END USER: Profiroll Technologies GmbH, +49 34243-74-270, www.profiroll.de.
CHALLENGE: Increase threading productivity while reducing scrap.
SOLUTION: High-performance, through-coolant thread formers.
SOLUTION PROVIDER: Walter USA LLC, (800) 945-5554, www.walter-tools.com/us.
To ensure process reliability, Profiroll Technologies GmbH, Bad Düben, Germany, a manufacturer of machines and tools for profiling rotationally symmetrical workpieces, is increasingly applying thread formers instead of conventional taps.
With its profile rolling machines, the company manufactures a range of products, including base plates for linear guides. The base plates are made from difficult-to-cut A-36 steel and measure up to 3m (9.8 ') long and 16mm to 20mm (0.63 " to 0.79 ") thick. They require up to 90 M5 or M6 through-hole threads.
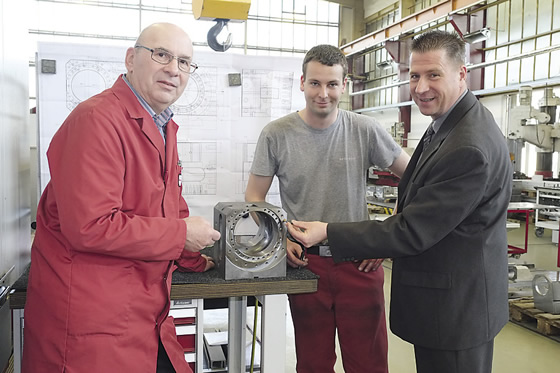
Courtesy of Walter USA
Left to right: Arno Deutrich, process planning officer at Profiroll, Andre Knofel, machine operator, and Thomas Neugebauer, technical support and sales for Walter.
Profiroll found fluctuations in material quality often made deep-hole tapping difficult. Chips can get jammed and cutting forces can fluctuate when tapping, increasing the risk of tool breakage. In the worst-case scenario, a tool breaks and the resulting tool steel fragments can be removed only by EDMing.
This is time-consuming, expensive and provides no guarantee of complete success, as hard particles often remain in the workpiece material. Therefore, process reliability became a top priority when thread cutting.
To avoid putting the process at risk, machine operators opted for slower feeds and speeds, and pecking was employed, so threads were actually cut in stages. “By working that way, tool life was reduced, because taps rub against the wall of the hole when they are withdrawn and wear out quickly,” explained Arno Deutrich, process planning officer.
“Some years ago, we thought about using thread formers for this application, but we didn’t have the right machine,” said Peter Zintl, division manager in production.
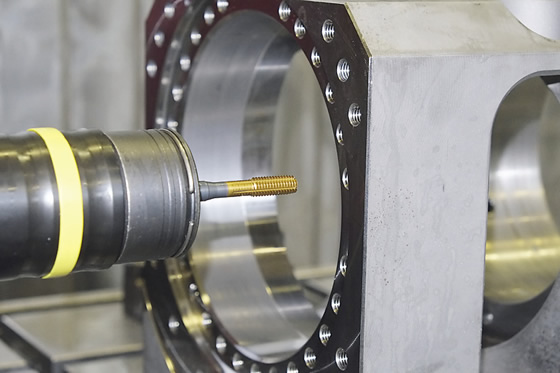
Courtesy of Walter USA
This bearing housing is made of heat-treated steel and requires around 50 M8 threaded holes. Thread formers are used up to a depth of 5 diameters deep.
For short work cycles, older machines are usually not capable of accelerating the spindle from zero to the nominal rotation speed in just a few seconds. This is a prerequisite for cost-effectively using high-performance thread formers, because valuable time is lost while the spindle comes up to speed. Running at less than full speed is possible, but not advisable.
“If the cutting speed is too low, the material does not ‘flow’ ideally when formed and tools wear more quickly,” said Thomas Neugebauer, technical support and sales with Walter AG, Tübingen, Germany, Profiroll’s tooling partner. (Walter USA LLC is based in Waukesha, Wis.)
The situation changed when Profiroll acquired a new SHW UniSpeed 7 universal machining center, enabling the use of high-performance thread formers. To allow Profiroll to work with both maximum process reliability and optimal productivity, Neugebauer recommended Walter’s Prototyp Protodyn S Eco Plus thread formers with internal cooling and radial outlets. Coated with wear-resistant TiN and finished with a subsequent steam treatment, these tools can operate at around three times the cutting speed of the previous taps, according to Walter.
The result? Profiroll reduced machining time by 70 percent. In addition, machine operators no longer need be concerned about the variations in machinability of A-36 and can have greater confidence in the reliability of their process because the thread formers show virtually no signs of wear even after several months of use.
Profiroll racked up even greater savings with the Walter tools when generating M8 threads in bearing housings made of heat-treated C-45 or 4142 on a Matec 40-HV machining center machine. Most of the threads (approximately 50) are blind-hole threads up to a depth of 5 diameters deep. “Overall, machining time is reduced by 20 minutes per component,” said Profiroll’s Deutrich.
“Switching over to the new threading technology has been a milestone for our production department,” Deutrich said.
Related Glossary Terms
- blind-hole
blind-hole
Hole or cavity cut in a solid shape that does not connect with other holes or exit through the workpiece.
- cutting speed
cutting speed
Tangential velocity on the surface of the tool or workpiece at the cutting interface. The formula for cutting speed (sfm) is tool diameter 5 0.26 5 spindle speed (rpm). The formula for feed per tooth (fpt) is table feed (ipm)/number of flutes/spindle speed (rpm). The formula for spindle speed (rpm) is cutting speed (sfm) 5 3.82/tool diameter. The formula for table feed (ipm) is feed per tooth (ftp) 5 number of tool flutes 5 spindle speed (rpm).
- machinability
machinability
The relative ease of machining metals and alloys.
- machining center
machining center
CNC machine tool capable of drilling, reaming, tapping, milling and boring. Normally comes with an automatic toolchanger. See automatic toolchanger.
- profiling
profiling
Machining vertical edges of workpieces having irregular contours; normally performed with an endmill in a vertical spindle on a milling machine or with a profiler, following a pattern. See mill, milling machine.
- tapping
tapping
Machining operation in which a tap, with teeth on its periphery, cuts internal threads in a predrilled hole having a smaller diameter than the tap diameter. Threads are formed by a combined rotary and axial-relative motion between tap and workpiece. See tap.
- threading
threading
Process of both external (e.g., thread milling) and internal (e.g., tapping, thread milling) cutting, turning and rolling of threads into particular material. Standardized specifications are available to determine the desired results of the threading process. Numerous thread-series designations are written for specific applications. Threading often is performed on a lathe. Specifications such as thread height are critical in determining the strength of the threads. The material used is taken into consideration in determining the expected results of any particular application for that threaded piece. In external threading, a calculated depth is required as well as a particular angle to the cut. To perform internal threading, the exact diameter to bore the hole is critical before threading. The threads are distinguished from one another by the amount of tolerance and/or allowance that is specified. See turning.
- through-hole
through-hole
Hole or cavity cut in a solid shape that connects with other holes or extends all the way through the workpiece.
- titanium nitride ( TiN)
titanium nitride ( TiN)
Added to titanium-carbide tooling to permit machining of hard metals at high speeds. Also used as a tool coating. See coated tools.