END USER: Northwood Industries Inc., (419) 666-2100, www.nwindustries.com.
CHALLENGE: Efficiently machine stainless steel parts without breaking endmills.
SOLUTION: 6-flute, solid-carbide endmills.
SOLUTION PROVIDER: IMCO Carbide Tool Inc., (800) 765-4626, www.imcousa.com.
When a machine shop is faced with either running cutting tools aggressively and breaking them in the process or pampering the tools and taking too long to complete a job, it must find a better way. Northwood Industries Inc. found itself in that situation when machining large, 316 stainless steel plates for the solar power industry, noted Greg Shepard, CNC machinist for the Perrysburg, Ohio, manufacturer.
Founded in 1968, Northwood operates in a 23,000-sq.-ft., air-conditioned plant, where more than 20 shop employees perform production machining, prototyping, fabrication and assembly for a host of industries, with automotive being a significant one. The company also offers design engineering and reverse engineering services.
When endmilling stainless steel plates up to 20 " (508mm) wide × 60 " (1,524mm) long × 3/4 " (19.05mm) thick, Shepard emphasized that a small increase in machining parameters pays big dividends in cycle time. However, when applying ½ "-dia., 4-flute carbide endmills at 2,000 rpm, 20 ipm (0.508 m/min.) and a 0.125 " (3.175mm) DOC, endmills were breaking “left and right” and he couldn’t complete the job.
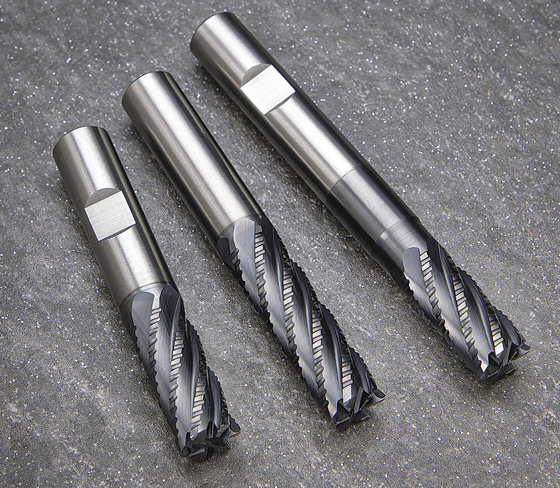
IMCO Carbide Tool’s new INCONEX M8 series 6-flute, solid-carbide endmills are suitable for roughing and finishing.
The shop attempted applying different sizes of endmills, but those tools also broke or burned up. In addition, Shepard reduced the machining parameters, but then the job took an excessively long time. “We wasted a couple hours trying to figure something out,” he said.
Northwood then turned to IMCO Carbide Tool Inc., located around the corner and down the street. IMCO recommended testing its new INCONEX M8 series 6-flute, solid-carbide endmill, which the toolmaker developed for tackling challenging metals, such as Inconel, Hastelloy, Waspalloy and other heat-resistant superalloys. Northwood tried four of the high-performance endmills, one ¼ " (6.35mm), two 3⁄8 " (9.525mm) and one ½ " (12.7mm), and used the two larger sizes on the stainless steel plates. “They both worked out great,” Shepard said, noting the new tools ran at the same machining parameters that caused the others to break.
Shepard added that he appreciates when one tool can complete the job. “It’s real nice because you can rough with it and then finish, and the tool still gives you a nice surface finish on the material,” he said. “You don’t have to set up two different tools.”
According to IMCO, the six flutes have optimized rake and relief angles for maximum cutting-edge engagement, and its AlCrNX coating protects the specially engineered cutting edges from heat generated in the tool/workpiece interface. “We developed a new cutting edge design,” said Steve Avers, application support team leader for IMCO. “Each cutting edge is individually shaped to reduce edge-wearing stress in the cutting zone. An added benefit of the new design is much smaller chips that can be easily flushed from the work zone.”
Although Northwood turns some challenging materials, such as TiAl4V6, Hastelloy and other nickel-base metals, the parts manufacturer has cut S7, 4140 and 4150 steel with the INCONEX M8 endmills, in addition to stainless steel. “They’re only useful for hard materials,” Shepard said. “It’s not like you’re going to run through aluminum with them.”
Related Glossary Terms
- computer numerical control ( CNC)
computer numerical control ( CNC)
Microprocessor-based controller dedicated to a machine tool that permits the creation or modification of parts. Programmed numerical control activates the machine’s servos and spindle drives and controls the various machining operations. See DNC, direct numerical control; NC, numerical control.
- endmill
endmill
Milling cutter held by its shank that cuts on its periphery and, if so configured, on its free end. Takes a variety of shapes (single- and double-end, roughing, ballnose and cup-end) and sizes (stub, medium, long and extra-long). Also comes with differing numbers of flutes.
- endmilling
endmilling
Operation in which the cutter is mounted on the machine’s spindle rather than on an arbor. Commonly associated with facing operations on a milling machine.
- flutes
flutes
Grooves and spaces in the body of a tool that permit chip removal from, and cutting-fluid application to, the point of cut.
- inches per minute ( ipm)
inches per minute ( ipm)
Value that refers to how far the workpiece or cutter advances linearly in 1 minute, defined as: ipm = ipt 5 number of effective teeth 5 rpm. Also known as the table feed or machine feed.
- rake
rake
Angle of inclination between the face of the cutting tool and the workpiece. If the face of the tool lies in a plane through the axis of the workpiece, the tool is said to have a neutral, or zero, rake. If the inclination of the tool face makes the cutting edge more acute than when the rake angle is zero, the rake is positive. If the inclination of the tool face makes the cutting edge less acute or more blunt than when the rake angle is zero, the rake is negative.
- relief
relief
Space provided behind the cutting edges to prevent rubbing. Sometimes called primary relief. Secondary relief provides additional space behind primary relief. Relief on end teeth is axial relief; relief on side teeth is peripheral relief.
- superalloys
superalloys
Tough, difficult-to-machine alloys; includes Hastelloy, Inconel and Monel. Many are nickel-base metals.