END USER: AMR Machines LLC, (860) 336-6208.
CHALLENGE: Reduce cycle times and time spent loading and unloading parts into a machine.
SOLUTION: Use clamps to create custom fixture plates and gang more parts per machining cycle.
SOLUTION PROVIDER: Mitee-Bite Products LLC, (800) 543-3580, www.miteebite.com.
Be it a depiction of a micrometer, a dragon or Larry, Moe and Curly, a sizeable portion of the population likes to adorn their epidermis with tattoos. Handcrafted tattoo machines for laying the ink can be fabricated from clock radio and headphone parts, but people tend to favor professional tattoo machines rather than looking like they received their designs while doing hard time.
Austin Riley understands the trade and, in 2012, founded AMR Machines LLC, Putnam, Conn., to machine parts for tattoo machines and make and distribute the machines and their components.
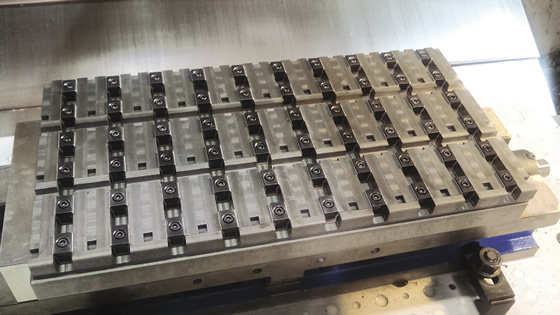
Mitee-Bite clamps enable AMR Machines to gang up to 60 parts in a fixture.
Along with another machinist, he produces the machine frames and parts on two vertical machining centers and a CNC lathe without live tooling. The workpiece materials include ductile iron, steel, brass, aluminum and Delrin. Initially, the shop was machining up to four parts at a time on a double vice, but needed a more cost-effective method. “They are low-dollar parts,” he said.
Riley explained that by creating a custom fixture to gang up to 60 parts per machining cycle, he’d be able to reduce the cycle time while allowing a machine to run longer before swapping parts. Instead of constantly monitoring a machine, having a machine spindle spend more time cutting would allow Riley and his employee to perform other functions during machining, such as deburring with knives. “I do use a tumbler and media blast parts, but I have to manually remove some of the bigger burrs,” he said.
Riley searched online for a solution and, after reading a forum about clamps from Mitee-Bite Products LLC, Center Ossipee, N.H., he visited the company’s Web site and saw that some of its clamps fit his application. They include the Uniforce and Pitbull clamps, as well as TalonGrip vise jaws. “I make my own jaws for them,” he said about the TalonGrips, “but I order the grips and the stops.”
Riley noted the clamps struck him as expensive at first, but he soon realized they pull their weight in productivity. “They pay for themselves quickly.” He estimated that the clamps helped boost productivity 40 to 50 percent.
In addition, because the TalonGrip system enables clamping on as little as 0.060" (1.5mm) of material, AMR Machines orders 3"×3" (76.2mm × 76.2mm) blocks of material that are 1" (25.4mm) thick to reduce costs. “Before the TalonGrips,” Riley said, “I had to order blocks 1¼" thick so I had something to grab onto, and that was the next size up.”
The shop still uses the double vise with the jaws on the outside to hold the 18" (457.2mm) fixture plate, or shop-made pallet, but is able to produce the parts with significantly less operator intervention. “Doing them the old way, I would’ve dedicated a worker to that machine for the whole day indefinitely, standing there and waiting every 3 minutes to take the parts out, flip them and hit the start button again,” Riley said.
With the custom fixtures and Mitee-Bite clamps, the shop produces about 2,000 parts every few months. Although a fixture plate gets unloaded and reloaded between machining cycles, Riley noted AMR Machines could implement a system to unload/load one plate of parts while another is being machined if volume increases.
Related Glossary Terms
- centers
centers
Cone-shaped pins that support a workpiece by one or two ends during machining. The centers fit into holes drilled in the workpiece ends. Centers that turn with the workpiece are called “live” centers; those that do not are called “dead” centers.
- computer numerical control ( CNC)
computer numerical control ( CNC)
Microprocessor-based controller dedicated to a machine tool that permits the creation or modification of parts. Programmed numerical control activates the machine’s servos and spindle drives and controls the various machining operations. See DNC, direct numerical control; NC, numerical control.
- fixture
fixture
Device, often made in-house, that holds a specific workpiece. See jig; modular fixturing.
- lathe
lathe
Turning machine capable of sawing, milling, grinding, gear-cutting, drilling, reaming, boring, threading, facing, chamfering, grooving, knurling, spinning, parting, necking, taper-cutting, and cam- and eccentric-cutting, as well as step- and straight-turning. Comes in a variety of forms, ranging from manual to semiautomatic to fully automatic, with major types being engine lathes, turning and contouring lathes, turret lathes and numerical-control lathes. The engine lathe consists of a headstock and spindle, tailstock, bed, carriage (complete with apron) and cross slides. Features include gear- (speed) and feed-selector levers, toolpost, compound rest, lead screw and reversing lead screw, threading dial and rapid-traverse lever. Special lathe types include through-the-spindle, camshaft and crankshaft, brake drum and rotor, spinning and gun-barrel machines. Toolroom and bench lathes are used for precision work; the former for tool-and-die work and similar tasks, the latter for small workpieces (instruments, watches), normally without a power feed. Models are typically designated according to their “swing,” or the largest-diameter workpiece that can be rotated; bed length, or the distance between centers; and horsepower generated. See turning machine.
- micrometer
micrometer
A precision instrument with a spindle moved by a finely threaded screw that is used for measuring thickness and short lengths.
- sawing machine ( saw)
sawing machine ( saw)
Machine designed to use a serrated-tooth blade to cut metal or other material. Comes in a wide variety of styles but takes one of four basic forms: hacksaw (a simple, rugged machine that uses a reciprocating motion to part metal or other material); cold or circular saw (powers a circular blade that cuts structural materials); bandsaw (runs an endless band; the two basic types are cutoff and contour band machines, which cut intricate contours and shapes); and abrasive cutoff saw (similar in appearance to the cold saw, but uses an abrasive disc that rotates at high speeds rather than a blade with serrated teeth).
- web
web
On a rotating tool, the portion of the tool body that joins the lands. Web is thicker at the shank end, relative to the point end, providing maximum torsional strength.