END USER: Orange Vise Co., (714) 482-3952, www.orangevise.com.
CHALLENGE: Speed throughput when deburring and surface finishing vise components.
SOLUTION: Abrasive disc brushes applied via a machining center's automatic toolchanger.
SOLUTION PROVIDER: Brush Research Manufacturing Co. Inc., (323) 261-2193, www.brushresearch.com.
Manually processing parts to remove burrs and tool marks is a time-consuming, labor-intensive task—something Eric Sun quickly realized after founding Orange Vise Co. in 2012. The Stanton, Calif.-based manufacturer of workholding devices deburred with hand-held brushes, files and other deburring tools and used an automatic surface grinder to remove cutting tool marks and impart an even surface finish and uniform appearance on all part surfaces. Those included noncritical, unhardened surfaces.
“A lot of the surfaces don’t require high-enough precision to warrant the expense and time of surface grinding,” Sun said.
Surfaces hardened to 50 to 60 HRC prior to machining, however, required grinding because milling cutters would wear too quickly, according to Sun. “This process involved removing, cleaning and repositioning parts several times to be able to grind each face.”
Although a deburring tool’s role is to remove burrs, Sun noted one for deburring 45° chamfers could leave a burr when the tool began to wear, even slightly. Based on this potential problem, the company had an employee inspect each part and manually remove any burrs.
In its quest to improve throughput and part consistency by automating deburring and surface finishing, the company examined an array of possible solutions that were “all over the place” and determined that abrasive disc brushes were the best option, according to Sun. Similar to a cutting tool, an abrasive brush occupies a position in a CNC machine tool’s magazine and the machine’s automatic toolchanger places the brush into the spindle for use. This allows a CNC operator to automate deburring while imparting a fine surface finish in the same operation because the rotating brush abrades the workpiece material as it conforms around the surface being deburred.
Based on a recommendation from a tool rep, Orange Vise chose Dot-style NamPower abrasive disc brushes from Brush Research Manufacturing Co. Inc., Los Angeles. “We started using the NamPower brushes for deburring, but quickly discovered they provided a really nice surface finish,” Sun said.
The brushes contain a combination of ceramic and silicon-carbide abrasives and are composed of flexible abrasive nylon filaments bonded to a fiber-reinforced thermoplastic base, according to Brush Research. The ceramic abrasive is responsible for material removal but tends to cut a bit coarse, while silicon carbide acts as a buffer to the cutting action. The abrasive filaments work like flexible files, conforming to part contours, wiping and filing across part edges and surfaces. In addition, Dot-style brushes allow entry into small holes and spaces.
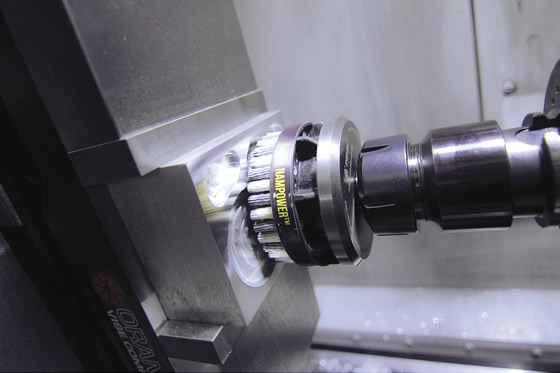
Orange Vise applies NamPower abrasive brushes from Brush Research to automatically deburr and surface finish the vise components it machines.
While they do remove metal, Sun pointed out that the brushes do not create tool marks and generate a surface finish fine enough to allow it to blend with the ground finishes. “With large surfaces that require multiple passes, there are no visible blends,” he said. “The whole thing looked like it was done in one pass.”
Sun noted the brushes, which add about 30 seconds to the part-making process and are applied on Orange Vise’s Mori Seiki NHX4000 horizontal machining center, made the deburring and finishing process significantly faster than the previous method.
Orange Vise uses brushes that measure 100mm (3.94"), 125mm (4.92") and 150mm (5.90") in diameter for steel, stainless steel, cast iron and aluminum workpieces. Brush changes are infrequent no matter what material is being processed, according to Sun.
He explained that after zeroing a brush to where it is barely touching the workpiece surface, the DOC ranges from 0.020" to 0.050" or more.
The company also uses the brushes to deburr the tops of parts engraved with a burr-generating 45° V-bit tool.
In addition to deburring and surface finishing, Orange Vise uses the brushes for edge blending and occasionally for rust removal when a surface isn’t wiped clean and the part is left outside.
To help dissipate heat, eliminate filament smearing, improve surface finish and extend brush life, a through-coolant toolholder is used to hold the brushes. “One of the best things to use coolant for is washing away the dust the brush creates,” Sun added.
According to Brush Research, the NamPower brushes were developed with tool longevity in mind. Because of the bristles’ linear construction, sharp new grains constantly come into contact with the workpiece surface and wear away, exposing fresh particles for consistent cutting throughout the bristle length.
Sun noted all of the brushes Orange Vise has purchased are still usable, with some having seen more than 2,000 minutes of use. “We use them just about every day and there’s definitely been no difference in performance from day one until now,” he said.
“We mainly use the 18mm bristles because our parts don’t have a whole lot of features sticking out,” he added, noting the bristles become shorter and stiffer with use. “With the 38mm bristles, youcould go much deeper without exerting as much force as an 18mm bristle.”
Related Glossary Terms
- abrasive
abrasive
Substance used for grinding, honing, lapping, superfinishing and polishing. Examples include garnet, emery, corundum, silicon carbide, cubic boron nitride and diamond in various grit sizes.
- automatic toolchanger
automatic toolchanger
Mechanism typically included in a machining center that, on the appropriate command, removes one cutting tool from the spindle nose and replaces it with another. The changer restores the used tool to the magazine and selects and withdraws the next desired tool from the storage magazine. The changer is controlled by a set of prerecorded/predetermined instructions associated with the part(s) to be produced.
- burr
burr
Stringy portions of material formed on workpiece edges during machining. Often sharp. Can be removed with hand files, abrasive wheels or belts, wire wheels, abrasive-fiber brushes, waterjet equipment or other methods.
- computer numerical control ( CNC)
computer numerical control ( CNC)
Microprocessor-based controller dedicated to a machine tool that permits the creation or modification of parts. Programmed numerical control activates the machine’s servos and spindle drives and controls the various machining operations. See DNC, direct numerical control; NC, numerical control.
- coolant
coolant
Fluid that reduces temperature buildup at the tool/workpiece interface during machining. Normally takes the form of a liquid such as soluble or chemical mixtures (semisynthetic, synthetic) but can be pressurized air or other gas. Because of water’s ability to absorb great quantities of heat, it is widely used as a coolant and vehicle for various cutting compounds, with the water-to-compound ratio varying with the machining task. See cutting fluid; semisynthetic cutting fluid; soluble-oil cutting fluid; synthetic cutting fluid.
- filing
filing
Operation in which a tool with numerous small teeth is applied manually to round off sharp corners and shoulders and remove burrs and nicks. Although often a manual operation, filing on a power filer or contour band machine with a special filing attachment can be an intermediate step in machining low-volume or one-of-a-kind parts.
- gang cutting ( milling)
gang cutting ( milling)
Machining with several cutters mounted on a single arbor, generally for simultaneous cutting.
- grinding
grinding
Machining operation in which material is removed from the workpiece by a powered abrasive wheel, stone, belt, paste, sheet, compound, slurry, etc. Takes various forms: surface grinding (creates flat and/or squared surfaces); cylindrical grinding (for external cylindrical and tapered shapes, fillets, undercuts, etc.); centerless grinding; chamfering; thread and form grinding; tool and cutter grinding; offhand grinding; lapping and polishing (grinding with extremely fine grits to create ultrasmooth surfaces); honing; and disc grinding.
- machining center
machining center
CNC machine tool capable of drilling, reaming, tapping, milling and boring. Normally comes with an automatic toolchanger. See automatic toolchanger.
- milling
milling
Machining operation in which metal or other material is removed by applying power to a rotating cutter. In vertical milling, the cutting tool is mounted vertically on the spindle. In horizontal milling, the cutting tool is mounted horizontally, either directly on the spindle or on an arbor. Horizontal milling is further broken down into conventional milling, where the cutter rotates opposite the direction of feed, or “up” into the workpiece; and climb milling, where the cutter rotates in the direction of feed, or “down” into the workpiece. Milling operations include plane or surface milling, endmilling, facemilling, angle milling, form milling and profiling.
- surface grinding
surface grinding
Machining of a flat, angled or contoured surface by passing a workpiece beneath a grinding wheel in a plane parallel to the grinding wheel spindle. See grinding.
- toolchanger
toolchanger
Carriage or drum attached to a machining center that holds tools until needed; when a tool is needed, the toolchanger inserts the tool into the machine spindle. See automatic toolchanger.
- toolholder
toolholder
Secures a cutting tool during a machining operation. Basic types include block, cartridge, chuck, collet, fixed, modular, quick-change and rotating.