END USER: Mid Valley Industries LLC, (920) 759-0314, www.mvii.com.
CHALLENGE: Eliminate tool breakage when tapping stainless steel.
SOLUTION: A tap with a new multiple-layered coating and an advanced chamfer geometry, rake and flute form.
SOLUTION PROVIDER: Emuge Corp., (800) 323-3013, www.emuge.com.
Because tapping is often one of the final machining operations during part production, a broken tap that causes a part to be scrapped can be costly. Mid Valley Industries LLC found that out when tapping 316-L stainless steel parts for fluid-recovery applications in the oil and gas industry. The Kaukauna, Wis., contract manufacturer specializes in short runs of large parts made of various materials, including Inconel, Monel, Hastelloy, steel and aluminum.
CNC Programming Manager Chad Kluth explained that each of the oil-and-gas parts has a material cost of $1,700, requires threading 48 holes with a ¼-20 tap and features ground surfaces with a 32-rms finish. “If we damage any of those surfaces, we’re out of luck and that part could be unusable,” Kluth said. “There is no way to fix it short of weld repair.”
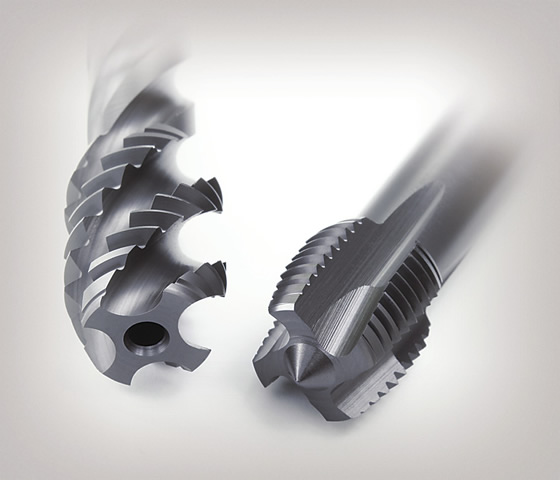
Emuge Z-Taps have a multilayer coating, which enables efficient chip evacuation.
In addition to tap breakage, the issue of tool life is often encountered when tapping. Kluth noted one of the taps the shop was applying typically didn’t last 10 holes before breaking while running at 5 to 10 sfm (1.5 to 3.0 m/min.). Also, Mid Valley experienced thread size and tearing issues, which prevented a thread gage from being inserted.
To avoid tap breakage, Mid Valley tried various cutting oils and coolant formulations, but without success. The shop also resorted to starting the tapping process on a vertical machining center, then switching to hand tapping. Manually threading the gummy material, however, consumed 4 to 5 hours per part. “And sometimes we were still breaking the tap,” he said. Besides being time-consuming, hand tapping also means the machine tool sits idle.
Thread milling enables part manufacturers to avoid removing a tool stuck in a hole if the tool breaks, but Mid Valley found carbide thread mills for that size hole were prohibitively expensive and the process consumed too much time compared to tapping on a machine, according to Kluth.
Seeking a solution, Kluth turned to Jason Kasinski, an Emuge Corp. sales representative based in Milwaukee. Kasinski immediately recommended Emuge’s Z-Tap. According to the West Boylston, Mass., high-performance cutting tool manufacturer, the taps have an advanced chamfer geometry and rake and flute form, an increased number of flutes and a shortened thread section to reduce friction and lower torque requirements. This helps reduce tap breakage and enables higher cutting speeds.
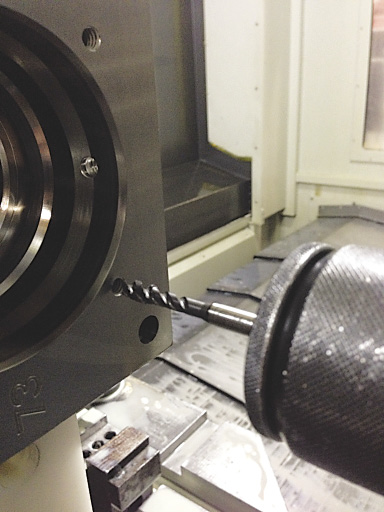
An Emuge GLT-1-coated Z-Tap finishes threading a 316-L stainless steel part.
In addition, Kluth emphasized that the tap’s GLT-1 multilayer coating is effective for threading challenging workpiece materials, such as 316-L stainless. “The coating is really impressive,” he said.
According to Emuge, this is because the coating has an outer antifriction layer and is structured with characteristics that resist heat and help form a consistent, controllable chip that releases smoothly from the hole.
To ensure the Z-Tap was the right tool for the job, Mid Valley tested it by drilling and tapping 200 holes at 20 sfm (6.1 m/min.) in a test part, Kluth explained. “We tapped all 200 holes and the tap looked like it was not even used.”
For optimal results, Emuge recommends applying Z-taps on CNC machines with synchronous spindles using emulsion coolant and synchronous tap holders, which Mid Valley does.
Since switching to the Z-Tap several months ago, Mid Valley has not broken one tap, though it switches taps after each part to avoid the risk of breaking one and having to use the time- and money-eating tap burner, Kluth said. “If put to the test, I would bet we could get four or five parts out of one tap.”
The shop also applies the tap for three other part families made of stainless steel. “I have not tried it on anything harder, like 4140,” he said, “but, usually, if it works well in stainless, it will work well in anything.”
Kluth added that another 316-L stainless job for a different oil-field application requires a screw thread insert (STI) tap and tool breakage issues caused him to again seek a solution from Emuge. Emuge offers taps for STI applications, which do not come standard with a GLT-1 coating, but Emuge can customize the taps with this coating. Based on Kasinski 's recommendation, Mid Valley buys Emuge taps for STI applications that are stocked standard in a bright finish and then upgraded by Emuge with the GLT-1 coating. “They work just wonderfully,” Kluth said.
Related Glossary Terms
- computer numerical control ( CNC)
computer numerical control ( CNC)
Microprocessor-based controller dedicated to a machine tool that permits the creation or modification of parts. Programmed numerical control activates the machine’s servos and spindle drives and controls the various machining operations. See DNC, direct numerical control; NC, numerical control.
- coolant
coolant
Fluid that reduces temperature buildup at the tool/workpiece interface during machining. Normally takes the form of a liquid such as soluble or chemical mixtures (semisynthetic, synthetic) but can be pressurized air or other gas. Because of water’s ability to absorb great quantities of heat, it is widely used as a coolant and vehicle for various cutting compounds, with the water-to-compound ratio varying with the machining task. See cutting fluid; semisynthetic cutting fluid; soluble-oil cutting fluid; synthetic cutting fluid.
- emulsion
emulsion
Suspension of one liquid in another, such as oil in water.
- flutes
flutes
Grooves and spaces in the body of a tool that permit chip removal from, and cutting-fluid application to, the point of cut.
- gang cutting ( milling)
gang cutting ( milling)
Machining with several cutters mounted on a single arbor, generally for simultaneous cutting.
- machining center
machining center
CNC machine tool capable of drilling, reaming, tapping, milling and boring. Normally comes with an automatic toolchanger. See automatic toolchanger.
- milling
milling
Machining operation in which metal or other material is removed by applying power to a rotating cutter. In vertical milling, the cutting tool is mounted vertically on the spindle. In horizontal milling, the cutting tool is mounted horizontally, either directly on the spindle or on an arbor. Horizontal milling is further broken down into conventional milling, where the cutter rotates opposite the direction of feed, or “up” into the workpiece; and climb milling, where the cutter rotates in the direction of feed, or “down” into the workpiece. Milling operations include plane or surface milling, endmilling, facemilling, angle milling, form milling and profiling.
- rake
rake
Angle of inclination between the face of the cutting tool and the workpiece. If the face of the tool lies in a plane through the axis of the workpiece, the tool is said to have a neutral, or zero, rake. If the inclination of the tool face makes the cutting edge more acute than when the rake angle is zero, the rake is positive. If the inclination of the tool face makes the cutting edge less acute or more blunt than when the rake angle is zero, the rake is negative.
- tap
tap
Cylindrical tool that cuts internal threads and has flutes to remove chips and carry tapping fluid to the point of cut. Normally used on a drill press or tapping machine but also may be operated manually. See tapping.
- tapping
tapping
Machining operation in which a tap, with teeth on its periphery, cuts internal threads in a predrilled hole having a smaller diameter than the tap diameter. Threads are formed by a combined rotary and axial-relative motion between tap and workpiece. See tap.
- threading
threading
Process of both external (e.g., thread milling) and internal (e.g., tapping, thread milling) cutting, turning and rolling of threads into particular material. Standardized specifications are available to determine the desired results of the threading process. Numerous thread-series designations are written for specific applications. Threading often is performed on a lathe. Specifications such as thread height are critical in determining the strength of the threads. The material used is taken into consideration in determining the expected results of any particular application for that threaded piece. In external threading, a calculated depth is required as well as a particular angle to the cut. To perform internal threading, the exact diameter to bore the hole is critical before threading. The threads are distinguished from one another by the amount of tolerance and/or allowance that is specified. See turning.