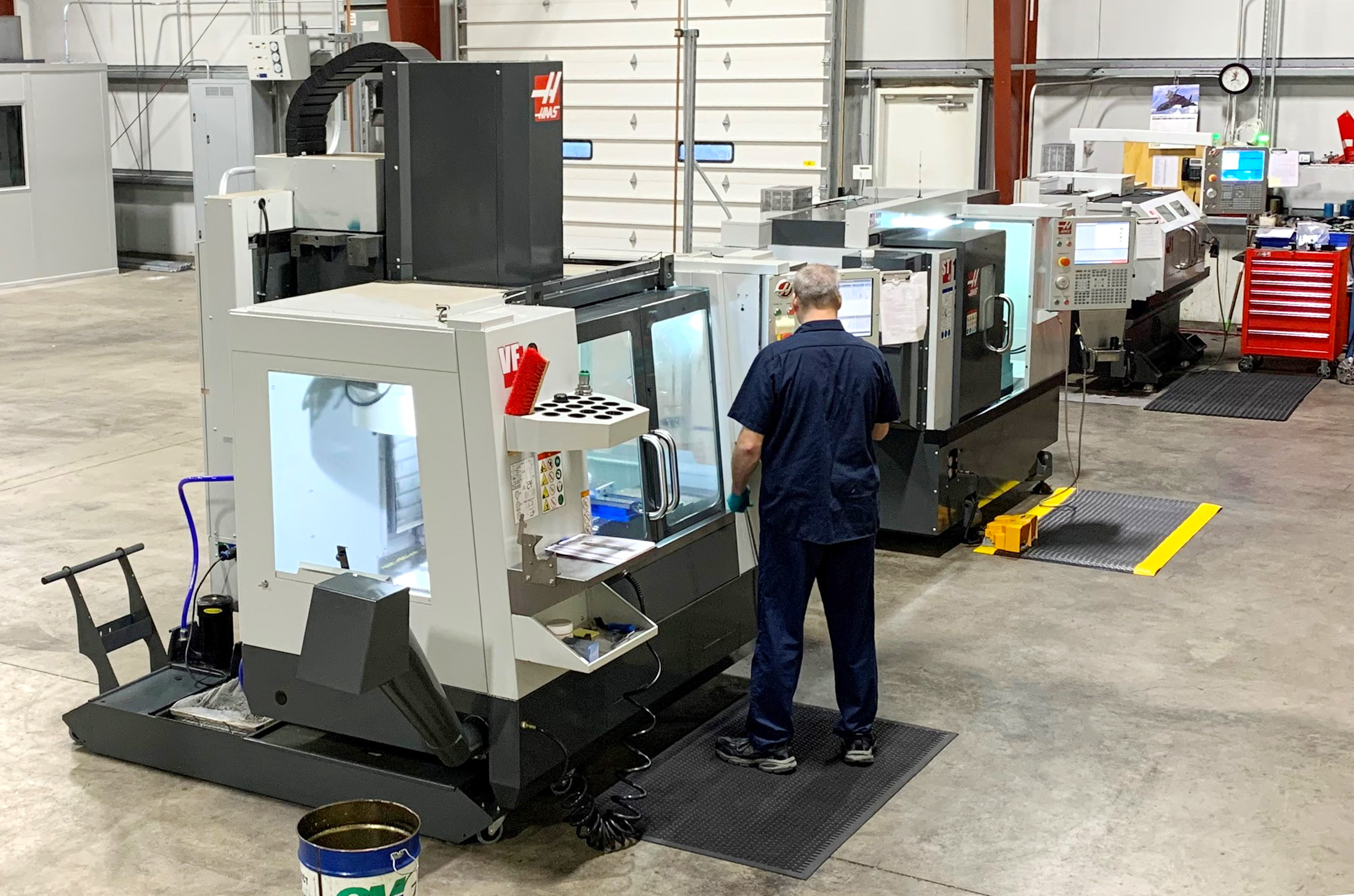
To support rapid growth within its mechanical testing department, Hermitage, Pennsylvania-based Solar Atmospheres of Western Pennsylvania has invested in a new Haas ST-10 CNC lathe.
The Haas ST-10’s 6,000-rpm spindle features an automatic toolchanger with a 12-station, bolt-on tool turret, allowing Solar’s machining center to automatically change tools at the push of a button. This capability results in significant time- and cost-savings over Solar’s original TL-1 Haas lathe, which requires up to five manual tool changes to produce one tensile specimen. The investment in an automated lathe results in a 50% savings in the production of a variety of round tensile specimens. The TL-1 lathe will be retained as back-up in the case of an unexpected breakdown.
The increased machining efficiency of the Haas ST-10 improves turnaround for the customer at the final stage in the thermal process, obtaining the tensile test results of processed materials. Previously performed by an outside company, the opportunity to bring this testing in-house saves the customer time and money.
Bob Hill, president of Solar Atmospheres of Western Pennsylvania, said, “This new CNC machining center will ultimately support our overall goal of becoming Nadcap Laboratory Testing AC 7101 approved. We have learned in the past that keeping these processes in-house is a benefit not just to Solar, but to our customers as well.”
Contact Details
Related Glossary Terms
- automatic toolchanger
automatic toolchanger
Mechanism typically included in a machining center that, on the appropriate command, removes one cutting tool from the spindle nose and replaces it with another. The changer restores the used tool to the magazine and selects and withdraws the next desired tool from the storage magazine. The changer is controlled by a set of prerecorded/predetermined instructions associated with the part(s) to be produced.
- computer numerical control ( CNC)
computer numerical control ( CNC)
Microprocessor-based controller dedicated to a machine tool that permits the creation or modification of parts. Programmed numerical control activates the machine’s servos and spindle drives and controls the various machining operations. See DNC, direct numerical control; NC, numerical control.
- lathe
lathe
Turning machine capable of sawing, milling, grinding, gear-cutting, drilling, reaming, boring, threading, facing, chamfering, grooving, knurling, spinning, parting, necking, taper-cutting, and cam- and eccentric-cutting, as well as step- and straight-turning. Comes in a variety of forms, ranging from manual to semiautomatic to fully automatic, with major types being engine lathes, turning and contouring lathes, turret lathes and numerical-control lathes. The engine lathe consists of a headstock and spindle, tailstock, bed, carriage (complete with apron) and cross slides. Features include gear- (speed) and feed-selector levers, toolpost, compound rest, lead screw and reversing lead screw, threading dial and rapid-traverse lever. Special lathe types include through-the-spindle, camshaft and crankshaft, brake drum and rotor, spinning and gun-barrel machines. Toolroom and bench lathes are used for precision work; the former for tool-and-die work and similar tasks, the latter for small workpieces (instruments, watches), normally without a power feed. Models are typically designated according to their “swing,” or the largest-diameter workpiece that can be rotated; bed length, or the distance between centers; and horsepower generated. See turning machine.
- machining center
machining center
CNC machine tool capable of drilling, reaming, tapping, milling and boring. Normally comes with an automatic toolchanger. See automatic toolchanger.
- toolchanger
toolchanger
Carriage or drum attached to a machining center that holds tools until needed; when a tool is needed, the toolchanger inserts the tool into the machine spindle. See automatic toolchanger.