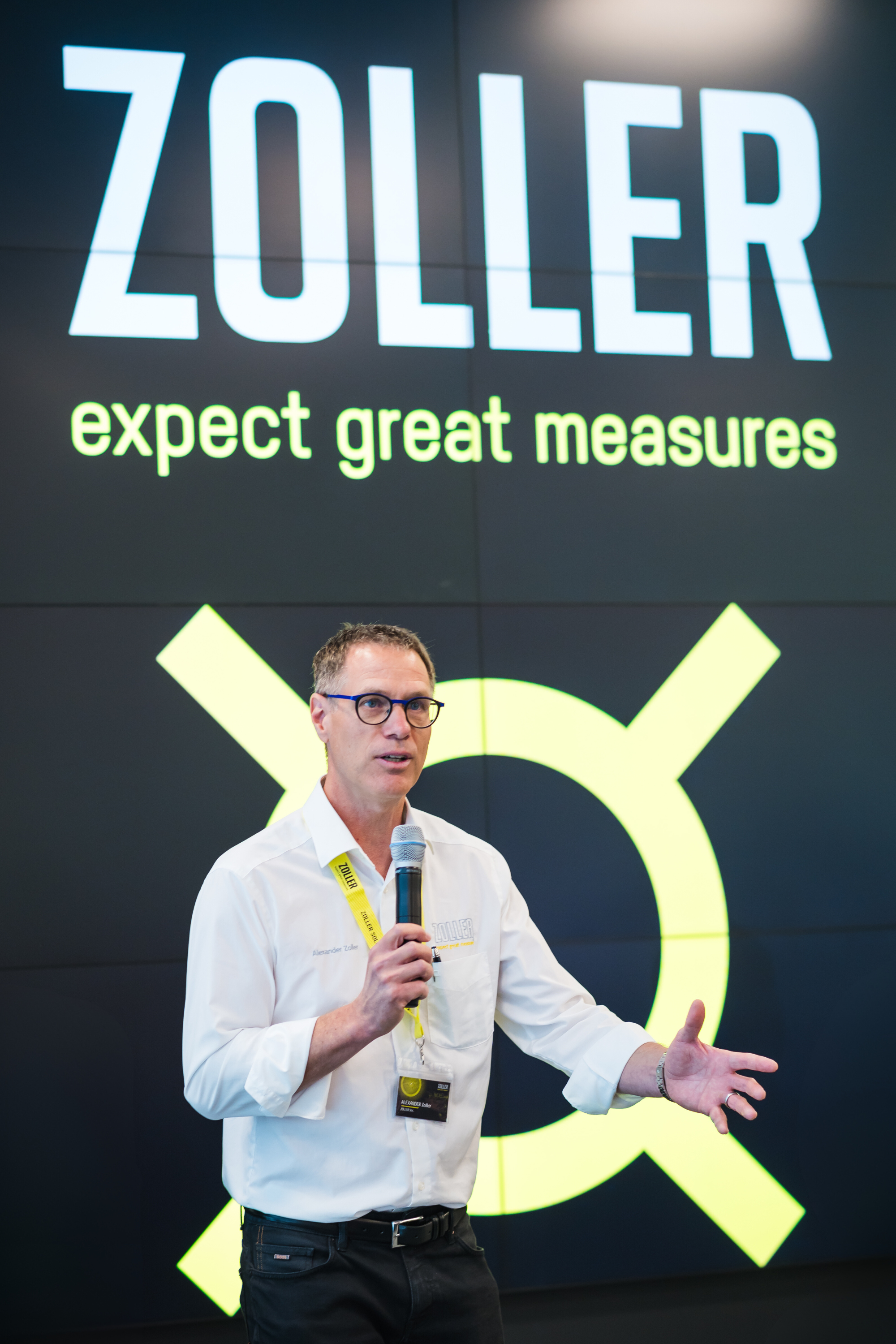
“Why do we do what we do?” asked Alexander Zoller, president of ZOLLER Inc., during his welcome and keynote address on the first day of the two-day ZOLLER Open House & Technology Days, which took place June 12-13 at the company’s headquarters in Ann Arbor, Michigan. He answered, “It’s in our blood.”
That deep-rooted passion to thrive in today’s competitive and digitized manufacturing environment was on display and demonstrated by the German-based manufacturer of tool presetting, measuring, management, inspection, automation, heat-shrink and balancing equipment.
With a theme of “Integrate. Success.,” Zoller kicked off the event by emphasizing that ZOLLER’s goal is to provide technology to increase shop efficiency and production at customers’ facilities and internally. One offering that he said is a “gamechanger” is the »idChip.« On request, the company provides all toolholders with an integrated chip and DataMatrix code to allow end users to clearly identify a toolholder at all times, with a comprehensive overview of all its information.
The day’s agenda continued with a presentation by Dietmar Moll, director of sales at ZOLLER, titled “The connected machine shop: A vision for how machining and Industry 4.0 meet.” He noted that the CAM department is where everything starts and defines the shop floor efficiency in a connected machine shop, with everything networked into a central database. With cutting tools being one of the few variables left in parts manufacturing, the challenge of having the right tools at the right location must be overcome and the machine tool must be notified when tool life expires using the right technology.
Automation is needed to make manufacturing more efficient, Moll said, and ZOLLER offers various solutions. For example, the new »coraMeasure LG« automated tool measurement system, which will be premiered at IMTS 2024, delivers tools assembled in a pallet system to a linear robot that loads the tools into a »venturion« presetting and measuring machine to save time, prevent errors and reduce the human workload. Other automation systems include »coraLogistic« to eliminate the need for manual tool transport, »loadBox« to provide the required tool deliveries from the central tool storage automatically and »roboBox« to automate processes like tool assembly, measurement, setting and heat shrinking.
Turning to customer applications, Daniel Skwierczynski, director of operations at ERA Industries Inc. in Elk Grove Village, Illinois, discussed how partnering with ZOLLER improved production efficiency. He explained that the contract manufacturer’s production equipment is connected through the ZOLLER TMS Tool Management Solutions to enhance organization and standardization and eliminate human error. ERA Industries built a tool library with TMS for use by its programmers, with every detail spelled out in a data sheet. The manufacturer’s next step for TMS, he noted, is to integrate purchasing and inventory.
Tom Bassett II, owner of ProCAM Services LLC in Zeeland, Michigan, continued with a presentation about how tool presetting transformed his machine shop. When he initially encountered the »smile 420« presetter at a ZOLLER trade show exhibit, Bassett dismissed it as something only suitable for production machining and not for a job shop. However, after doing some calculations in his head about how much time is spent setting up and touching off tools for each job, he quickly changed his mind about how helpful the presetter would be in reducing lead times without sacrificing part quality. During the first two years of presetter use, ProCAM increased sales by $1 million. “This is the perfect thing for us.”
Cedric Hasenfratz, ZOLLER’s North America sales and partnership manager for TMS, and Felix Kanbach, national service manager, teamed up to provide an overview of the CAM to part experience. They demonstrated, with Hasenfratz covering the art and Kanbach covering the part, how the company’s system of solutions works together for smart, efficient manufacturing.
Hasenfratz continued with a presentation about how part manufacturers can leverage the features of TMS to drive digitization and gain full control over their cutting tools.
Video presentations concluded the morning agenda, with one showing how the Athens, Alabama, production facility of Intech, a manufacturer of medical devices and equipment, used TMS to better organize and manage cutting tools and related tooling on the shop floor. (See the Productive Times in the December 2023 issue.)
A second video showed how a presetter and TMS can even be beneficial at a school. Located in Nashville, Indiana, Brown County High School is not only the home of the Eagles athletic teams but also the student-run Eagles Manufacturing business. The job shop has a »smile 420« presetter and TMS to help train future workers while they already sell machining services.
After a lunch that featured German cuisine, Michael Stepke, training manager at ZOLLER, led a panel that addressed the skills gap with the need to engage the future workforce through mentoring, apprenticeships and corporate partnerships. Ryan Rowe, career and technical education director and career education planning districts administrator for the Washtenaw Intermediate School District in Ann Arbor, said schools that once were removing shop classes are now implementing them as demand for those skills has become more prominent. Learning those skills should start earlier in a student’s career, even as early as elementary school. “The pendulum has swung back.”
Kyrsten Rue, director of the Washtenaw Community College Center for Career Success in Ann Arbor, noted that because the industry needs a talent pipeline, the college collaborates with employers on crafting apprenticeship programs and saturating students with work experience while educating them. “We must all be at the table together.”
The first day concluded with various technical talks in breakout sessions and live demonstrations, followed by a barbecue buffet.
Contact Details
Related Glossary Terms
- arbor
arbor
Shaft used for rotary support in machining applications. In grinding, the spindle for mounting the wheel; in milling and other cutting operations, the shaft for mounting the cutter.
- computer-aided manufacturing ( CAM)
computer-aided manufacturing ( CAM)
Use of computers to control machining and manufacturing processes.
- payload ( workload)
payload ( workload)
Maximum load that the robot can handle safely.
- toolholder
toolholder
Secures a cutting tool during a machining operation. Basic types include block, cartridge, chuck, collet, fixed, modular, quick-change and rotating.
- turning
turning
Workpiece is held in a chuck, mounted on a face plate or secured between centers and rotated while a cutting tool, normally a single-point tool, is fed into it along its periphery or across its end or face. Takes the form of straight turning (cutting along the periphery of the workpiece); taper turning (creating a taper); step turning (turning different-size diameters on the same work); chamfering (beveling an edge or shoulder); facing (cutting on an end); turning threads (usually external but can be internal); roughing (high-volume metal removal); and finishing (final light cuts). Performed on lathes, turning centers, chucking machines, automatic screw machines and similar machines.