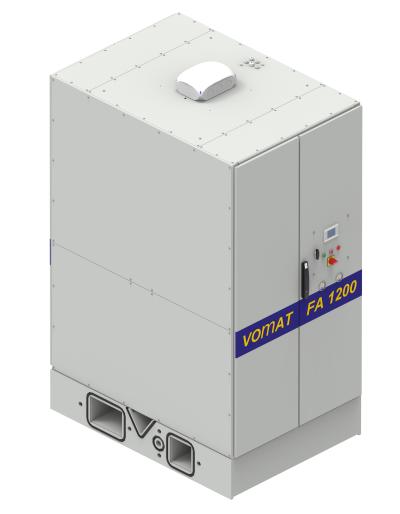
Extremely clean grinding oils are essential for economical, process-reliable and high-quality tool grinding. In this field, Vomat from Treuen offers not only individual compact filtration plants of the FA series but also extremely flexible central filtration plants (ZFA) to which several grinding machines are connected. The great advantage of these systems is that they consist of separate modules that can be flexibly combined with each other. Depending on the requirements of the particular system, Vomat provides the necessary components. If production requirements or capacities change, the system can be expanded with appropriate planning. In this way, maximum performance is achieved in various phases of production and company development, always perfectly adapted to the individual needs of the user.
Vomat is a renowned specialist for the ultrafine filtration of cooling lubricants in the metalworking industry. The wide product range includes solutions for single and central plants as well as customized special configurations with central and decentralized functions. Steffen Strobel, sales manager at Vomat, emphasizes, "Our central systems are optimal for the filtration of fine particles from oil, such as those produced during grinding, honing, lapping, eroding and other processes. In contrast to problematic bypass processes, our machines operate with precise, on-demand full-flow filtration using the backflush method. The automatic cycle is based on the amount of dirt. This means that dirty and clean oil are separated 100 percent. Thanks to our innovative backwashable high-performance precoat filters, costly filter aids are also unnecessary."
Flexible modular combination
Vomat ZFA central filter systems consist of separate modules. Their advantage is their combinability. The modules are assembled according to the customer's system requirements. The basic model for Vomat central filter systems is the ZFA 1200, whose filter unit has compact dimensions of 1200 x 1200 x 2200 mm (L x W x H). The filter fineness is 3-5 µm. Steffen Strobel: "Due to the special design features, clean oil in quality class NAS 7 is also available during backwashing."
The PLC-controlled cooling unit is designed according to the requirements of the production process. The control accuracy is up to +/- 0.2 K. Heat is dissipated via an external condenser. Optionally, Vomat also offers the possibility of cold water operation.
Vomat supplies energy-optimized machine supply pumps according to the performance of the machines. The customized system configuration ensures that the disposal volume is minimized and the drag-out loss is kept to a minimum. The disposal of recyclable materials takes place fully automatically via a sedimentator directly into the transport containers of recycling companies.
The central control takes over the linking of the modules and the control of external components such as machine supply pumps. In addition, the remote maintenance function via Remote Control enables remote monitoring and maintenance.
Steffen Strobel: "Vomat offers central large filter systems that are individually adapted to the respective production and can be scaled up in steps of 1200 liters. The diverse selection of modules and optional features allows maximum flexibility. Thanks to our new-generation ultra-fine filtration systems, cooling lubricants with a high degree of purification can remain in the system significantly longer than with conventional filter systems. This also increases the service life of the grinding wheels. Overall, maintenance and energy requirements are significantly reduced, and shortened machine downtimes further minimize production costs. The bottom line is resource-saving and profitable coolant filtration."
Contact Details
Related Glossary Terms
- coolant
coolant
Fluid that reduces temperature buildup at the tool/workpiece interface during machining. Normally takes the form of a liquid such as soluble or chemical mixtures (semisynthetic, synthetic) but can be pressurized air or other gas. Because of water’s ability to absorb great quantities of heat, it is widely used as a coolant and vehicle for various cutting compounds, with the water-to-compound ratio varying with the machining task. See cutting fluid; semisynthetic cutting fluid; soluble-oil cutting fluid; synthetic cutting fluid.
- grinding
grinding
Machining operation in which material is removed from the workpiece by a powered abrasive wheel, stone, belt, paste, sheet, compound, slurry, etc. Takes various forms: surface grinding (creates flat and/or squared surfaces); cylindrical grinding (for external cylindrical and tapered shapes, fillets, undercuts, etc.); centerless grinding; chamfering; thread and form grinding; tool and cutter grinding; offhand grinding; lapping and polishing (grinding with extremely fine grits to create ultrasmooth surfaces); honing; and disc grinding.
- lapping
lapping
Finishing operation in which a loose, fine-grain abrasive in a liquid medium abrades material. Extremely accurate process that corrects minor shape imperfections, refines surface finishes and produces a close fit between mating surfaces.
- metalworking
metalworking
Any manufacturing process in which metal is processed or machined such that the workpiece is given a new shape. Broadly defined, the term includes processes such as design and layout, heat-treating, material handling and inspection.