END USER: DPI Inc., (215) 953-9800, www.dpicnc.com.
CHALLENGE: Eliminate unpredictable and premature tool chipping and enhance consistency and chip control when drilling 304 stainless steel.
SOLUTION: An adjustable drill that accepts double-sided indexable inserts with six cutting edges.
SOLUTION PROVIDERS: Tungaloy America Inc., (888) 554-8394, www.tungaloyamerica.com. Tri-State Industrial Supplies of PA Inc., (215) 340-1911, www.tristateofpa.com.
DPI Inc. is a job shop that specializes in making flanged cylinders. One ongoing job requires drilling a 3.150" (80.01mm) hole in 304 stainless steel 4½" (114.3mm) deep on its Hitachi Seiki 25G 2-axis lathe and then flipping the part to drill a hole with the same dimensions from the other side and achieve a concentricity and diameter tolerance of ±0.005" (0.127mm).
The task of drilling the difficult-to-machine material was compounded when DPI experienced unpredictable and premature tool chipping, uncontrollable chips wrapping around the drill and inconsistent horsepower draw during drilling, explained Lance Zeitz, vice president of operations and foreman for the Huntingdon Valley, Pa., shop. He added that the horsepower fluctuated by about 20 percent, which caused the indexable-insert drill to impart a rough surface finish and shortened insert life. It also made holding size a challenge and, therefore, required leaving extra material for finish boring.
The machining parameters were a cutting speed of 400 sfm (121.9 m/min.) and a feed from 0.0030 to 0.0040 ipr (0.076 mm/rev. to 0.102 mm/rev.), depending on the material heat lot.
Seeking a solution, Zeitz consulted with Leo Fitzpatrick, a salesman at distributor Tri-State Industrial Supplies of PA Inc., New Britain, Pa. Fitzpatrick felt confident that Tungaloy Corp. offered a drill to do the job but the Japan- headquartered toolmaker was not going to release the drill in the size DPI needed for 9 months. “I waited 9 months and bought the first four cartridges they brought into the country,” Zeitz said.
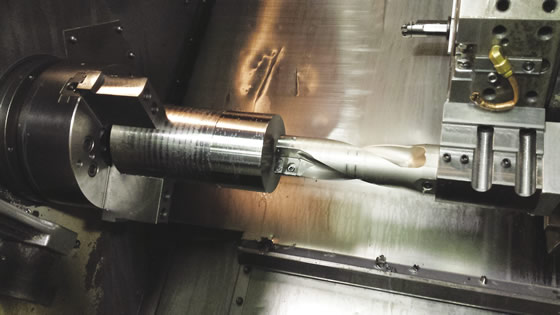
A TungDrillBig drill tooled with TungSix-Drill inserts from Tungaloy prepares to cut a 304 stainless steel workpiece at DPI.
Albert Anelli, regional sales engineer for Tungaloy America Inc., Arlington Height, Ill., added that he needed to “beg, borrow and get creative to make sure Lance got what he needed to outfit his shop first.”
The drills for large-diameter holes are from the TungDrillBig series, which have new replaceable cartridges to accept TungSix-Drill WWMU-type indexable inserts with six cutting edges. The cartridges are also adjustable, enabling any of the five available tool bodies to produce multiple hole sizes.
For the 304 stainless application, DPI applies a 3.0" (76.2mm) drill, offset to 3.150" (80.01mm), at a cutting speed of 660 sfm (201.17 m/min.) and a feed rate of 0.0048 ipr (0.1219 mm/rev.), or 3.84 ipm (97.54 mm/min.). The speed is the maximum surface footage Tungaloy recommends. Although the maximum recommended feed is 5.0 ipm (127 mm/min.), DPI runs slightly lower during production to ensure chips don’t wrap around the tool or overload the conveyor, Zeitz noted. “We tested it at up to 0.0055 ipr and the drill took it.”
Establishing those parameters for production holemaking was quick and painless, Zeitz said. “This drill is plug-and-play. With other drills I’ve had, it takes time to adjust them and get the speed, feed and offset to where they run best.”
Compared to producing about 30 holes before indexing an insert with the previous drill, DPI can drill up to 100 holes, or 450" (11,430mm) of material, per edge with the new tool, Zeitz said. “I’m indexing the insert before it needs to be until I get more of a track record.” The longer tool life is because chipping is not a problem for an insert’s chamfered center edge at the drill center, where the cutting speed is zero, he added. “This drill has an extremely innovative insert design, which solved the problem. It’s really an excellent piece of engineering.”
DPI doesn’t peck when applying the TungDrillBig drill, and, regardless of the brand of carbide drill, Zeitz doesn’t recommend pecking because it shortens tool life when the hard, brittle cutting edges repeatedly enter and exit the cut. Nonetheless, he noted operators have a tendency to change the program and peck to prevent chip wrapping, particularly when drilling copper but also when making holes in stainless. That’s understandable because it can take a couple minutes to remove the chips using a chip hook after machining a part.
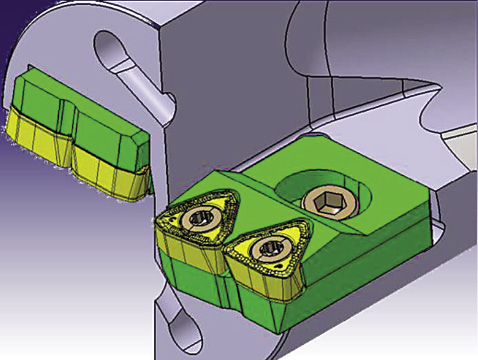
Tungaloy’s TungDrillBig drill body accepts TungSix-Drill indexable inserts with six cutting edges, and its diameter can be adjusted with the use of setting plates.
To enhance chip evacuation, the Tungaloy drill bodies supply coolant directly to the cutting edge, according to the toolmaker. “The coolant is ported right where it’s supposed to be,” Zeitz added, noting the lathe supplies coolant at 40 psi (2.76 bar). “In these larger holes, it’s more about volume than pressure.”
Zeitz appreciates that all four pockets in the drill accept the same insert instead of one insert for an inside pocket and another for an outside pocket. The only difference is the cutting edge on the outside insert wears a bit faster because it removes more metal. He added that the chip shape varies, depending on insert location. The center insert generates tightly curled chips, the outside insert produces chips with kinks and chips from the two inboard inserts flow like ribbons.
In addition, unlike when drilling with the previous tool, DPI sees minimal fluctuation in horsepower draw using the Tungaloy offering. This enables finishing the holes with four boring passes to achieve the ±0.002" (0.051mm) concentricity and size tolerances and impart a 16-rms finish on a thin wall.
An additional advantage of the TungDrillBig can be heard—or rather not heard. “The drills I used in the past would scream,” Zeitz said. “We would push them until you needed to wear earplugs. Jose Prunes, the setup guy and operator, said, ‘This drill is stealth.’ It makes for much better shop conditions. Another advantage to the Tungaloy drill is when something goes wrong, such as chips building up, the drill holds up compared to previous drills, which melted and were unusable.”
Related Glossary Terms
- boring
boring
Enlarging a hole that already has been drilled or cored. Generally, it is an operation of truing the previously drilled hole with a single-point, lathe-type tool. Boring is essentially internal turning, in that usually a single-point cutting tool forms the internal shape. Some tools are available with two cutting edges to balance cutting forces.
- coolant
coolant
Fluid that reduces temperature buildup at the tool/workpiece interface during machining. Normally takes the form of a liquid such as soluble or chemical mixtures (semisynthetic, synthetic) but can be pressurized air or other gas. Because of water’s ability to absorb great quantities of heat, it is widely used as a coolant and vehicle for various cutting compounds, with the water-to-compound ratio varying with the machining task. See cutting fluid; semisynthetic cutting fluid; soluble-oil cutting fluid; synthetic cutting fluid.
- cutting speed
cutting speed
Tangential velocity on the surface of the tool or workpiece at the cutting interface. The formula for cutting speed (sfm) is tool diameter 5 0.26 5 spindle speed (rpm). The formula for feed per tooth (fpt) is table feed (ipm)/number of flutes/spindle speed (rpm). The formula for spindle speed (rpm) is cutting speed (sfm) 5 3.82/tool diameter. The formula for table feed (ipm) is feed per tooth (ftp) 5 number of tool flutes 5 spindle speed (rpm).
- feed
feed
Rate of change of position of the tool as a whole, relative to the workpiece while cutting.
- inches per minute ( ipm)
inches per minute ( ipm)
Value that refers to how far the workpiece or cutter advances linearly in 1 minute, defined as: ipm = ipt 5 number of effective teeth 5 rpm. Also known as the table feed or machine feed.
- lathe
lathe
Turning machine capable of sawing, milling, grinding, gear-cutting, drilling, reaming, boring, threading, facing, chamfering, grooving, knurling, spinning, parting, necking, taper-cutting, and cam- and eccentric-cutting, as well as step- and straight-turning. Comes in a variety of forms, ranging from manual to semiautomatic to fully automatic, with major types being engine lathes, turning and contouring lathes, turret lathes and numerical-control lathes. The engine lathe consists of a headstock and spindle, tailstock, bed, carriage (complete with apron) and cross slides. Features include gear- (speed) and feed-selector levers, toolpost, compound rest, lead screw and reversing lead screw, threading dial and rapid-traverse lever. Special lathe types include through-the-spindle, camshaft and crankshaft, brake drum and rotor, spinning and gun-barrel machines. Toolroom and bench lathes are used for precision work; the former for tool-and-die work and similar tasks, the latter for small workpieces (instruments, watches), normally without a power feed. Models are typically designated according to their “swing,” or the largest-diameter workpiece that can be rotated; bed length, or the distance between centers; and horsepower generated. See turning machine.
- tolerance
tolerance
Minimum and maximum amount a workpiece dimension is allowed to vary from a set standard and still be acceptable.