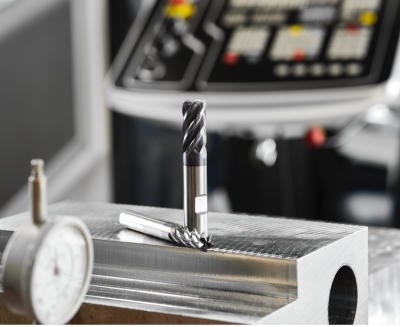
WIDIATM has expanded the capabilities of its bestselling WCE solid end milling series with a 5-flute geometry specifically designed for optimal performance when shoulder milling and side milling carbon, stainless steel and cast iron. The WCE5 solid end mill combines the unequal index feature with an elevated 38-degree helix to deliver unparalleled machining performance.
The 5-flute square-end end mill with sharp edges, chamfers and corner radii joins a 4-flute square-end and ball-nose end mill with both straight and Weldon® shanks as part of WIDIA’s WCE solid end mill portfolio. The WCE4, a 4-flute geometry solid end mill, combines the asymmetrical index and variable helix features to excel in operations like full slots and heavy cuts.
“Our customers look to WIDIA for solutions that prolong tool life and get the job done,” said Tamir Sherif, WIDIA Solid End Milling Global Portfolio Manager. “With WIDIA’s WCE5, we’re giving them a tool that delivers reliable performance for side and shoulder milling, as well as helical and dynamic milling. It is the next gen solution for versatility and expands on the overall performance and capabilities of WIDIA’s trusted WCE platform.”
Other benefits of WIDIA’s WCE solid end mill series include:
- Faceted and eccentric relief to provide vibration dampening
- Core taper to improve chip evacuation
Universal grade (WU20PD) to perform in steel, stainless-steel and cast-iron material
Both the WCE4 and WCE5 solid end mill series are available in inch and metric measurement systems. WCE5 launches less than a year after the release of WCE4.
The WCE solid end mill portfolio is available through WIDIA authorized distributers.
Contact Details
Related Glossary Terms
- gang cutting ( milling)
gang cutting ( milling)
Machining with several cutters mounted on a single arbor, generally for simultaneous cutting.
- milling
milling
Machining operation in which metal or other material is removed by applying power to a rotating cutter. In vertical milling, the cutting tool is mounted vertically on the spindle. In horizontal milling, the cutting tool is mounted horizontally, either directly on the spindle or on an arbor. Horizontal milling is further broken down into conventional milling, where the cutter rotates opposite the direction of feed, or “up” into the workpiece; and climb milling, where the cutter rotates in the direction of feed, or “down” into the workpiece. Milling operations include plane or surface milling, endmilling, facemilling, angle milling, form milling and profiling.
- milling machine ( mill)
milling machine ( mill)
Runs endmills and arbor-mounted milling cutters. Features include a head with a spindle that drives the cutters; a column, knee and table that provide motion in the three Cartesian axes; and a base that supports the components and houses the cutting-fluid pump and reservoir. The work is mounted on the table and fed into the rotating cutter or endmill to accomplish the milling steps; vertical milling machines also feed endmills into the work by means of a spindle-mounted quill. Models range from small manual machines to big bed-type and duplex mills. All take one of three basic forms: vertical, horizontal or convertible horizontal/vertical. Vertical machines may be knee-type (the table is mounted on a knee that can be elevated) or bed-type (the table is securely supported and only moves horizontally). In general, horizontal machines are bigger and more powerful, while vertical machines are lighter but more versatile and easier to set up and operate.
- relief
relief
Space provided behind the cutting edges to prevent rubbing. Sometimes called primary relief. Secondary relief provides additional space behind primary relief. Relief on end teeth is axial relief; relief on side teeth is peripheral relief.