inches per minute ( ipm)
inches per minute ( ipm)
Value that refers to how far the workpiece or cutter advances linearly in 1 minute, defined as: ipm = ipt 5 number of effective teeth 5 rpm. Also known as the table feed or machine feed.
- linear motor
linear motor
Functionally the same as a rotary motor in a machine tool, a linear motor can be thought of as a standard permanent-magnet, rotary-style motor slit axially to the center and then peeled back and laid flat. The major advantage of using a linear motor to drive the axis motion is that it eliminates the inefficiency and mechanical variance caused by the ballscrew assembly system used in most CNC machines.
- machining center
machining center
CNC machine tool capable of drilling, reaming, tapping, milling and boring. Normally comes with an automatic toolchanger. See automatic toolchanger.
- milling
milling
Machining operation in which metal or other material is removed by applying power to a rotating cutter. In vertical milling, the cutting tool is mounted vertically on the spindle. In horizontal milling, the cutting tool is mounted horizontally, either directly on the spindle or on an arbor. Horizontal milling is further broken down into conventional milling, where the cutter rotates opposite the direction of feed, or “up” into the workpiece; and climb milling, where the cutter rotates in the direction of feed, or “down” into the workpiece. Milling operations include plane or surface milling, endmilling, facemilling, angle milling, form milling and profiling.
- robotics
robotics
Discipline involving self-actuating and self-operating devices. Robots frequently imitate human capabilities, including the ability to manipulate physical objects while evaluating and reacting appropriately to various stimuli. See industrial robot; robot.