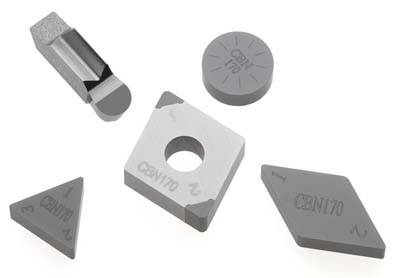
Seco Tools has announced the availability of its new CBN 170 grade, a PCBN grade developed for the finish turning of nickel-based super alloys commonly found in aerospace, power generation and automotive components. Designed for both toughness and wear-resistance, CBN 170 works well in materials such as Inconel 718, UDIMET, Waspaloy, MAR M and others.
In field tests run using CBN 170, it has increased tool life by 40 percent and cutting speed by 45 percent as compared to whisker ceramics. Designed to satisfy the exacting surface finish, tolerance and length of cut requirements typically found in finishing operations for nickel-based super alloys, CBN 170 incorporates a unique whisker ceramic binder, which enhances tool life and reduces insert indexes. These whiskers of silicon carbide crystals add tensile strength and fracture toughness to the grade.
The new grade can be applied to finish machining of hardened and unhardened nickel-based superalloys from cast, forged, powdered metal or machined from solid source. It can achieve depths of cut up to 0.020" at cutting speeds of 900 to 1300 sfm. Designed for continuous cutting applications, coolant must be applied to the operation.
To further enhance tool life, Seco recommends the use of its Jetstream tooling, which delivers coolant at high pressures close to the cutting edge, cooling the work area and producing smaller, hard, brittle chips.
Contact Details
Related Glossary Terms
- alloys
alloys
Substances having metallic properties and being composed of two or more chemical elements of which at least one is a metal.
- ceramics
ceramics
Cutting tool materials based on aluminum oxide and silicon nitride. Ceramic tools can withstand higher cutting speeds than cemented carbide tools when machining hardened steels, cast irons and high-temperature alloys.
- coolant
coolant
Fluid that reduces temperature buildup at the tool/workpiece interface during machining. Normally takes the form of a liquid such as soluble or chemical mixtures (semisynthetic, synthetic) but can be pressurized air or other gas. Because of water’s ability to absorb great quantities of heat, it is widely used as a coolant and vehicle for various cutting compounds, with the water-to-compound ratio varying with the machining task. See cutting fluid; semisynthetic cutting fluid; soluble-oil cutting fluid; synthetic cutting fluid.
- cubic boron nitride ( CBN)
cubic boron nitride ( CBN)
Crystal manufactured from boron nitride under high pressure and temperature. Used to cut hard-to-machine ferrous and nickel-base materials up to 70 HRC. Second hardest material after diamond. See superabrasive tools.
- cutting speed
cutting speed
Tangential velocity on the surface of the tool or workpiece at the cutting interface. The formula for cutting speed (sfm) is tool diameter 5 0.26 5 spindle speed (rpm). The formula for feed per tooth (fpt) is table feed (ipm)/number of flutes/spindle speed (rpm). The formula for spindle speed (rpm) is cutting speed (sfm) 5 3.82/tool diameter. The formula for table feed (ipm) is feed per tooth (ftp) 5 number of tool flutes 5 spindle speed (rpm).
- fracture toughness
fracture toughness
Critical value (KIC) of stress intensity. A material property.
- polycrystalline cubic boron nitride ( PCBN)
polycrystalline cubic boron nitride ( PCBN)
Cutting tool material consisting of polycrystalline cubic boron nitride with a metallic or ceramic binder. PCBN is available either as a tip brazed to a carbide insert carrier or as a solid insert. Primarily used for cutting hardened ferrous alloys.
- superalloys
superalloys
Tough, difficult-to-machine alloys; includes Hastelloy, Inconel and Monel. Many are nickel-base metals.
- tensile strength
tensile strength
In tensile testing, the ratio of maximum load to original cross-sectional area. Also called ultimate strength. Compare with yield strength.
- tolerance
tolerance
Minimum and maximum amount a workpiece dimension is allowed to vary from a set standard and still be acceptable.
- turning
turning
Workpiece is held in a chuck, mounted on a face plate or secured between centers and rotated while a cutting tool, normally a single-point tool, is fed into it along its periphery or across its end or face. Takes the form of straight turning (cutting along the periphery of the workpiece); taper turning (creating a taper); step turning (turning different-size diameters on the same work); chamfering (beveling an edge or shoulder); facing (cutting on an end); turning threads (usually external but can be internal); roughing (high-volume metal removal); and finishing (final light cuts). Performed on lathes, turning centers, chucking machines, automatic screw machines and similar machines.