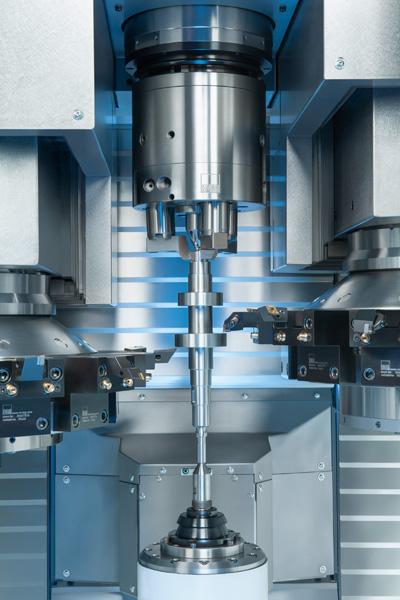
According to a recent study by Roland-Berger, the automotive supplier industry will grow at a rate of approximately 6 percent in the next two years with competition intensifying. To gain an advantage, manufacturers must take a close look at the profitability of production sites. Component production must become faster, deliver high precision and show a greater degree of economic viability. EMAG's production solution is the VT 4-4 vertical lathe that delivers top efficiency levels in large-volume gearbox production.
For a number of reasons, the production of drive and gear shafts represents a very specific key task in the manufacture of automobiles. For one, many of their components are of a very detailed and highly complex geometry, on which so much depends. For instance, high-precision gearings ensure a highly effective torque transmission within the gearbox. Having high-precision shoulders and grooves allows for the safe connectivity of components. The efficiency of the powertrain as a whole depends to a large degree on the functionality of their shafts. These highly complex components are produced in batches of millions and on completion of the central turning work the shaft should ideally display a geometry that is as close to its final contour as possible. Tolerance production planners look for the micrometre range of the shaft.
To reconcile these high-performance requirements the turning specialists at EMAG have developed the 4-axis VT 4-4 vertical shaft turning machine. It opens up new potential in the machining of components with a maximum length of 41 inches and a maximum diameter of 8 inches with the following advantages:
• Simultaneous: Machining is carried out in 4 axes at a maximum speed of 4,500 rpm. The process employs two turrets with twelve tool stations each, equipped with turning tools or driven tools, with one station reserved for the gripper.
• Automated: Workpiece grippers move the raw-parts to the machining area and remove the finished components, i.e. one gripper inserts a new raw-part into the machine while the other gripper removes the finished component from it.
"This principle offers a great step up in performance in the production of shafts, especially in an environment that deals with large component volumes," explains Dr. Guido Hegener, Managing Director of EMAG Maschinenfabrik GmbH. "Due to the fast workpiece changeovers and powerful machining with four axes, cycle times are very short. Together with the integrated automation system, the process ensures that unit costs are kept to a minimum."
In its standard model, the machine is equipped with two space-saving, recirculating conveyors that accommodate up to 28 raw-parts and 28 finished components respectively. Transfer and turnover units or robots ensure that a number of VT machines can be linked up both cost-effectively and with great ease. Of particular importance to the development engineers at EMAG is the quality of the components produced. For this purpose, the machine base is made of the polymer concrete MINERALIT. It carries all technology modules: the powerful workspindle, turrets and the tailstock. Its rigid, vibration resistant construction guarantees an equally vibration resistant turning process which ensures high-quality surfaces and highly accurate geometries. EMAG's typical vertical alignment of the workpiece also guarantees constant process integrity, as the unhindered chip flow it offers prevents the accumulation of chips in the machining area.
"Last, but by no means least, we have also attached great importance to the ease of operation of these machines," emphasises Hegener. "After all, the human factor is a very important one when it comes to productivity. We want to make it as simple as possible for the operator."
To achieve this, all relevant components, from electrics to hydraulics, including the cooling system, are very easy to access with the user interface being of an intuitive, clearly laid out design. The VT 4-4 opens up a wide range of possibilities for the production planner in gearbox manufacturing. Use of the machine is made even more economical by its compact design, with the vertical alignment taking up very little space. There is also no necessity for additional automation, as this is already an integrated part of the machine. Short cycle times, a high degree of flexibility and a small footprint summarize EMAG's new Modular Standard machine concept.
Hegener concludes, "With a very attractive price-performance ratio, the VT4-4 ingeniously complements our vertical shaft turning program. It is the reason why we believe our chances in the marketplace are excellent."
Contact Details
Related Glossary Terms
- lathe
lathe
Turning machine capable of sawing, milling, grinding, gear-cutting, drilling, reaming, boring, threading, facing, chamfering, grooving, knurling, spinning, parting, necking, taper-cutting, and cam- and eccentric-cutting, as well as step- and straight-turning. Comes in a variety of forms, ranging from manual to semiautomatic to fully automatic, with major types being engine lathes, turning and contouring lathes, turret lathes and numerical-control lathes. The engine lathe consists of a headstock and spindle, tailstock, bed, carriage (complete with apron) and cross slides. Features include gear- (speed) and feed-selector levers, toolpost, compound rest, lead screw and reversing lead screw, threading dial and rapid-traverse lever. Special lathe types include through-the-spindle, camshaft and crankshaft, brake drum and rotor, spinning and gun-barrel machines. Toolroom and bench lathes are used for precision work; the former for tool-and-die work and similar tasks, the latter for small workpieces (instruments, watches), normally without a power feed. Models are typically designated according to their “swing,” or the largest-diameter workpiece that can be rotated; bed length, or the distance between centers; and horsepower generated. See turning machine.
- tolerance
tolerance
Minimum and maximum amount a workpiece dimension is allowed to vary from a set standard and still be acceptable.
- turning
turning
Workpiece is held in a chuck, mounted on a face plate or secured between centers and rotated while a cutting tool, normally a single-point tool, is fed into it along its periphery or across its end or face. Takes the form of straight turning (cutting along the periphery of the workpiece); taper turning (creating a taper); step turning (turning different-size diameters on the same work); chamfering (beveling an edge or shoulder); facing (cutting on an end); turning threads (usually external but can be internal); roughing (high-volume metal removal); and finishing (final light cuts). Performed on lathes, turning centers, chucking machines, automatic screw machines and similar machines.
- turning machine
turning machine
Any machine that rotates a workpiece while feeding a cutting tool into it. See lathe.