Contact Details
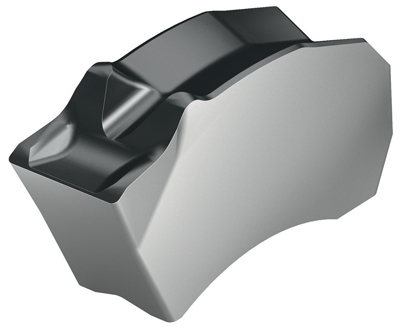
Walter USA LLC has introduced the Walter Cut SX grooving and parting system, a flexible new approach for both turning and milling operations that reportedly brings higher levels of reliability, productivity, and tool life to these crucial operations. The key to the system's performance is its innovative design featuring self-clamping, single edge grooving inserts with positive-locking integration in the tool insert seat. The locking action is made possible by the unique curved shape of the inserts. Positive locking keeps the inserts secure and accurately seated when subjected to heavy load in the feed direction.
The new self-locking system's top clamp produces high retaining forces without hindering the chip flow. It fixes the insert in the seat, which takes the form of a prism for precise insert location. In addition, the seat also has a contact surface at the back for supporting the insert. As a result, the cutting forces are transferred into the fixed part of the tool. This distribution of force guarantees excellent process reliability and enables an increase in productivity due to higher cutting parameters. The Walter Cut system employs a straight coolant outlet resulting in no spray effect. In addition, a special key for changing the insert allows replacement in just one simple and rapid operation.
Walter supplies these new grooving inserts in the tough, proven Tiger-tec Silver PVD cutting material grades WSM33S and WSM43S for steel, stainless steel and difficult to machine materials. Currently there are three geometries to choose from: The universal CE4 geometry with tough cutting edge for medium to high feed rates, the positive CF5 geometry for long-chipping materials and medium feed rates, and the sharp CF6 geometry for small diameters or thin-walled tubes and low feed rates. All grooving inserts can be supplied in insert widths from 2.0 to 6.0mm.
Related Glossary Terms
- coolant
coolant
Fluid that reduces temperature buildup at the tool/workpiece interface during machining. Normally takes the form of a liquid such as soluble or chemical mixtures (semisynthetic, synthetic) but can be pressurized air or other gas. Because of water’s ability to absorb great quantities of heat, it is widely used as a coolant and vehicle for various cutting compounds, with the water-to-compound ratio varying with the machining task. See cutting fluid; semisynthetic cutting fluid; soluble-oil cutting fluid; synthetic cutting fluid.
- feed
feed
Rate of change of position of the tool as a whole, relative to the workpiece while cutting.
- gang cutting ( milling)
gang cutting ( milling)
Machining with several cutters mounted on a single arbor, generally for simultaneous cutting.
- grooving
grooving
Machining grooves and shallow channels. Example: grooving ball-bearing raceways. Typically performed by tools that are capable of light cuts at high feed rates. Imparts high-quality finish.
- milling
milling
Machining operation in which metal or other material is removed by applying power to a rotating cutter. In vertical milling, the cutting tool is mounted vertically on the spindle. In horizontal milling, the cutting tool is mounted horizontally, either directly on the spindle or on an arbor. Horizontal milling is further broken down into conventional milling, where the cutter rotates opposite the direction of feed, or “up” into the workpiece; and climb milling, where the cutter rotates in the direction of feed, or “down” into the workpiece. Milling operations include plane or surface milling, endmilling, facemilling, angle milling, form milling and profiling.
- parting
parting
When used in lathe or screw-machine operations, this process separates a completed part from chuck-held or collet-fed stock by means of a very narrow, flat-end cutting, or parting, tool.
- physical vapor deposition ( PVD)
physical vapor deposition ( PVD)
Tool-coating process performed at low temperature (500° C), compared to chemical vapor deposition (1,000° C). Employs electric field to generate necessary heat for depositing coating on a tool’s surface. See CVD, chemical vapor deposition.
- turning
turning
Workpiece is held in a chuck, mounted on a face plate or secured between centers and rotated while a cutting tool, normally a single-point tool, is fed into it along its periphery or across its end or face. Takes the form of straight turning (cutting along the periphery of the workpiece); taper turning (creating a taper); step turning (turning different-size diameters on the same work); chamfering (beveling an edge or shoulder); facing (cutting on an end); turning threads (usually external but can be internal); roughing (high-volume metal removal); and finishing (final light cuts). Performed on lathes, turning centers, chucking machines, automatic screw machines and similar machines.