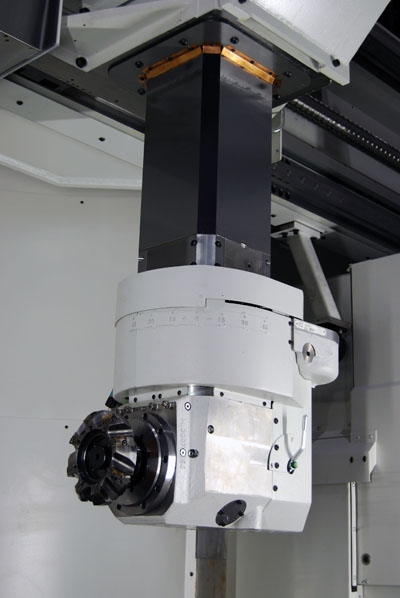
Fives brings off-centerline turning, drilling, milling and tapping capabilities to its Giddings & Lewis vertical turning centers with a new Y-axis attachment, that combines a C-axis head with table and X and Z axes motions. The attachment, available fully integrated on new VTCs or as a retrofit, allows for single-setup processing of flanged parts, pumps, compressors, motor housings, fluid routing parts, intakes and exhausts, among others.
"The Y-axis attachment is a powerful package, with a wide range of motion," said Pete Beyer, Director of Product Strategy and Development at Fives Giddings & Lewis. "Its power and torque are equal to our standard, heavy-duty right-angle heads, with no limits in cutting performance relative to speed. This is an affordable way to reduce setups and free up machine time on horizontal machining centers and boring mills that used to be required to produce these same features on turned parts."
The C-axis head provides +/-45 degrees rotation, creating a machining range of Y-axis features of +/- the VTC table radius. The continuous power 22-kW (29-hp) attachment has a maximum spindle speed of 2200 rpm, and continuous torque of 875 Nm (645 ft-lb), and can be loaded manually or automatically via the machine's automatic toolchanger. A live spindle accommodates standard Kennametal KM80 or Sandvik Coromant Capto C8 tooling. Coolant delivery via external nozzles on the face of the attachment or through-the-spindle coolant is provided.
The preloaded C-axis drive and high-stiffness roller bearings ensure accuracy, according to the company. The attachment's integrated measurement system allows for accurate machining of part features.
Contact Details
Related Glossary Terms
- automatic toolchanger
automatic toolchanger
Mechanism typically included in a machining center that, on the appropriate command, removes one cutting tool from the spindle nose and replaces it with another. The changer restores the used tool to the magazine and selects and withdraws the next desired tool from the storage magazine. The changer is controlled by a set of prerecorded/predetermined instructions associated with the part(s) to be produced.
- boring
boring
Enlarging a hole that already has been drilled or cored. Generally, it is an operation of truing the previously drilled hole with a single-point, lathe-type tool. Boring is essentially internal turning, in that usually a single-point cutting tool forms the internal shape. Some tools are available with two cutting edges to balance cutting forces.
- centers
centers
Cone-shaped pins that support a workpiece by one or two ends during machining. The centers fit into holes drilled in the workpiece ends. Centers that turn with the workpiece are called “live” centers; those that do not are called “dead” centers.
- coolant
coolant
Fluid that reduces temperature buildup at the tool/workpiece interface during machining. Normally takes the form of a liquid such as soluble or chemical mixtures (semisynthetic, synthetic) but can be pressurized air or other gas. Because of water’s ability to absorb great quantities of heat, it is widely used as a coolant and vehicle for various cutting compounds, with the water-to-compound ratio varying with the machining task. See cutting fluid; semisynthetic cutting fluid; soluble-oil cutting fluid; synthetic cutting fluid.
- gang cutting ( milling)
gang cutting ( milling)
Machining with several cutters mounted on a single arbor, generally for simultaneous cutting.
- milling
milling
Machining operation in which metal or other material is removed by applying power to a rotating cutter. In vertical milling, the cutting tool is mounted vertically on the spindle. In horizontal milling, the cutting tool is mounted horizontally, either directly on the spindle or on an arbor. Horizontal milling is further broken down into conventional milling, where the cutter rotates opposite the direction of feed, or “up” into the workpiece; and climb milling, where the cutter rotates in the direction of feed, or “down” into the workpiece. Milling operations include plane or surface milling, endmilling, facemilling, angle milling, form milling and profiling.
- tapping
tapping
Machining operation in which a tap, with teeth on its periphery, cuts internal threads in a predrilled hole having a smaller diameter than the tap diameter. Threads are formed by a combined rotary and axial-relative motion between tap and workpiece. See tap.
- toolchanger
toolchanger
Carriage or drum attached to a machining center that holds tools until needed; when a tool is needed, the toolchanger inserts the tool into the machine spindle. See automatic toolchanger.
- turning
turning
Workpiece is held in a chuck, mounted on a face plate or secured between centers and rotated while a cutting tool, normally a single-point tool, is fed into it along its periphery or across its end or face. Takes the form of straight turning (cutting along the periphery of the workpiece); taper turning (creating a taper); step turning (turning different-size diameters on the same work); chamfering (beveling an edge or shoulder); facing (cutting on an end); turning threads (usually external but can be internal); roughing (high-volume metal removal); and finishing (final light cuts). Performed on lathes, turning centers, chucking machines, automatic screw machines and similar machines.