Continuing the theme of my previous two columns, presented here are additional tips and tricks for effectively performing finish work.
■ If you have a bunch of parts to be sanded at a particular angle, you can mark witness lines on the table of the belt sander to guide your roughing work. This visual cue keeps you from drifting too far from your intended angle. You can clamp a guide to the table, but that destroys one spot on the bench.
■ Use a thin masking plate when you are working with intersecting linear finish lines. This produces a crisp demarcation line between the two intersecting finishes. Be sure to use a plate of the same material to avoid contamination.
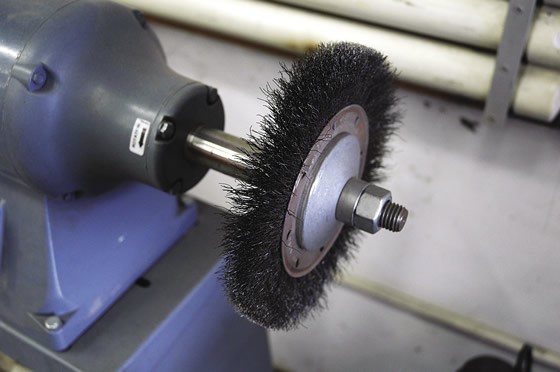
One of the guiltiest parties in the shop with regard to contamination is the dirty little wire brush on a bench grinder or buffer.
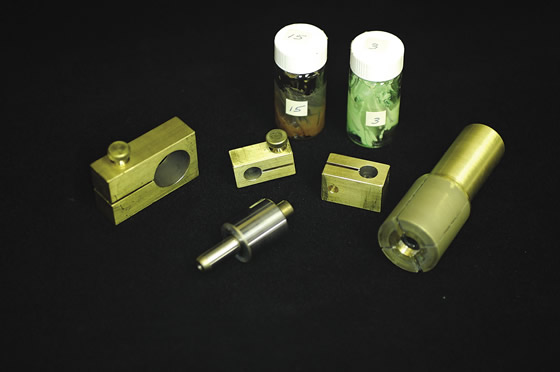
These brass laps were applied to a bearing bore (far right) and the OD of a gage (front, center). The lapping compound is diamond paste. The laps are applied at 100 to 300 rpm and stroked axially over the part length to produce a 30° to 45° crosshatch pattern.
■ Mark the materials you use abrasives on and segregate them from the other discs. I have seen some beautiful jobs ruined by a contaminated sanding disc or even a dirty wire brush. When in doubt, use a new disc. One of the guiltiest parties in the shop with regard to contamination is the dirty little wire brush on the bench grinder or buffer. It spreads its corrosive disease on everything it touches. You may have the best intentions, but this wheel is almost always contaminated with steel, rust and grease.
■ Cylindrical laps for OD and ID work are easy to make and produce fantastic results. The results are controllable down to microinches if necessary. The laps need to be made accurately, but, with a little effort, results that cannot be attained any other way are possible.
■ Dress a surface grinder wheel at a slight angle for peripheral roughing work. The edge will break down fast, exposing sharp grains for fast stock removal. Redress the wheel for fine finish work. For roughing, use an aggressive DOC and step-over as much as the wheel will tolerate without complaint. The abrasive grains must break down to continue the cutting action. If they are babied and allowed to glaze over, all your effort just turns into heat. Abrasives should be thought of as little cutting tools, much like those applied on a lathe or milling machine. Properly applied, the chips from abrasive tools look similar to those from cutting tools under high magnification.
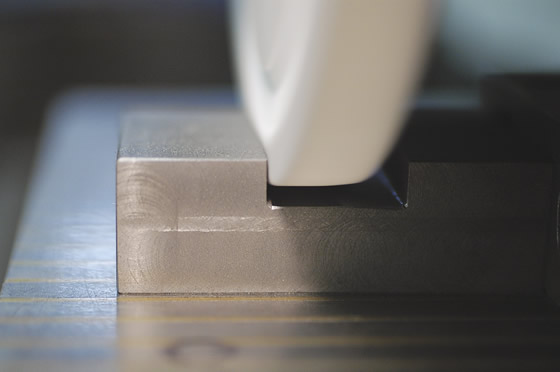
Although not an efficient material-removal method, side-wheel grinding is sometimes necessary.
■ A similar roughing trick works for side-wheel grinding, which even on a good day is a bit of a pain. Side-wheel grinding is not an efficient material-removal method, but it is necessary at times because of setup issues or part geometry. Dress the side of a wheel as you normally would, then stop the grinder and loosen the nut. Rotate the wheel slightly in relation to the spindle, tighten it all back up and perform your side-wheel roughing. The wheel will run out a little from where it was dressed and only cut on one part of the periphery. This small edge breaks down quickly and continues to cut while needing frequent redressing during roughing. Redress the wheel and don’t rotate it when finishing. This trick can extend the time between dressings, making a difficult grinding job go faster.
■ Glass-bead blasting can deburr and impart finishes that are difficult to produce any other way. Anything from a fine satin finish to a rough surface to add grip or traction to a part can be generated with a few different grit sizes and by varying the blasting pressures. Tool marks can be blended or removed with fine-mesh glass beads.
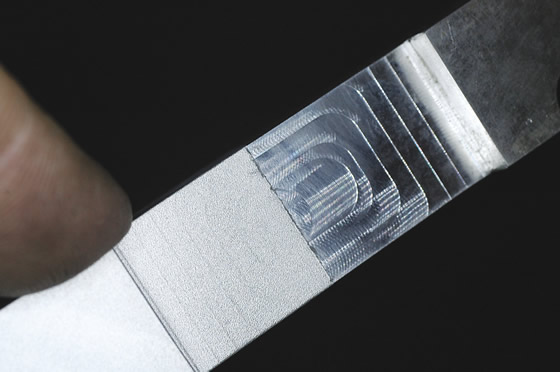
Fine-mesh glass beads are suitable for blending or removing tool marks.
■ Beware of blasting large sheets and surfaces. Using a bead blaster is similar to hammering with a vast supply of ball peen hammers and will remove material if you’re not careful. Also, the bead or sand blaster is an often-overlooked source of material cross contamination. If you have been cleaning engine parts, for example, you’ll need to replace the media when blasting medical parts.
■ Ever had a hard time holding onto small parts in a bead blaster? Ever drop one in the bottom of the blaster and have to fish it out? Use a tea strainer to keep the part under the blast stream, but be sure the mesh opening is larger than the beads or it will take a long time to do the job.
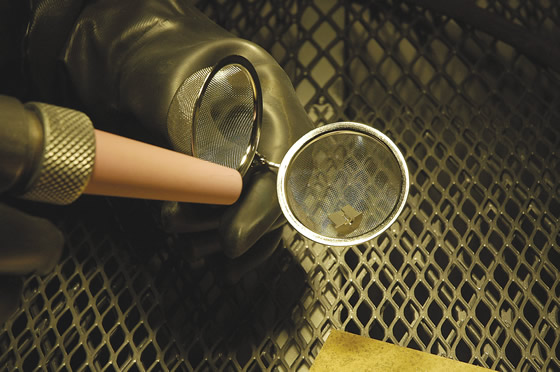
When bead blasting a difficult-to-hold part, a tea strainer keeps the part under the blast stream. A spring closes and holds the two halves of the strainer together during use.
■ There is a use for all those cheap, nicely hemmed carpet samples flooring stores offer! They make great throwaway portable part protectors and backup surfaces for dual-action detailing. When a sample gets loaded with dust, toss it and start over with a fresh one.
■ For fine deburring, try a surgical scalpel blade. The sterile stainless steel blades seem to be considerably sharper than carbon steel ones. If you don’t like it for deburring, you can always do a little amateur shop surgery with it. CTE
About the Author: Tom Lipton is a career metalworker who has worked at various job shops that produce parts for the consumer product development, laboratory equipment, medical services and custom machinery design industries. He has received six U.S. patents and lives in Alamo, Calif. For more information, visit his blog at oxtool.blogspot.com and video channel at www.youtube.com/user/oxtoolco. Lipton’s column is adapted from information in his book “Metalworking Sink or Swim: Tips and Tricks for Machinists, Welders, and Fabricators,” published by Industrial Press Inc., South Norwalk, Conn. The publisher can be reached by calling (888) 528-7852 or visiting www.industrialpress.com. By indicating the code CTE-2014 when ordering, CTE readers will receive a 20 percent discount off the book’s list price of $44.95.Related Glossary Terms
- abrasive
abrasive
Substance used for grinding, honing, lapping, superfinishing and polishing. Examples include garnet, emery, corundum, silicon carbide, cubic boron nitride and diamond in various grit sizes.
- gang cutting ( milling)
gang cutting ( milling)
Machining with several cutters mounted on a single arbor, generally for simultaneous cutting.
- grinding
grinding
Machining operation in which material is removed from the workpiece by a powered abrasive wheel, stone, belt, paste, sheet, compound, slurry, etc. Takes various forms: surface grinding (creates flat and/or squared surfaces); cylindrical grinding (for external cylindrical and tapered shapes, fillets, undercuts, etc.); centerless grinding; chamfering; thread and form grinding; tool and cutter grinding; offhand grinding; lapping and polishing (grinding with extremely fine grits to create ultrasmooth surfaces); honing; and disc grinding.
- inner diameter ( ID)
inner diameter ( ID)
Dimension that defines the inside diameter of a cavity or hole. See OD, outer diameter.
- lapping
lapping
Finishing operation in which a loose, fine-grain abrasive in a liquid medium abrades material. Extremely accurate process that corrects minor shape imperfections, refines surface finishes and produces a close fit between mating surfaces.
- lapping compound( powder)
lapping compound( powder)
Light, abrasive material used for finishing a surface.
- lathe
lathe
Turning machine capable of sawing, milling, grinding, gear-cutting, drilling, reaming, boring, threading, facing, chamfering, grooving, knurling, spinning, parting, necking, taper-cutting, and cam- and eccentric-cutting, as well as step- and straight-turning. Comes in a variety of forms, ranging from manual to semiautomatic to fully automatic, with major types being engine lathes, turning and contouring lathes, turret lathes and numerical-control lathes. The engine lathe consists of a headstock and spindle, tailstock, bed, carriage (complete with apron) and cross slides. Features include gear- (speed) and feed-selector levers, toolpost, compound rest, lead screw and reversing lead screw, threading dial and rapid-traverse lever. Special lathe types include through-the-spindle, camshaft and crankshaft, brake drum and rotor, spinning and gun-barrel machines. Toolroom and bench lathes are used for precision work; the former for tool-and-die work and similar tasks, the latter for small workpieces (instruments, watches), normally without a power feed. Models are typically designated according to their “swing,” or the largest-diameter workpiece that can be rotated; bed length, or the distance between centers; and horsepower generated. See turning machine.
- milling
milling
Machining operation in which metal or other material is removed by applying power to a rotating cutter. In vertical milling, the cutting tool is mounted vertically on the spindle. In horizontal milling, the cutting tool is mounted horizontally, either directly on the spindle or on an arbor. Horizontal milling is further broken down into conventional milling, where the cutter rotates opposite the direction of feed, or “up” into the workpiece; and climb milling, where the cutter rotates in the direction of feed, or “down” into the workpiece. Milling operations include plane or surface milling, endmilling, facemilling, angle milling, form milling and profiling.
- milling machine ( mill)
milling machine ( mill)
Runs endmills and arbor-mounted milling cutters. Features include a head with a spindle that drives the cutters; a column, knee and table that provide motion in the three Cartesian axes; and a base that supports the components and houses the cutting-fluid pump and reservoir. The work is mounted on the table and fed into the rotating cutter or endmill to accomplish the milling steps; vertical milling machines also feed endmills into the work by means of a spindle-mounted quill. Models range from small manual machines to big bed-type and duplex mills. All take one of three basic forms: vertical, horizontal or convertible horizontal/vertical. Vertical machines may be knee-type (the table is mounted on a knee that can be elevated) or bed-type (the table is securely supported and only moves horizontally). In general, horizontal machines are bigger and more powerful, while vertical machines are lighter but more versatile and easier to set up and operate.
- outer diameter ( OD)
outer diameter ( OD)
Dimension that defines the exterior diameter of a cylindrical or round part. See ID, inner diameter.
- step-over
step-over
Distance between the passes of the toolpath; the path spacing. The distance the tool will move horizontally when making the next pass. Too great of a step-over will cause difficulty machining because there will be too much pressure on the tool as it is trying to cut with too much of its surface area.