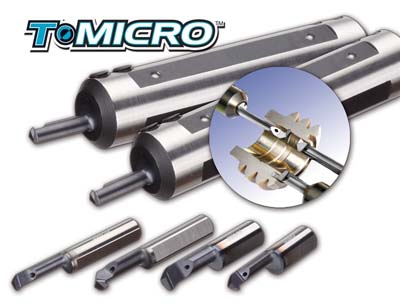
Ingersoll Cutting Tools introduces the T-Micro system specifically designed for the machining of very small internal diameters. The T-Micro system is a 2-piece design, consisting of a sleeve and replaceable carbide inserts. Applications include grooving, profiling, chamfering, face grooving/deep face grooving, threading, and back turning starting at .024" (.6mm). The inserts feature coolant thru capabilities and are available in grade TT9030, a submicron substrate with PVD-TiAlN coating, making them the perfect solution for all miniature internal applications.
Inside the new T-Micro sleeve design is a locating pin to ensure repeatability when indexing the inserts. This allows operators to return to machining without resetting the tool. The locating pin also allows operators to replace inserts without removing the sleeve from the tool post. The T-Micro sleeve also features an angular clamping design to avoid interference when replacing the insert allowing simplified tool change on Swiss-type and other multi-spindle lathes. Ingersoll offers this sleeve in many shank sizes .500", .625", .750", and 1.00" also 12mm, 14mm, 16mm, 20mm, 22mm, and 25mm to accommodate all machines.
Contact Details
Related Glossary Terms
- chamfering
chamfering
Machining a bevel on a workpiece or tool; improves a tool’s entrance into the cut.
- coolant
coolant
Fluid that reduces temperature buildup at the tool/workpiece interface during machining. Normally takes the form of a liquid such as soluble or chemical mixtures (semisynthetic, synthetic) but can be pressurized air or other gas. Because of water’s ability to absorb great quantities of heat, it is widely used as a coolant and vehicle for various cutting compounds, with the water-to-compound ratio varying with the machining task. See cutting fluid; semisynthetic cutting fluid; soluble-oil cutting fluid; synthetic cutting fluid.
- grooving
grooving
Machining grooves and shallow channels. Example: grooving ball-bearing raceways. Typically performed by tools that are capable of light cuts at high feed rates. Imparts high-quality finish.
- profiling
profiling
Machining vertical edges of workpieces having irregular contours; normally performed with an endmill in a vertical spindle on a milling machine or with a profiler, following a pattern. See mill, milling machine.
- shank
shank
Main body of a tool; the portion of a drill or similar end-held tool that fits into a collet, chuck or similar mounting device.
- threading
threading
Process of both external (e.g., thread milling) and internal (e.g., tapping, thread milling) cutting, turning and rolling of threads into particular material. Standardized specifications are available to determine the desired results of the threading process. Numerous thread-series designations are written for specific applications. Threading often is performed on a lathe. Specifications such as thread height are critical in determining the strength of the threads. The material used is taken into consideration in determining the expected results of any particular application for that threaded piece. In external threading, a calculated depth is required as well as a particular angle to the cut. To perform internal threading, the exact diameter to bore the hole is critical before threading. The threads are distinguished from one another by the amount of tolerance and/or allowance that is specified. See turning.
- turning
turning
Workpiece is held in a chuck, mounted on a face plate or secured between centers and rotated while a cutting tool, normally a single-point tool, is fed into it along its periphery or across its end or face. Takes the form of straight turning (cutting along the periphery of the workpiece); taper turning (creating a taper); step turning (turning different-size diameters on the same work); chamfering (beveling an edge or shoulder); facing (cutting on an end); turning threads (usually external but can be internal); roughing (high-volume metal removal); and finishing (final light cuts). Performed on lathes, turning centers, chucking machines, automatic screw machines and similar machines.