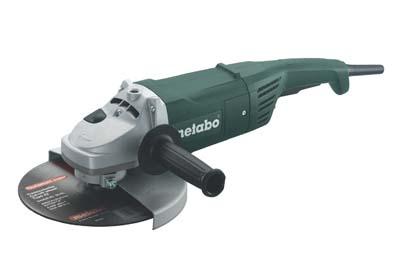
Metabo Corp. introduces the W2000 9" angle grinder. This new large angle grinder, featuring the same quality and performance as other Metabo tools, is lighter and more economical than other grinders in its class, the company claims.
deal for cutting, grinding and sanding applications, the W2000 is equipped with a 9" wheel guard, delivers 115 inch-lbs of torque and a no-load speed of 6,600 rpm. This large angle grinder is one of the most efficient on the market, featuring a long-lasting 15 A motor with 2,000 watts of power.
The W2000 features an advanced ergonomic design with a three-position side handle that allows users to turn the tool 90 degrees to cut vertically, while still having a firm grasp on the grinder. The tool includes a simplified on/off switch configuration with a safety lock to prevent the tool from accidentally turning on, as well as a burst-proof guard and spindle lock. Auto-stop carbon brushes help to increase the tool's service life.
The W2000 9" angle grinder is covered by Metabo's XXL warranty. This free warranty extends the normal one year power tool warranty to three years. Optional equipment for the W2000 includes a variety of Metabo abrasives, adapter kits to mount Type 1 and Type 27 non-hubbed wheels, a Type 1 cut-off wheel guard and a carrying case.
Contact Details
Related Glossary Terms
- grinding
grinding
Machining operation in which material is removed from the workpiece by a powered abrasive wheel, stone, belt, paste, sheet, compound, slurry, etc. Takes various forms: surface grinding (creates flat and/or squared surfaces); cylindrical grinding (for external cylindrical and tapered shapes, fillets, undercuts, etc.); centerless grinding; chamfering; thread and form grinding; tool and cutter grinding; offhand grinding; lapping and polishing (grinding with extremely fine grits to create ultrasmooth surfaces); honing; and disc grinding.
- turning
turning
Workpiece is held in a chuck, mounted on a face plate or secured between centers and rotated while a cutting tool, normally a single-point tool, is fed into it along its periphery or across its end or face. Takes the form of straight turning (cutting along the periphery of the workpiece); taper turning (creating a taper); step turning (turning different-size diameters on the same work); chamfering (beveling an edge or shoulder); facing (cutting on an end); turning threads (usually external but can be internal); roughing (high-volume metal removal); and finishing (final light cuts). Performed on lathes, turning centers, chucking machines, automatic screw machines and similar machines.