Continuing the theme of December’s column, this month’s column provides more tips for enhancing the operation of a manual milling machine.
• Sometimes it’s faster and easier to make a quick drill fixture to drill and tap holes in the edges of large plates. Otherwise, the setup time and handling can be murderous for just a few holes. Make the block an accurate size so you can locate it precisely on the plate.
• A “poor man’s” knee rapid feed saves you quite a bit of time over the course of a year (see photo, right). It has wrench flats on the shank so you can still make fine adjustments with a wrench. Nobody can say I’m not a cheapskate.
• Once a part is completed, cut it off with a slitting saw or keyseat cutter. This works particularly well for small parts (see photo, opposite page). Be sure to keep your eye on the part when it comes off or you might spend more time looking for the part than it took to make it.
• Use a right-angle head like a precision cold saw to neatly and accurately cut parts to length. This is an effective use of a retractable stop to eliminate parts jamming between the stop and the blade. Use blades with enough thickness to cut straight. You should be able to cut parts within 0.002 ". Make sure the bottom of the right-angle head clears the parts and the vise. Also, be sure to retract your stop before the part comes off or it may jam.
• You can quickly align the right-angle head if the vise is positioned correctly. With the clamp screws for the head lightly clamping the body, drop the head into the jaws of the vise and snug the vise slightly. For fussy work, you will still want to indicate the head for perfect alignment. By the way, don’t trust the flats on the side for fussy work. Indicate a test bar held in a collet.
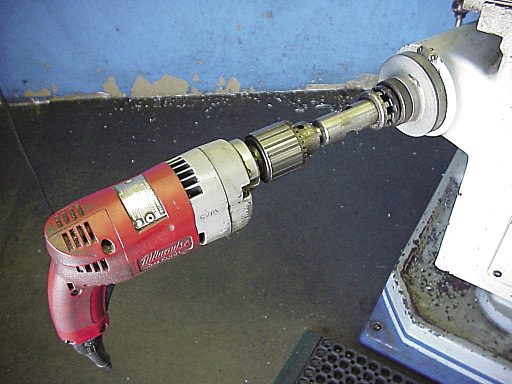
Courtesy of All images: T. Lipton
A “poor man’s” knee rapid feed saves you quite a bit of time over the course of a year.
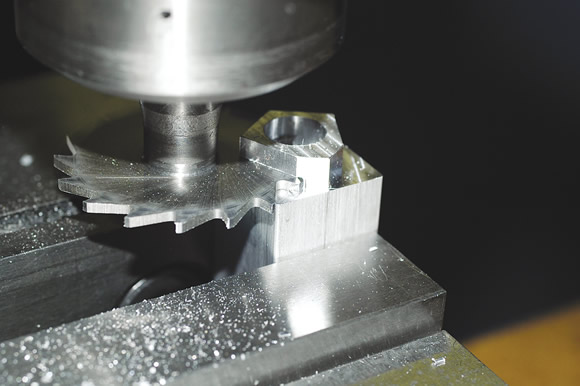
Once a part is completed, cut it off with a slitting saw or keyseat cutter. This works particularly well for small parts.
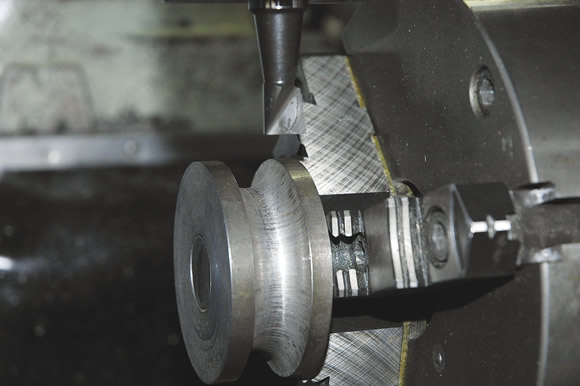
Cut odd radii, such as a tube-bending die for an odd centerline radius, with a boring head.
• Cut odd radii, such as a tube-bending die for an odd centerline radius, with a boring head. Such a part can be rotated by the rotary table with the boring tool’s cutting edge on the centerline.
• Cut chamfers with a standard countersink. Stay off the tip for best results.
• Place a piece of brown paper under plates clamped to the mill table. This bit of paper acts like a brake lining to keep a part from slipping.
• Try using annular cutters when holemaking. They produce accurate holes and need a fraction of the feed pressure to effectively cut compared to drill bits. You also create a neat little slug, which you can use to make something else. In addition, annular cutters are more efficient than drill bits. The cutting speed of a standard drill bit approaches zero at the tip. Essentially, the center portion of a drill bit is broaching its way through the material. Annular cutters maintain a more uniform cutting speed and convert more energy into the hole and less energy into chips. However, you should not stack-cut with annular cutters.
• Annular cutters could care less if they cut a full hole or some fractional part of one. The helical flutes on the outside of the cutters extract the chips, unlike a hole saw.
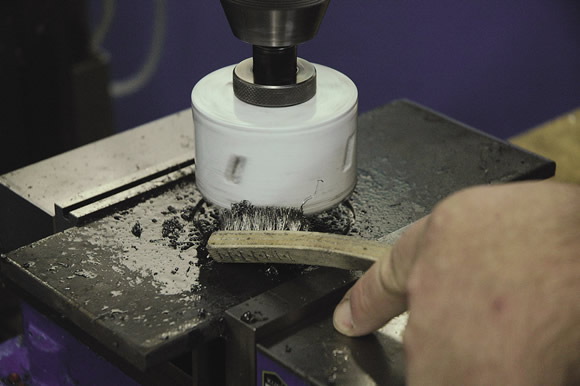
After two pecks, clean the teeth of a hole saw with a small wire brush or air hose while it’s running.
• When applying hole saws in a mill, only stay in the cut for about 3 seconds at a time, backing the saw out after each 3-second peck. After two pecks, clean the teeth of the hole saw with a small wire brush or air hose while it’s running. This clears the chips out of the teeth and keeps the tool cutting. Also, predrill one to four holes in the saw groove to break the chips and strip them out of the teeth.
• Mill your blocks square with the end cutting surface of the tool. Less tool flex improves part quality.
• Check flatness of parts with a three-point leveling system. Level the underside datum to the same indicator reading. Then sweep the top surface of the part, flip and repeat.
• Use a V-block for holding round stuff in a mill vise. It provides three-point contact and automatically and accurately squares the stock to the jaw. An extra tall V-block can be set up with a couple of angle plates. One advantage of doing this is it allows setting up any desired angle between the two plates. Be sure to indicate the faces vertically to ensure they are straight. You can also leave a space between the plates for clamping purposes.
• You also can make a soft jaw that has a V-groove already in it when three-point holding various round items. CTE
About the Author: Tom Lipton is a career metalworker who has worked at various job shops that produce parts for the consumer product development, laboratory equipment, medical services and custom machinery design industries. He has received six U.S. patents and lives in Alamo, Calif. Lipton’s column is adapted from information in his book “Metalworking Sink or Swim: Tips and Tricks for Machinists, Welders, and Fabricators,” published by Industrial Press Inc., New York. The publisher can be reached by calling (888) 528-7852 or visiting www.industrialpress.com. By indicating the code CTE-2013 when ordering, CTE readers will receive a 20 percent discount off the book’s list price of $44.95.
Related Glossary Terms
- V-block
V-block
Workholding device with V-shaped slot for holding pipe and other round stock during machining or inspection.
- backing
backing
1. Flexible portion of a bandsaw blade. 2. Support material behind the cutting edge of a tool. 3. Base material for coated abrasives.
- boring
boring
Enlarging a hole that already has been drilled or cored. Generally, it is an operation of truing the previously drilled hole with a single-point, lathe-type tool. Boring is essentially internal turning, in that usually a single-point cutting tool forms the internal shape. Some tools are available with two cutting edges to balance cutting forces.
- boring head
boring head
Single- or multiple-point precision tool used to bring an existing hole within dimensional tolerance. The head attaches to a standard toolholder and a mechanism permits fine adjustments to be made to the head within a diameter range.
- broaching
broaching
Operation in which a cutter progressively enlarges a slot or hole or shapes a workpiece exterior. Low teeth start the cut, intermediate teeth remove the majority of the material and high teeth finish the task. Broaching can be a one-step operation, as opposed to milling and slotting, which require repeated passes. Typically, however, broaching also involves multiple passes.
- collet
collet
Flexible-sided device that secures a tool or workpiece. Similar in function to a chuck, but can accommodate only a narrow size range. Typically provides greater gripping force and precision than a chuck. See chuck.
- countersink
countersink
Tool that cuts a sloped depression at the top of a hole to permit a screw head or other object to rest flush with the surface of the workpiece.
- cutting speed
cutting speed
Tangential velocity on the surface of the tool or workpiece at the cutting interface. The formula for cutting speed (sfm) is tool diameter 5 0.26 5 spindle speed (rpm). The formula for feed per tooth (fpt) is table feed (ipm)/number of flutes/spindle speed (rpm). The formula for spindle speed (rpm) is cutting speed (sfm) 5 3.82/tool diameter. The formula for table feed (ipm) is feed per tooth (ftp) 5 number of tool flutes 5 spindle speed (rpm).
- feed
feed
Rate of change of position of the tool as a whole, relative to the workpiece while cutting.
- fixture
fixture
Device, often made in-house, that holds a specific workpiece. See jig; modular fixturing.
- flutes
flutes
Grooves and spaces in the body of a tool that permit chip removal from, and cutting-fluid application to, the point of cut.
- gang cutting ( milling)
gang cutting ( milling)
Machining with several cutters mounted on a single arbor, generally for simultaneous cutting.
- gang cutting ( milling)2
gang cutting ( milling)
Machining with several cutters mounted on a single arbor, generally for simultaneous cutting.
- milling
milling
Machining operation in which metal or other material is removed by applying power to a rotating cutter. In vertical milling, the cutting tool is mounted vertically on the spindle. In horizontal milling, the cutting tool is mounted horizontally, either directly on the spindle or on an arbor. Horizontal milling is further broken down into conventional milling, where the cutter rotates opposite the direction of feed, or “up” into the workpiece; and climb milling, where the cutter rotates in the direction of feed, or “down” into the workpiece. Milling operations include plane or surface milling, endmilling, facemilling, angle milling, form milling and profiling.
- milling machine ( mill)
milling machine ( mill)
Runs endmills and arbor-mounted milling cutters. Features include a head with a spindle that drives the cutters; a column, knee and table that provide motion in the three Cartesian axes; and a base that supports the components and houses the cutting-fluid pump and reservoir. The work is mounted on the table and fed into the rotating cutter or endmill to accomplish the milling steps; vertical milling machines also feed endmills into the work by means of a spindle-mounted quill. Models range from small manual machines to big bed-type and duplex mills. All take one of three basic forms: vertical, horizontal or convertible horizontal/vertical. Vertical machines may be knee-type (the table is mounted on a knee that can be elevated) or bed-type (the table is securely supported and only moves horizontally). In general, horizontal machines are bigger and more powerful, while vertical machines are lighter but more versatile and easier to set up and operate.
- milling machine ( mill)2
milling machine ( mill)
Runs endmills and arbor-mounted milling cutters. Features include a head with a spindle that drives the cutters; a column, knee and table that provide motion in the three Cartesian axes; and a base that supports the components and houses the cutting-fluid pump and reservoir. The work is mounted on the table and fed into the rotating cutter or endmill to accomplish the milling steps; vertical milling machines also feed endmills into the work by means of a spindle-mounted quill. Models range from small manual machines to big bed-type and duplex mills. All take one of three basic forms: vertical, horizontal or convertible horizontal/vertical. Vertical machines may be knee-type (the table is mounted on a knee that can be elevated) or bed-type (the table is securely supported and only moves horizontally). In general, horizontal machines are bigger and more powerful, while vertical machines are lighter but more versatile and easier to set up and operate.
- sawing machine ( saw)
sawing machine ( saw)
Machine designed to use a serrated-tooth blade to cut metal or other material. Comes in a wide variety of styles but takes one of four basic forms: hacksaw (a simple, rugged machine that uses a reciprocating motion to part metal or other material); cold or circular saw (powers a circular blade that cuts structural materials); bandsaw (runs an endless band; the two basic types are cutoff and contour band machines, which cut intricate contours and shapes); and abrasive cutoff saw (similar in appearance to the cold saw, but uses an abrasive disc that rotates at high speeds rather than a blade with serrated teeth).
- shank
shank
Main body of a tool; the portion of a drill or similar end-held tool that fits into a collet, chuck or similar mounting device.
- tap
tap
Cylindrical tool that cuts internal threads and has flutes to remove chips and carry tapping fluid to the point of cut. Normally used on a drill press or tapping machine but also may be operated manually. See tapping.