END USER: Evansville Tool & Die Inc., (812) 422-7101, www.evansvilletoolanddie.com.
CHALLENGE: Increase wire EDM capacity and cutting speed.
SOLUTION: Replace two old, technologically obsolete wire EDMs with two new ones.
SOLUTION PROVIDERS: Innovate Technologies Inc., (877) 250-1770, www.innovatetec.com; MC Machinery Systems Inc., (630) 616-5920, www.mcmachinery.com.
A machine tool may function as effectively as it was designed to, but technological obsolescence dictates when it’s time to upgrade and sever ties. Evansville (Ind.) Tool & Die Inc. experienced that with two wire EDMs: one 25 years old, the other a year older.
The 15-person manufacturing service provider specializes in producing dies, thermoform molds, trim tools and production machining. Jack Droste, company owner, said the shop began wire EDMing in 1979, 20 years after the company was founded, and performs a multitude of wire EDM jobs in a variety of workpiece materials, including steel, aluminum, brass and graphite. “We do custom wire work and whatever can be done on a wire machine.”
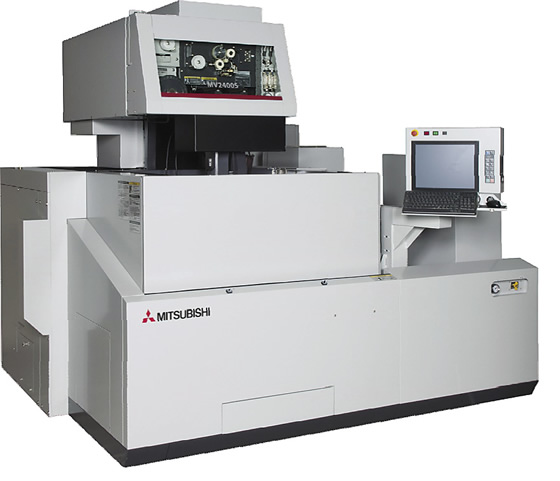
The Mitsubishi MV2400-ST, as well as the MV2400-S (pictured), features a noncontact cylindrical drive system and the M700 series control with 15 " touchscreen. Images courtesy MC Machinery Systems.
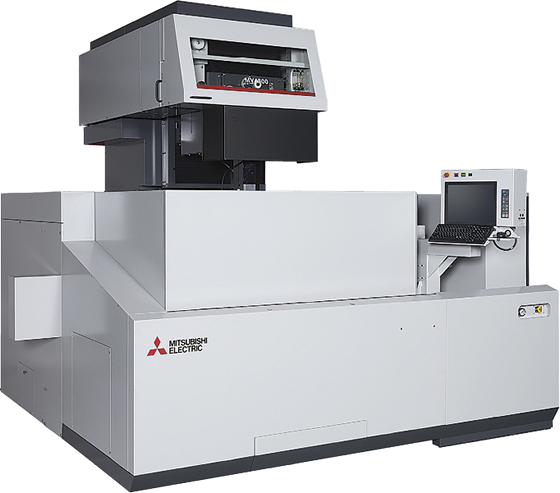
The Mitsubishi MV4800 wire EDM is capable of submerged cutting up to 20 " deep with the support of an auto-threading system.
Nonetheless, the company’s vintage Mitsubishi EDMs were limited in their capacity. As an example, they could only cut material up to 10 " (254mm) thick, Droste noted. That limitation restricted the type of work Evansville Tool & Die could bid on. “We had to turn down work because of the size of our machines,” he said, adding that the shop has a 20-year-old Mitsubishi FX10 wire EDM, with X-, Y- and Z-axis travels of 14 ", 10 " and 8.5 " (355.6mm, 254mm and 215.9mm), respectively.
Realizing it was time to replace the two oldest wire EDMs, Droste researched new equipment offerings, including participating in some cutting demonstrations, but the shop’s experience with Mitsubishi tipped the balance. “I like their machines and I like their service,” he said. “I didn’t see anything better out there, so I stuck with who I’ve had a long relationship with.”
Evansville Tool & Die purchased an MV2400-ST and an MV4800 from Innovate Technologies Inc., a Mitsubishi distributor in St. Charles, Ill. The MV2400-ST has X-, Y- and Z-axis travels of 23.6 ", 15.7 " and 16.5 " (599.4mm, 398.8mm and 419.1mm), respectively, is capable of submerged cutting up to 16.5 " deep and can handle a workpiece up to 41.3 " wide × 32.3 " deep × 16.3 " high (1,049mm × 820.4mm × 414mm). The MV4800 has X-, Y- and Z-axis travels of 31.5 ", 23.6 " and 20.1 " (800.1mm, 599.4mm and 510.5mm), respectively, is capable of submerged cutting up to 20 " (508mm) deep and can handle a workpiece up to 53.1 " wide × 43.3 " deep × 20.0 " high (1,348.7mm × 1,100mm × 508mm).
“Now with the capability of cutting up to 20 " thick, these additions enable us to do work we couldn’t do before,” Droste said, adding that the cutting speed for the new machines is considerably faster than the old ones and they are able to impart a finer surface finish with no recast layer.
He noted the shop doesn’t have the capacity for more than three wire EDMs, so it sold the two machines. “They were good, old machines, but their time had come,” Droste said. “We were still using them every day, until the day I unhooked them.”
Related Glossary Terms
- cutting speed
cutting speed
Tangential velocity on the surface of the tool or workpiece at the cutting interface. The formula for cutting speed (sfm) is tool diameter 5 0.26 5 spindle speed (rpm). The formula for feed per tooth (fpt) is table feed (ipm)/number of flutes/spindle speed (rpm). The formula for spindle speed (rpm) is cutting speed (sfm) 5 3.82/tool diameter. The formula for table feed (ipm) is feed per tooth (ftp) 5 number of tool flutes 5 spindle speed (rpm).
- electrical-discharge machining ( EDM)
electrical-discharge machining ( EDM)
Process that vaporizes conductive materials by controlled application of pulsed electrical current that flows between a workpiece and electrode (tool) in a dielectric fluid. Permits machining shapes to tight accuracies without the internal stresses conventional machining often generates. Useful in diemaking.
- wire EDM
wire EDM
Process similar to ram electrical-discharge machining except a small-diameter copper or brass wire is used as a traveling electrode. Usually used in conjunction with a CNC and only works when a part is to be cut completely through. A common analogy is wire electrical-discharge machining is like an ultraprecise, electrical, contour-sawing operation.