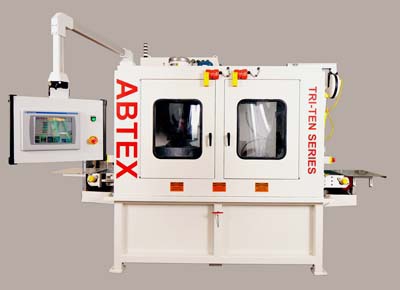
Abtex Corp. has expanded its Tri-Ten series of deburring systems to include a model that is designed to accept precision ground parts, in carriers, directly from a grinding, lapping or honing machine.
All Tri-Ten machines are customized for Abtex application-specific abrasive filament brushes. The first system (pictured) was sold to a major manufacturer of lapping and honing equipment. It will be used to demonstrate the higher productivity and time saving advantages of deburring multiple parts in carriers. Parts, in carriers, will be automatically conveyed from the lapping machine into the Tri-Ten deburring system.
As the magnetized belt grips the parts in their carrier, they are presented to the planetary head, where three 10-inch abrasive filament disc brushes deburr the upward facing surface. Edge break, surface finish and material removal are accurately controlled. In this system, the parts are then rinsed as they pass under a coolant shower, and then dried by an air knife before traveling over a demagnetizer.
In the application for which the pictured machine was built, the parts, still in their carrier, are removed, flipped manually, and sent through the system again to deburr the opposite side of the parts. A system that deburrs both sides of the parts in a single pass is also available from Abtex.
Abtex brushes may be specified with silicon carbide, aluminum oxide, ceramic or diamond filaments. All are mounted in the company's proprietary, molded, composite material.
Contact Details
Related Glossary Terms
- abrasive
abrasive
Substance used for grinding, honing, lapping, superfinishing and polishing. Examples include garnet, emery, corundum, silicon carbide, cubic boron nitride and diamond in various grit sizes.
- aluminum oxide
aluminum oxide
Aluminum oxide, also known as corundum, is used in grinding wheels. The chemical formula is Al2O3. Aluminum oxide is the base for ceramics, which are used in cutting tools for high-speed machining with light chip removal. Aluminum oxide is widely used as coating material applied to carbide substrates by chemical vapor deposition. Coated carbide inserts with Al2O3 layers withstand high cutting speeds, as well as abrasive and crater wear.
- coolant
coolant
Fluid that reduces temperature buildup at the tool/workpiece interface during machining. Normally takes the form of a liquid such as soluble or chemical mixtures (semisynthetic, synthetic) but can be pressurized air or other gas. Because of water’s ability to absorb great quantities of heat, it is widely used as a coolant and vehicle for various cutting compounds, with the water-to-compound ratio varying with the machining task. See cutting fluid; semisynthetic cutting fluid; soluble-oil cutting fluid; synthetic cutting fluid.
- grinding
grinding
Machining operation in which material is removed from the workpiece by a powered abrasive wheel, stone, belt, paste, sheet, compound, slurry, etc. Takes various forms: surface grinding (creates flat and/or squared surfaces); cylindrical grinding (for external cylindrical and tapered shapes, fillets, undercuts, etc.); centerless grinding; chamfering; thread and form grinding; tool and cutter grinding; offhand grinding; lapping and polishing (grinding with extremely fine grits to create ultrasmooth surfaces); honing; and disc grinding.
- lapping
lapping
Finishing operation in which a loose, fine-grain abrasive in a liquid medium abrades material. Extremely accurate process that corrects minor shape imperfections, refines surface finishes and produces a close fit between mating surfaces.