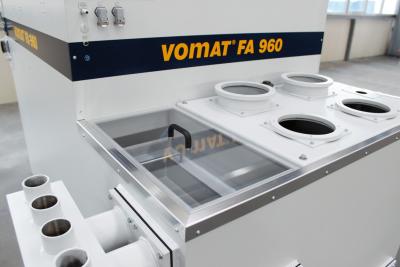
Finely filtered grinding oils in cutting tool manufacturing are an important key to more quality and efficiency in production. Tool manufacturers who rely on the right technology and competence of their fine filtration equipment manufacturer make optimal use of the many advantages offered by efficient grinding oil filtration.
Metal abrasion, dirt and decomposing materials due to thermal influences contaminate grinding oils during the manufacturing of precision tools. The fluids could not be used for long periods without high performance ultrafine filtration. Temperature and foreign particles would compromise process reliability and quality. For this reason, ultrafine filtration plays a key role in the overall machining process for tool manufacturers in terms of cost and quality, as do premium quality blanks, state-of-the-art grinding technology and high-precision grinding wheels.
Vomat, Treuen, Germany, specializes in filtration, and Steffen Strobel, the company's technical sales manager, says, "Filtered grinding oils are an important component in the value chain and should therefore not be underestimated. The longer the finely filtered grinding oil can remain in the system in almost fresh oil quality, the more benefits the tool manufacturer will gain in respect to increased quality and reduced costs."
For example, the fewer particles in circulation, the lower the abrasion of the grinding wheel during tool grinding. The grinding tools last longer and more drills or cutters can be ground with one disc. In addition, the downtimes of machines are reduced because the grinding wheels and the grinding oil does not have to be changed as often.
Strobel said: "With Vomat technology, the tool manufacturer is on the safe side. Because our high-quality pre-coat filters, operate in full flow filtration and separate the dirty and clean grinding oil 100 percent. This provides nearly fresh oil quality in the 3 to 5 µm range (Nas 7) over a very long period of time. Long service life of grinding wheels as well as high process reliability, and operational stability of the entire manufacturing system are the rewards. In addition, the tool manufacturer saves grinding oil costs and minimizes drag-out losses thanks to innovative technology."
Depending on production requirements, Vomat supplies stand-alone filtration systems, as well as large industrial central systems, and integrates them precisely into the respective production workflow. Different filter, cooling and disposal technologies ensure economic and ecological success and harmony.
One example is the Vomat FA 960 (dimensions: 2500mm L x 1400mm W x 1500mm W), with an oil capacity of approximately 2,400 liters and 960 liters/minute filtration capacity. Depending on the amount of dirt, the high-performance filters are automatically back-washed as required, which has a positive effect on the filter durability and the energy usage. The high-precision temperature controls guarantee +/-2 K accuracy, which guarantees that the medium has a long service life. It also prevents temperature related expansion of machine components and the workpieces to be ground. In addition, there is an intelligent, fully automatic recycling system for the carbide sludge, which has a residual moisture content of around 5 to 10 percent: The patented “Sedimentator” disposes the sludge directly into a disposable transport container ready to be picked-up by the recycling companies.
Strobel said: "Tool manufacturers are confronted with the high quality demands in today’s markets. Drills, milling cutters, reamers and threading tools, etc. must be manufactured within extremely narrow tolerances. Optimally filtered grinding oils are an important mosaic piece in the overall manufacturing process and contribute to the fact that high quality micro to extra - large dimension tools can be ground economically."
Contact Details
Related Glossary Terms
- gang cutting ( milling)
gang cutting ( milling)
Machining with several cutters mounted on a single arbor, generally for simultaneous cutting.
- grinding
grinding
Machining operation in which material is removed from the workpiece by a powered abrasive wheel, stone, belt, paste, sheet, compound, slurry, etc. Takes various forms: surface grinding (creates flat and/or squared surfaces); cylindrical grinding (for external cylindrical and tapered shapes, fillets, undercuts, etc.); centerless grinding; chamfering; thread and form grinding; tool and cutter grinding; offhand grinding; lapping and polishing (grinding with extremely fine grits to create ultrasmooth surfaces); honing; and disc grinding.
- grinding wheel
grinding wheel
Wheel formed from abrasive material mixed in a suitable matrix. Takes a variety of shapes but falls into two basic categories: one that cuts on its periphery, as in reciprocating grinding, and one that cuts on its side or face, as in tool and cutter grinding.
- milling
milling
Machining operation in which metal or other material is removed by applying power to a rotating cutter. In vertical milling, the cutting tool is mounted vertically on the spindle. In horizontal milling, the cutting tool is mounted horizontally, either directly on the spindle or on an arbor. Horizontal milling is further broken down into conventional milling, where the cutter rotates opposite the direction of feed, or “up” into the workpiece; and climb milling, where the cutter rotates in the direction of feed, or “down” into the workpiece. Milling operations include plane or surface milling, endmilling, facemilling, angle milling, form milling and profiling.
- threading
threading
Process of both external (e.g., thread milling) and internal (e.g., tapping, thread milling) cutting, turning and rolling of threads into particular material. Standardized specifications are available to determine the desired results of the threading process. Numerous thread-series designations are written for specific applications. Threading often is performed on a lathe. Specifications such as thread height are critical in determining the strength of the threads. The material used is taken into consideration in determining the expected results of any particular application for that threaded piece. In external threading, a calculated depth is required as well as a particular angle to the cut. To perform internal threading, the exact diameter to bore the hole is critical before threading. The threads are distinguished from one another by the amount of tolerance and/or allowance that is specified. See turning.