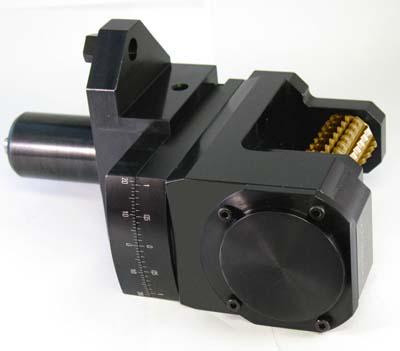
A special compact gear hobber system from EXSYS Tool Inc. allows shops to generate splines, spur or helical gears in one operation. The EXSYS/EPPINGER adjustable tool holding system, designed for Mazak horizontal turning centers, as well as most other machine brands, eliminates having to rough gears on one machine, then transfer them to another for gear hobbing.
To compensate for different types of grooves or pitches in splines and gears, users simply set the vernier dial up to +/- 20 degrees. Software for gear hobbing is an option on most turning centers.
Having a compact design, the system, in most instances, operates without interrupting its neighboring tool stations in a machine turret. Other comparable systems often require the room of two tool positions. Built for heavy machining loads, the gear-driven EXSYS/EPPINGER gear hobbing system has been designed for 45 Nm of torque and speeds of up to 3,000 rpm for hobs or slotting saws up to 2.480 dia (63mm). Arbor diameters are available for all standard sizes for use of both slotting saws and gear hobs. Changing tools takes just seconds by removing the yoke plate and sliding out the arbor. The base of the tool holder remains in its station.
Contact Details
Related Glossary Terms
- arbor
arbor
Shaft used for rotary support in machining applications. In grinding, the spindle for mounting the wheel; in milling and other cutting operations, the shaft for mounting the cutter.
- centers
centers
Cone-shaped pins that support a workpiece by one or two ends during machining. The centers fit into holes drilled in the workpiece ends. Centers that turn with the workpiece are called “live” centers; those that do not are called “dead” centers.
- slotting
slotting
Machining, normally milling, that creates slots, grooves and similar recesses in workpieces, including T-slots and dovetails.
- turning
turning
Workpiece is held in a chuck, mounted on a face plate or secured between centers and rotated while a cutting tool, normally a single-point tool, is fed into it along its periphery or across its end or face. Takes the form of straight turning (cutting along the periphery of the workpiece); taper turning (creating a taper); step turning (turning different-size diameters on the same work); chamfering (beveling an edge or shoulder); facing (cutting on an end); turning threads (usually external but can be internal); roughing (high-volume metal removal); and finishing (final light cuts). Performed on lathes, turning centers, chucking machines, automatic screw machines and similar machines.