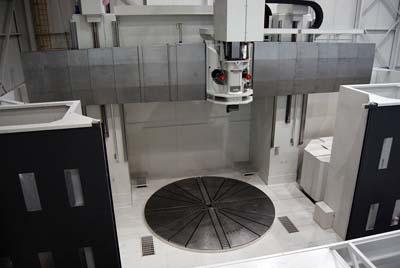
MAG IAS LLC shipped its first VTC 5000 to a U.S. manufacturer of power generation equipment. Available with 5m, 6m, 7m and 8m hydrostatic tables, the initial machine's 5m table supports up to 330,000 lbs. while turning parts at up to 75 rpm. The 7m and 8m models each have a load capacity of 550,000 lbs.
"North American manufacturers in the nuclear and wind energy, mining and construction industries are all scaling up their equipment. We are taking our product development in the same direction," said Helene Nimmer, director of proposals and product management for MAG. "The major components of our large VTCs weigh in excess of 50,000 lbs. each and can be more than 48' long. As a U.S. builder of these supersize machines, we can reduce customer lead time and simplify logistics."
The pictured adjustable-rail model offers a cross rail that is both an infinitely-variable-positioning axis and a machining axis. The X/Z traverse rate is 787 ipm, and the rail-elevating rate is 78 ipm. Full X-axis travel right and left of center allows machining from both sides and accommodates probing of diameters. W-axis machining improves part geometries, and the hydrostatic ram's high dynamic stiffness allows heavy cuts and provides the ability to impart fine surface finishes, according to the company.
The VTC 5000 has a modular design, allowing various combinations of standard modules to tailor it to specific applications. It can be equipped with an optional live spindle for grinding, milling, drilling and tapping, as well as a C-axis for contouring.
Contact Details
Related Glossary Terms
- dynamic stiffness
dynamic stiffness
Measure of a machining system’s ability to dampen vibration from a forced input. If the dynamic stiffness of a system is not sufficient to dampen vibration, chatter occurs. See static stiffness; stiffness.
- gang cutting ( milling)
gang cutting ( milling)
Machining with several cutters mounted on a single arbor, generally for simultaneous cutting.
- grinding
grinding
Machining operation in which material is removed from the workpiece by a powered abrasive wheel, stone, belt, paste, sheet, compound, slurry, etc. Takes various forms: surface grinding (creates flat and/or squared surfaces); cylindrical grinding (for external cylindrical and tapered shapes, fillets, undercuts, etc.); centerless grinding; chamfering; thread and form grinding; tool and cutter grinding; offhand grinding; lapping and polishing (grinding with extremely fine grits to create ultrasmooth surfaces); honing; and disc grinding.
- inches per minute ( ipm)
inches per minute ( ipm)
Value that refers to how far the workpiece or cutter advances linearly in 1 minute, defined as: ipm = ipt 5 number of effective teeth 5 rpm. Also known as the table feed or machine feed.
- milling
milling
Machining operation in which metal or other material is removed by applying power to a rotating cutter. In vertical milling, the cutting tool is mounted vertically on the spindle. In horizontal milling, the cutting tool is mounted horizontally, either directly on the spindle or on an arbor. Horizontal milling is further broken down into conventional milling, where the cutter rotates opposite the direction of feed, or “up” into the workpiece; and climb milling, where the cutter rotates in the direction of feed, or “down” into the workpiece. Milling operations include plane or surface milling, endmilling, facemilling, angle milling, form milling and profiling.
- modular design ( modular construction)
modular design ( modular construction)
Manufacturing of a product in subassemblies that permits fast and simple replacement of defective assemblies and tailoring of the product for different purposes. See interchangeable parts.
- stiffness
stiffness
1. Ability of a material or part to resist elastic deflection. 2. The rate of stress with respect to strain; the greater the stress required to produce a given strain, the stiffer the material is said to be. See dynamic stiffness; static stiffness.
- tapping
tapping
Machining operation in which a tap, with teeth on its periphery, cuts internal threads in a predrilled hole having a smaller diameter than the tap diameter. Threads are formed by a combined rotary and axial-relative motion between tap and workpiece. See tap.
- turning
turning
Workpiece is held in a chuck, mounted on a face plate or secured between centers and rotated while a cutting tool, normally a single-point tool, is fed into it along its periphery or across its end or face. Takes the form of straight turning (cutting along the periphery of the workpiece); taper turning (creating a taper); step turning (turning different-size diameters on the same work); chamfering (beveling an edge or shoulder); facing (cutting on an end); turning threads (usually external but can be internal); roughing (high-volume metal removal); and finishing (final light cuts). Performed on lathes, turning centers, chucking machines, automatic screw machines and similar machines.