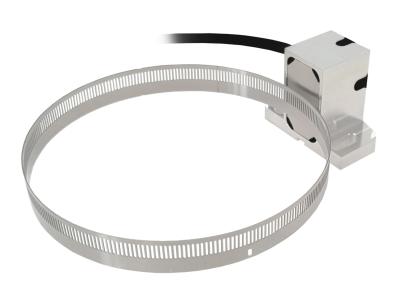
The new WMK 3010S rotational speed sensor from AMO is now available, and provides users of milling and turning machines a better option for operation of their main spindle. Besides providing speed data, the WMK 3010S also supports the capturing of operating status data of that spindle thus optimizing many costs related to the operation of the machine.
Available in North America through parent company HEIDENHAIN, this new AMO speed sensor includes a USB interface which allows the operating status of the spindle to output to the machine control. This enables the user to record rotational speed, operating time, temperature and more. Put these factors together, and overall performance and uptime expectations are optimized.
The rugged, inductive, incremental scanning head on the WMK 3010S is available with a 1Vpp interface. It has a minimalist modular design, allowing this IP67-rated product to be installed in existing customer designs without significant modifications. It is available in the common industry line count increments and can be operated up to a max of 50,000 rpm.
Many useful features are offered in the WMK 3010S including:
- Inductive Scanning
- IP67 protection
- Max speed of 50,000 rpm
- Integrated acquisition of operational data
- Offline output of data via USB
- Low Cost
Contact Details
Related Glossary Terms
- gang cutting ( milling)
gang cutting ( milling)
Machining with several cutters mounted on a single arbor, generally for simultaneous cutting.
- milling
milling
Machining operation in which metal or other material is removed by applying power to a rotating cutter. In vertical milling, the cutting tool is mounted vertically on the spindle. In horizontal milling, the cutting tool is mounted horizontally, either directly on the spindle or on an arbor. Horizontal milling is further broken down into conventional milling, where the cutter rotates opposite the direction of feed, or “up” into the workpiece; and climb milling, where the cutter rotates in the direction of feed, or “down” into the workpiece. Milling operations include plane or surface milling, endmilling, facemilling, angle milling, form milling and profiling.
- modular design ( modular construction)
modular design ( modular construction)
Manufacturing of a product in subassemblies that permits fast and simple replacement of defective assemblies and tailoring of the product for different purposes. See interchangeable parts.
- turning
turning
Workpiece is held in a chuck, mounted on a face plate or secured between centers and rotated while a cutting tool, normally a single-point tool, is fed into it along its periphery or across its end or face. Takes the form of straight turning (cutting along the periphery of the workpiece); taper turning (creating a taper); step turning (turning different-size diameters on the same work); chamfering (beveling an edge or shoulder); facing (cutting on an end); turning threads (usually external but can be internal); roughing (high-volume metal removal); and finishing (final light cuts). Performed on lathes, turning centers, chucking machines, automatic screw machines and similar machines.