Translating machine tool axes are often driven by screws attached to the rotor of a motor by a coupling, with the motor attached to the fixed frame of the machine. A nut is attached to the moving element, such as a table or carriage, and is fixed so it cannot rotate. When the screw rotates, the nut and the attached moving element translate along the length of the screw.
In this configuration, the screw is called a lead screw. The screw has a large mechanical advantage, meaning its thrust capacity is high. In designs where more turns of the screw are required for a given linear translation, the mechanical advantage and load capacity are higher. Lead screws are stiff because the thrust load is carried on the large contact area between the threads.
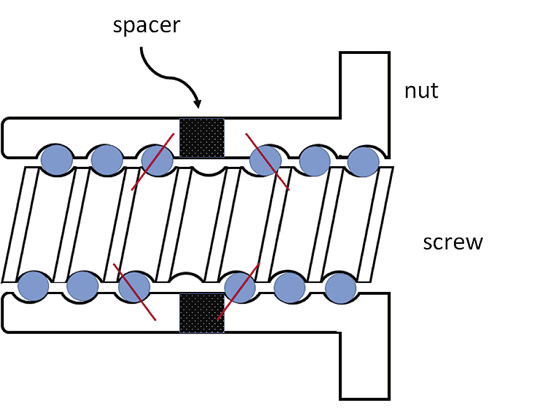
Figure 1. A split-nut, spacer-preloaded ball nut.
However, lead screws in this configuration have two significant limitations:
1. The motor has to overcome a significant amount of friction as the screw and nut slide against each other, and the friction generates heat. This heat, in turn, thermally deforms the screw and machine, reducing accuracy.
2. A clearance must exist between the screw threads and nut threads such that only one side contacts at a time. Typically, the position feedback is on the motor, not the translating slide. As a result, when the screw reverses direction, the slide remains stationary as the screw turns and makes contact with the other side of the nut thread. The controller thinks the slide moved, but the slide remained stationary. This is called backlash. A trade-off always exists between machine accuracy (and stiffness) and cost. Some controllers use backlash compensation, so whenever the axis reverses direction, additional motion is commanded to compensate for the measured backlash.
To reduce friction, balls are often introduced between the screw and nut. When the screw rotates, the balls roll, as in a ball bearing. The balls roll through the nut from one end to the other, then are collected into a tube that transports them back to the start of the nut. This configuration is called a recirculating ballscrew. The balls dramatically reduce friction and heat generation, but they also reduce stiffness. The balls act as springs, but they do not exhibit a linear relationship between force and deflection like coil springs do. Rather, because the contact exists only at small points on opposite sides of the balls, a small deflection only requires a small force. As the deflection increases, the force required to cause the deflection quickly increases, and stiffness goes up.
A preload, which would keep the balls in a compressed condition all the time would increase stiffness and eliminate backlash. So how can it be arranged? There are four basic ways: a split nut with a spacer, a split nut with a spring, a variable thread pitch and oversized balls.
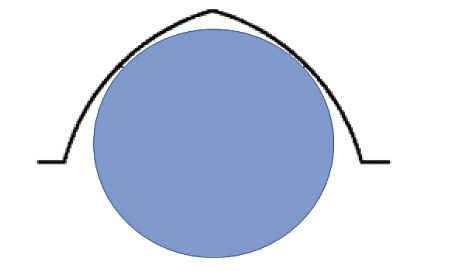
Figure 2. A ball makes contact with two points in a Gothic- arch thread.
Figure 1 shows a cross-section of a split nut with a spacer mounted on the screw. The left and right portions of the nut are separated by a spacer, whose dimension is carefully chosen and controlled to preload the balls on the left of the figure toward the left and preload the balls on the right of the figure toward the right. The red lines in the figure indicate the lines along which the balls are compressed.
This design is inexpensive and robust. However, if the screw does not have a perfect pitch and the balls are not the exact same size, the preload changes and the stiffness of the ballscrew changes as it rotates. Even small errors in the geometry can cause large changes in the stiffness. One way to fix this problem is to replace the spacer with a stiff linear spring (split nut with a spring). The spring keeps the balls compressed with a constant preload, even if there are small errors in the geometry. This design keeps the ballscrew stiffness more constant, but it is more expensive.
Variable thread pitch means the spacing of the threads on the screw and nut are not quite the same. If the difference is too great, the screw could not rotate in the nut. However, if the difference is small, the change in pitch preloads the balls in opposite directions over the length of the nut. This design can be compact, but it is difficult to fabricate, and some balls are preloaded more than others.
When oversized balls are used, they are slightly larger than the gap between the screw and nut. In addition, the threads of the screw and nut are not circular in profile, but are created in the form of a Gothic arch. This means the sides are parts of circles, but the circles have different centers. As a result, an oversize ball makes contact with the thread in two places on the nut and two places on the screw (Figure 2). This design is compact and stiff, but generates higher friction and has shorter life than the others.
The choice of preload mechanism in a modern ballscrew is a compromise that balances friction, heat generation, stiffness, backlash, load capacity and bearing life. CTE
About the Author: Dr. Scott Smith is a professor and chair of the Department of Mechanical Engineering at the William States Lee College of Engineering, University of North Carolina at Charlotte, specializing in machine tool structural dynamics. Contact him via e-mail at [email protected].Related Glossary Terms
- backlash
backlash
Reaction in dynamic motion systems where potential energy that was created while the object was in motion is released when the object stops. Release of this potential energy or inertia causes the device to quickly snap backward relative to the last direction of motion. Backlash can cause a system’s final resting position to be different from what was intended and from where the control system intended to stop the device.
- centers
centers
Cone-shaped pins that support a workpiece by one or two ends during machining. The centers fit into holes drilled in the workpiece ends. Centers that turn with the workpiece are called “live” centers; those that do not are called “dead” centers.
- clearance
clearance
Space provided behind a tool’s land or relief to prevent rubbing and subsequent premature deterioration of the tool. See land; relief.
- pitch
pitch
1. On a saw blade, the number of teeth per inch. 2. In threading, the number of threads per inch.
- stiffness
stiffness
1. Ability of a material or part to resist elastic deflection. 2. The rate of stress with respect to strain; the greater the stress required to produce a given strain, the stiffer the material is said to be. See dynamic stiffness; static stiffness.