END USER: Lotus F1 racing team, +44 1608-672410, www.lotusf1team.com.
CHALLENGE: Boost productivity by reducing machine downtime.
SOLUTION: Six 5-axis milling machines with pallet systems and lights-out manufacturing capability.
SOLUTION PROVIDER: GF Machining Solutions, (800) 282-1336, www.gfms.com/us.
In September of last year, the Lotus F1 Team purchased six 5-axis Mikron HPM 450U automated milling centers from Geneva, Switzerland-based machine tool builder GF Machining Solutions for the Formula 1 racing team’s production facility at its Enstone, England, headquarters. (GF’s U.S. facility is in Lincolnshire, Ill.)
“We made the strategic decision to extend our milling capacities to five axes” said Lotus F1 Team COO Thomas Mayer, “and in this respect we chose a system that allows us to machine workpieces in a single setup. This decision has enabled us to considerably increase productivity, improve the utilization of our machine tools, achieve a higher and more uniform [level of] part precision and lower the unit costs.”
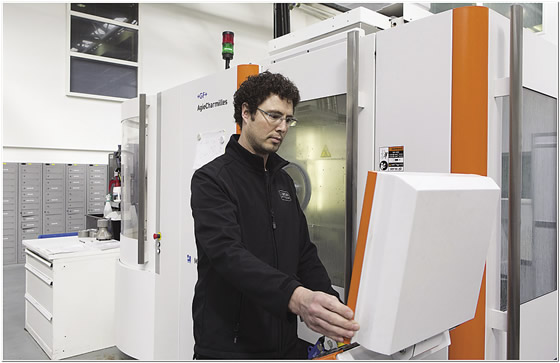
Courtesy of GF Machining Solutions
To standardize production, Lotus F1 Team purchased six 5-axis Mikron HPM 450U milling machines from GF Machining Solutions.
GF has been one of the team’s technical partners since 1997. The team typically will operate a machine for 2 to 3 years before upgrading, according to Mayer. However, the partnership with GF is about more than simply buying the latest and greatest machine tools.
“For us, it’s less about buying a new machine and more about having them provide us with a complete solution to our problem,” Mayer said. “Depending on the issue, that solution may turn out to be a machine, but they are able to bring their expertise to bear and can provide anything up to a fully automated machining cell, if that’s what we need.”
With that in mind, the team put together a list of requirements for GF, and the Mikron HPM 450U was chosen based on its footprint, capacity, features, cost, availability and maintenance requirements. In addition, the machine features a pallet system and lights-out manufacturing capability, allowing Lotus to virtually eliminate machine downtime by enabling premachining work, such as mounting workpieces, to occur off of the machine.
Prior to the purchase, the racing team relied primarily on 3-axis milling machines, which weren’t productive enough, according to Mayer. “We were not as efficient and effective as we wanted to be,” he said. “With the old machines, too much time was wasted setting up the machinery and planning and designing individual add-on devices for milling. We knew that 5-axis machines would be the ideal solution for our production requirements.”
To standardize production, the Lotus F1 Team purchased six identical machines, as well as the corresponding tools and clamping devices for each, so that if one machine fails, another is available without any part compatibility or operator familiarity issues. Along with the Mikron HTM 450U machines, the Lotus F1 team purchased four GF CUT 300 EDMs. The EDMs and machining centers are also used in the auto shop to make parts for testing in the company’s wind tunnel, Mayer noted.
Related Glossary Terms
- centers
centers
Cone-shaped pins that support a workpiece by one or two ends during machining. The centers fit into holes drilled in the workpiece ends. Centers that turn with the workpiece are called “live” centers; those that do not are called “dead” centers.
- gang cutting ( milling)
gang cutting ( milling)
Machining with several cutters mounted on a single arbor, generally for simultaneous cutting.
- milling
milling
Machining operation in which metal or other material is removed by applying power to a rotating cutter. In vertical milling, the cutting tool is mounted vertically on the spindle. In horizontal milling, the cutting tool is mounted horizontally, either directly on the spindle or on an arbor. Horizontal milling is further broken down into conventional milling, where the cutter rotates opposite the direction of feed, or “up” into the workpiece; and climb milling, where the cutter rotates in the direction of feed, or “down” into the workpiece. Milling operations include plane or surface milling, endmilling, facemilling, angle milling, form milling and profiling.