END USER: ulrich medical, +49-731-9654-0, www.ulrichmedical.com.
CHALLENGE: Extend tool life when machining titanium vertebrae implants and supports.
SOLUTION: A shrink-fit collet and collet chuck system.
SOLUTION PROVIDER: Bilz Tool Co. Inc., (847) 734-9390, www.bilzusa.com.
Implants and supports in the vertebrae are helping more patients overcome a common disorder: back pain. In many cases, the prosthesis eliminates the need for surgically induced stiffening of the vertebrae in the affected area, allowing the the body to retain its flexibility.
Because they are corrosion-resistant and the human body tolerates them, titanium alloys are common materials for prosthetic components. In addition, titanium alloys withstand the high stresses exerted on the components, enabling them to continue to function faultlessly for extended periods.
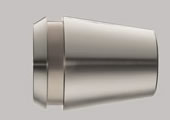
After switching to the TER shrink-fit collet and collet chuck system from Bilz, ulrich medical increased tool life 300 percent.
After a surgery, an oxide layer develops on the surface of an implant, a “passivating effect.” This prevents titanium from passing into the body.
One manufacturer of these vertebrae implants and supports is ulrich medical, Ulm, Germany, which also has a facility in Chesterfield, Mo. The company produces vertebral supports made of Ti6Al4V. Machining the difficult-to-cut workpiece material was limiting tool life to 500 pieces, after which the tools imparted an unacceptable surface finish.
Applied on an INDEX G 200 horizontal lathe, the cutting tools were held in a 10mm ER25 collet for roughing and a 6mm ER25 collet for finishing. Roughing was performed at a cutting speed of 50.24 m/min. (164.8 sfm) and a feed rate of 0.08 mm/min. (0.003 ipm). Cutting time when roughing consumed 75 seconds. Finishing took 20 seconds at a speed of 75.36 m/min. (247.2 sfm) and a feed of 0.05 mm/min. (0.002 ipm).
Seeking to extend tool life, the medical parts manufacturer turned to toolholder manufacturer Bilz Werkzeugfabrik GmbH & Co. KG, Ostifildern, Germany, the parent company of Lombard, Ill.-based Bilz Tool Co. Inc. Bilz recommended its TER1000/25 shrink-fit collet and collet chuck system for roughing and its TER0600/25 for finishing.
Although the cutting speed when roughing remained the same, the medical parts manufacturer increased the feed rate when roughing to 0.2 mm/min. (0.008 ipm) and the finishing speed and feed to 84.78 m/min. (278.1 sfm) and 0.06 mm/min. (0.002 ipm), respectively, after switching to the TER shrink-fit system. In addition, cutting time dropped to 30 seconds when roughing and 17 seconds when finishing—a 50.5 percent decrease—and tool life increased 300 percent, enabling one tool to produce 1,500 parts.
Based on a machine cost of just under $4/min., ulrich medical saves more than $4,750 on each 1,500-part run of the titanium vertebral supports.
Related Glossary Terms
- alloys
alloys
Substances having metallic properties and being composed of two or more chemical elements of which at least one is a metal.
- chuck
chuck
Workholding device that affixes to a mill, lathe or drill-press spindle. It holds a tool or workpiece by one end, allowing it to be rotated. May also be fitted to the machine table to hold a workpiece. Two or more adjustable jaws actually hold the tool or part. May be actuated manually, pneumatically, hydraulically or electrically. See collet.
- collet
collet
Flexible-sided device that secures a tool or workpiece. Similar in function to a chuck, but can accommodate only a narrow size range. Typically provides greater gripping force and precision than a chuck. See chuck.
- cutting speed
cutting speed
Tangential velocity on the surface of the tool or workpiece at the cutting interface. The formula for cutting speed (sfm) is tool diameter 5 0.26 5 spindle speed (rpm). The formula for feed per tooth (fpt) is table feed (ipm)/number of flutes/spindle speed (rpm). The formula for spindle speed (rpm) is cutting speed (sfm) 5 3.82/tool diameter. The formula for table feed (ipm) is feed per tooth (ftp) 5 number of tool flutes 5 spindle speed (rpm).
- feed
feed
Rate of change of position of the tool as a whole, relative to the workpiece while cutting.
- lathe
lathe
Turning machine capable of sawing, milling, grinding, gear-cutting, drilling, reaming, boring, threading, facing, chamfering, grooving, knurling, spinning, parting, necking, taper-cutting, and cam- and eccentric-cutting, as well as step- and straight-turning. Comes in a variety of forms, ranging from manual to semiautomatic to fully automatic, with major types being engine lathes, turning and contouring lathes, turret lathes and numerical-control lathes. The engine lathe consists of a headstock and spindle, tailstock, bed, carriage (complete with apron) and cross slides. Features include gear- (speed) and feed-selector levers, toolpost, compound rest, lead screw and reversing lead screw, threading dial and rapid-traverse lever. Special lathe types include through-the-spindle, camshaft and crankshaft, brake drum and rotor, spinning and gun-barrel machines. Toolroom and bench lathes are used for precision work; the former for tool-and-die work and similar tasks, the latter for small workpieces (instruments, watches), normally without a power feed. Models are typically designated according to their “swing,” or the largest-diameter workpiece that can be rotated; bed length, or the distance between centers; and horsepower generated. See turning machine.
- toolholder
toolholder
Secures a cutting tool during a machining operation. Basic types include block, cartridge, chuck, collet, fixed, modular, quick-change and rotating.