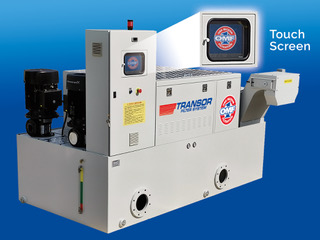
Transor Filter USA has entered into a working relationship with Star Cutter. The relationship includes the promotion of Transor’s One Micron filtration (OMF) system and Star Cutter’s line of tool and cutter grinders.
Both companies will have their technology on display in the Grinding Pavilion at the upcoming IMTS exhibition in Chicago from September 12 -17. Transor will be on display at booth #237440 and Star Su is in booth #237013.
“After several meetings and a presentation made to management and sales staff, Star SU recognized the many benefits that Transor’s patented One Micron filtration brought to their ability to produce both carbide and HSS cutting tools,” said Irv Kaage, Transor CEO. The combination of one-micron filtration and temperature control (0.1º C.) has maximized their productivity.”
Kaage added that Star SU will be offering Transor as a filtration option on its specialized tool and cutter grinders they sell in the marketplace. Plans also include the installation of a Transor unit in its manufacturing facility.
Star Cutter specializes in solid carbide cutting tools, carbide blanks, and preforms, gundrills, and 5-axis CNC tool and cutter grinding machines. In addition, they have a line of gear grinding, hobbing, chamfer/deburring, and vertical turning machines.
Contact Details
Contact Details
Related Glossary Terms
- computer numerical control ( CNC)
computer numerical control ( CNC)
Microprocessor-based controller dedicated to a machine tool that permits the creation or modification of parts. Programmed numerical control activates the machine’s servos and spindle drives and controls the various machining operations. See DNC, direct numerical control; NC, numerical control.
- grinding
grinding
Machining operation in which material is removed from the workpiece by a powered abrasive wheel, stone, belt, paste, sheet, compound, slurry, etc. Takes various forms: surface grinding (creates flat and/or squared surfaces); cylindrical grinding (for external cylindrical and tapered shapes, fillets, undercuts, etc.); centerless grinding; chamfering; thread and form grinding; tool and cutter grinding; offhand grinding; lapping and polishing (grinding with extremely fine grits to create ultrasmooth surfaces); honing; and disc grinding.
- high-speed steels ( HSS)
high-speed steels ( HSS)
Available in two major types: tungsten high-speed steels (designated by letter T having tungsten as the principal alloying element) and molybdenum high-speed steels (designated by letter M having molybdenum as the principal alloying element). The type T high-speed steels containing cobalt have higher wear resistance and greater red (hot) hardness, withstanding cutting temperature up to 1,100º F (590º C). The type T steels are used to fabricate metalcutting tools (milling cutters, drills, reamers and taps), woodworking tools, various types of punches and dies, ball and roller bearings. The type M steels are used for cutting tools and various types of dies.
- micron
micron
Measure of length that is equal to one-millionth of a meter.
- turning
turning
Workpiece is held in a chuck, mounted on a face plate or secured between centers and rotated while a cutting tool, normally a single-point tool, is fed into it along its periphery or across its end or face. Takes the form of straight turning (cutting along the periphery of the workpiece); taper turning (creating a taper); step turning (turning different-size diameters on the same work); chamfering (beveling an edge or shoulder); facing (cutting on an end); turning threads (usually external but can be internal); roughing (high-volume metal removal); and finishing (final light cuts). Performed on lathes, turning centers, chucking machines, automatic screw machines and similar machines.