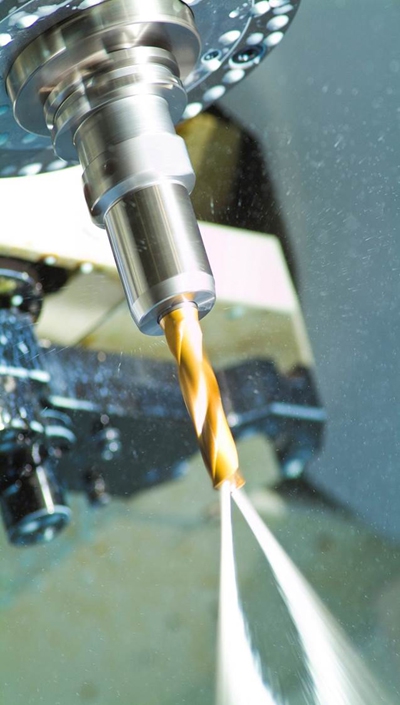
BTM Corp., a Michigan-based manufacturer of clinch joining systems, automation components and contract machine work, has reported substantial savings in coolant usage and waste removal costs after switching its aluminum and steel machining operations to run on QualiChem XTREME CUT 251C semi-synthetic metalworking fluid.
Michigan Petroleum Technologies, QualiChem's distributor in lower Michigan, oversaw the 6-month trials in which BTM compared XTREME CUT 251C against the fluids it had been using.
"The results of the trials on four machines spoke for themselves," said Richard Seim, executive vice president of Michigan Petroleum Technologies. "Coolant usage and waste removal costs were down 50 percent, and machine operators reported total elimination of noxious odors. Altogether, the total documented hard savings resulting from reduced coolant usage and waste removal costs added up to more than $47,000 in 2013."
Dave Lamb, BTM manufacturing manager, said: "BTM has an intensive coolant maintenance program and Michigan Petroleum stated that we should be able to lower consumption and the maintenance cost using QualiChem XTREME CUT 251C. We tested several coolants and found that Michigan Petroleum was correct. We lowered our coolant consumption, maintenance cost, and waste coolant disposal cost using XTREME CUT 251C."
"I like the cleanliness, clarity and machinability of the QualiChem XTREME CUT 251C," said Tony Weber, BTM milling supervisor. "There is minimal maintenance and operator acceptance has been excellent."
Dick Kleinknecht, lathe supervisor at BTM, said, "I've experienced excellent results with XTREME CUT 251C. The product does not have an undesirable odor and is very easy to maintain."
"At QualiChem, our strategy for success is dependent on our superior technology and outstanding distributors like Michigan Petroleum Technologies," said Mike Forest, director of metalworking at QualiChem.
"They brought to the table a deep understanding of their customer's needs and challenges, combined with their technical expertise and knowledge of QualiChem's product lines. The result is a solution that dramatically reduces BTM's operating costs, extends tool life, produces cleaner finished products and improves operator satisfaction on the job."
Contact Details
Related Glossary Terms
- coolant
coolant
Fluid that reduces temperature buildup at the tool/workpiece interface during machining. Normally takes the form of a liquid such as soluble or chemical mixtures (semisynthetic, synthetic) but can be pressurized air or other gas. Because of water’s ability to absorb great quantities of heat, it is widely used as a coolant and vehicle for various cutting compounds, with the water-to-compound ratio varying with the machining task. See cutting fluid; semisynthetic cutting fluid; soluble-oil cutting fluid; synthetic cutting fluid.
- gang cutting ( milling)
gang cutting ( milling)
Machining with several cutters mounted on a single arbor, generally for simultaneous cutting.
- lathe
lathe
Turning machine capable of sawing, milling, grinding, gear-cutting, drilling, reaming, boring, threading, facing, chamfering, grooving, knurling, spinning, parting, necking, taper-cutting, and cam- and eccentric-cutting, as well as step- and straight-turning. Comes in a variety of forms, ranging from manual to semiautomatic to fully automatic, with major types being engine lathes, turning and contouring lathes, turret lathes and numerical-control lathes. The engine lathe consists of a headstock and spindle, tailstock, bed, carriage (complete with apron) and cross slides. Features include gear- (speed) and feed-selector levers, toolpost, compound rest, lead screw and reversing lead screw, threading dial and rapid-traverse lever. Special lathe types include through-the-spindle, camshaft and crankshaft, brake drum and rotor, spinning and gun-barrel machines. Toolroom and bench lathes are used for precision work; the former for tool-and-die work and similar tasks, the latter for small workpieces (instruments, watches), normally without a power feed. Models are typically designated according to their “swing,” or the largest-diameter workpiece that can be rotated; bed length, or the distance between centers; and horsepower generated. See turning machine.
- machinability
machinability
The relative ease of machining metals and alloys.
- metalworking
metalworking
Any manufacturing process in which metal is processed or machined such that the workpiece is given a new shape. Broadly defined, the term includes processes such as design and layout, heat-treating, material handling and inspection.
- milling
milling
Machining operation in which metal or other material is removed by applying power to a rotating cutter. In vertical milling, the cutting tool is mounted vertically on the spindle. In horizontal milling, the cutting tool is mounted horizontally, either directly on the spindle or on an arbor. Horizontal milling is further broken down into conventional milling, where the cutter rotates opposite the direction of feed, or “up” into the workpiece; and climb milling, where the cutter rotates in the direction of feed, or “down” into the workpiece. Milling operations include plane or surface milling, endmilling, facemilling, angle milling, form milling and profiling.