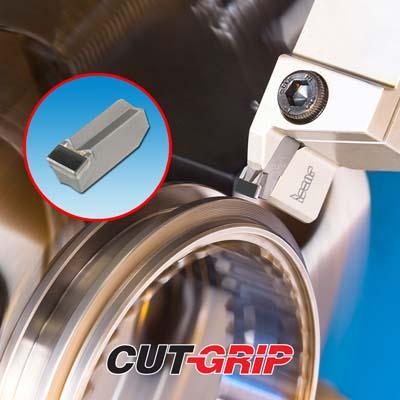
ISCAR has fine-tuned its workhorse GROOVE TURN cubic boron nitride (CBN) formulation to materially improve rough and finish grooving on hard ferrous materials under a wider range of conditions. They have created new CBN grade IB10H, which is harder than the mainstay grade IB50; and grade IB20H which is stronger and tougher.
In a continuous-cut external groove-turn on punishing 4340 steel hardened to 58-61 HRc, the GROOVE TURN IB10H tool lasted through 20 parts vs.7 for IB50 and produced a fine surface finish. In an interrupted cut in the identical material, an IB20H tool delivered 500 parts per edge vs. 350. Of note is that the failure mode with the new inserts was gradual edge wear, not sudden cracking or rupture.
Grade IB10H, with 53 percent fine-grain CBN content, features the identical edge preparation as its predecessor IB50. By contrast, the honed edge on the IB20H is slightly larger and at a sharper angle, to withstand less ideal cutting conditions. Its substrate content is 63 percent fine- and medium-grain CBN. Both new grades come in two styles that target hard ferrous materials: GROOVE TURN GITM for turning and grooving, and GROOVE TURN GITM (full radius) for profiling and grooving. In a profiling test in 1045 tool steel hardened to 60 HRc, the GITM (full radius) tool outlasted its IB50 counterpart 200 parts to 80.
Contact Details
Related Glossary Terms
- cubic boron nitride ( CBN)
cubic boron nitride ( CBN)
Crystal manufactured from boron nitride under high pressure and temperature. Used to cut hard-to-machine ferrous and nickel-base materials up to 70 HRC. Second hardest material after diamond. See superabrasive tools.
- cubic boron nitride ( CBN)2
cubic boron nitride ( CBN)
Crystal manufactured from boron nitride under high pressure and temperature. Used to cut hard-to-machine ferrous and nickel-base materials up to 70 HRC. Second hardest material after diamond. See superabrasive tools.
- edge preparation
edge preparation
Conditioning of the cutting edge, such as a honing or chamfering, to make it stronger and less susceptible to chipping. A chamfer is a bevel on the tool’s cutting edge; the angle is measured from the cutting face downward and generally varies from 25° to 45°. Honing is the process of rounding or blunting the cutting edge with abrasives, either manually or mechanically.
- grooving
grooving
Machining grooves and shallow channels. Example: grooving ball-bearing raceways. Typically performed by tools that are capable of light cuts at high feed rates. Imparts high-quality finish.
- interrupted cut
interrupted cut
Cutting tool repeatedly enters and exits the work. Subjects tool to shock loading, making tool toughness, impact strength and flexibility vital. Closely associated with milling operations. See shock loading.
- profiling
profiling
Machining vertical edges of workpieces having irregular contours; normally performed with an endmill in a vertical spindle on a milling machine or with a profiler, following a pattern. See mill, milling machine.
- turning
turning
Workpiece is held in a chuck, mounted on a face plate or secured between centers and rotated while a cutting tool, normally a single-point tool, is fed into it along its periphery or across its end or face. Takes the form of straight turning (cutting along the periphery of the workpiece); taper turning (creating a taper); step turning (turning different-size diameters on the same work); chamfering (beveling an edge or shoulder); facing (cutting on an end); turning threads (usually external but can be internal); roughing (high-volume metal removal); and finishing (final light cuts). Performed on lathes, turning centers, chucking machines, automatic screw machines and similar machines.