END USER: Fiat Powertrain Technologies do Brasil Ltda., www.fiat.com.
CHALLENGE: Extend the life cycle of machine tools that produce engine crankshafts and cylinder blocks.
SOLUTION: Upgraded CNC systems.
SOLUTION PROVIDER: NUM Corp., (630) 505-7722, www.num.com.
Extending the life cycle of machine tools while minimizing future downtime is critical when producing major components for automotive engines. To achieve that, Fiat Powertrain Technologies do Brasil Ltda. needed to upgrade the CNC systems of machine tools used to produce crankshaft and cylinder blocks at its engine plant in Campo Largo, Brazil, according to Tarcisio Cruz Filho, technical support manager at the plant.
The plant manufactures about 230,000 engines annually and specializes in 1.6- and 1.8-liter E.torQ engines for medium-size cars that can run on gasoline or ethanol. It uses multiple-axis CNC transfer machines, machining centers, grinding machines and custom machine tools throughout its operations. In total, the plant’s crankshaft and cylinder production lines are equipped with 20 key machines, involving more than 120 feed axes, and each machine was originally controlled by a 1050 series CNC from NUM Corp., Naperville, Ill., with NUM’s MDLU1 servodrives and BMH series servomotors.
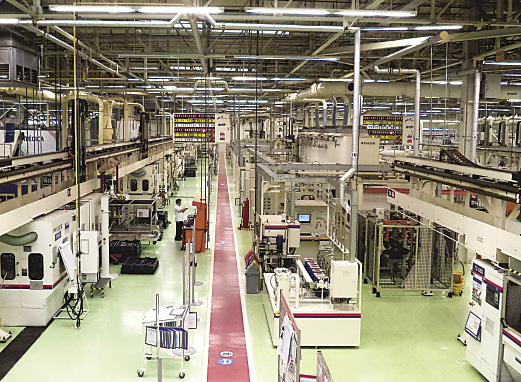
NUM is helping to upgrade the CNC systems of vital machine tools at Fiat Powertrain’s engine manufacturing plant in Campo Largo, Brazil.
The average age of the machines was approaching 20 years and, as the machines and their CNCs aged, Fiat Powertrain became increasingly concerned about the likelihood of increased downtime. In addition, troubleshooting the machines and sourcing spare parts, as well as performing general machine maintenance, was threatening to take too long and negatively impact production. This is because some machine components were scheduled to no longer be available as new parts, requiring time-consuming repairs if Fiat couldn’t source an exchange part. Because the machines were fully serviceable, the company made the strategic decision to extend the life cycle of the production lines by upgrading all 20 machines with new CNCs, drives and motors.
After reviewing various products and services from CNC manufacturers, Cruz Filho noted NUM was the best upgrade option because it is the CNC OEM for the machines, would implement the upgrades the fastest and provide the best cost/benefit ratio. The review involved analyzing each machine’s electrical bill of material and electrical prints to determine suitable replacements and required wiring changes, as well as verifying the compatibility of application-level software.
“The fact that we are upgrading machines used for everyday production imposes some very demanding conditions,” he said. “We needed a CNC supplier with the expertise and resources to collaborate on the design and installation of systems here in Brazil, while the systems themselves had to provide exactly the same level of functionality as our existing CNC equipment. We are impressed by the commitment to the project shown by NUM’s management team in Switzerland and by the quality of technical support, including several on-site visits provided by their U.S. office, especially given that the Brazilian market for this CNC series is not huge.”
To minimize production disruption, the replacement CNCs had to be engineered in a way that the upgrade could be accomplished as quickly as possible. Using video conferencing, technical teams from both companies established that NUM’s Axium CNC platform provided the least-invasive upgrade option because it used the same architecture as the 1050 series CNC to minimize wiring and software modifications.
The upgrade also required replacement of the servomotors on all the feed axes of the machines. NUM’s BPH series motors were selected as the replacements partly because they have a built-in feedback device to provide higher resolution and the motor mount is the same as their previous series. In addition, the BPH motors have shaft ends, pilot diameters and flange squares physically identical to their earlier-generation counterparts. This simplifies replacement, and the orientation of their power and sensor connectors can be altered during installation to suit the machine configuration.
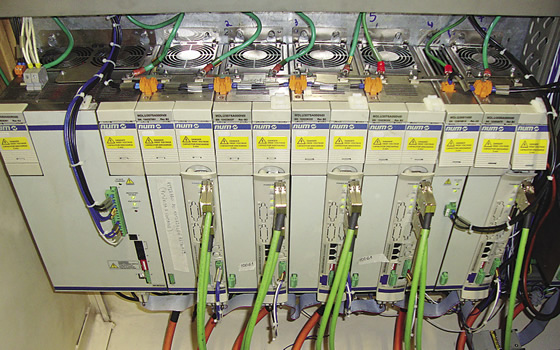
The new controllers at Fiat Powertrain are based on NUM Axium CNCs and the NUMDrive C servodrives.
“We allowed for a maximum of 4 days out-of-service time for each CNC machine on our crankshaft and cylinder block production lines,” Cruz Filho said. “Most of the machines have been upgraded and in each case—even on complex machines with seven controlled axes plus spindles—it has taken less time than we allocated. The machines’ diagnostics are now much better, allowing us to perform more efficient preventive maintenance, and our technicians are now familiar with the CNC systems, all of which will help reduce production downtime in the future.”
He added that the upgrade is on track to be completed by the end of the year.
Collaboration in knowledge transfer is proving to be valuable in making the upgrade proceed smoothly. “The exchange of information and the training that NUM provided for our maintenance staff during the upgrade were important,” said Claudio Rocha, manufacturing engineering director for Fiat Powertrain’s Latin American operations. “We appreciate this open approach and the commitment demonstrated by the supplier in this program.”
As part of the installation, for example, Fiat technicians were involved in the system backup translation and reload, said NUM General Manager Steven Schilling. “They also learned to view and interpret more advanced diagnostic and historical fault pages.”
Because Fiat Powertrain’s technicians were fully involved at each phase of the upgrade, they gained a high level of NUM system know-how to help achieve the project’s goal of maximizing the production lines’ life cycle, Schilling noted.
Related Glossary Terms
- centers
centers
Cone-shaped pins that support a workpiece by one or two ends during machining. The centers fit into holes drilled in the workpiece ends. Centers that turn with the workpiece are called “live” centers; those that do not are called “dead” centers.
- computer numerical control ( CNC)
computer numerical control ( CNC)
Microprocessor-based controller dedicated to a machine tool that permits the creation or modification of parts. Programmed numerical control activates the machine’s servos and spindle drives and controls the various machining operations. See DNC, direct numerical control; NC, numerical control.
- feed
feed
Rate of change of position of the tool as a whole, relative to the workpiece while cutting.
- grinding
grinding
Machining operation in which material is removed from the workpiece by a powered abrasive wheel, stone, belt, paste, sheet, compound, slurry, etc. Takes various forms: surface grinding (creates flat and/or squared surfaces); cylindrical grinding (for external cylindrical and tapered shapes, fillets, undercuts, etc.); centerless grinding; chamfering; thread and form grinding; tool and cutter grinding; offhand grinding; lapping and polishing (grinding with extremely fine grits to create ultrasmooth surfaces); honing; and disc grinding.