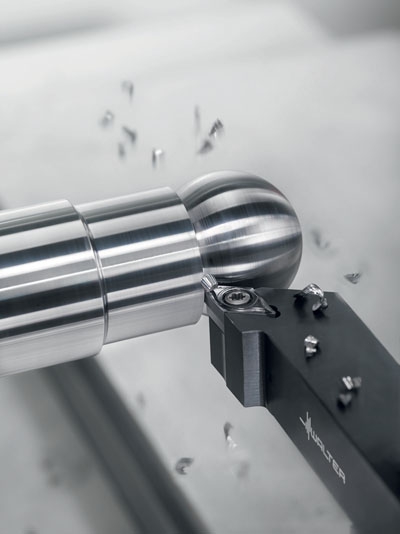
Walter has introduced a trio of universal, positive insert geometries that reduce downtime and boost performance in steel, stainless and iron machining (ISO material types P, M, and K).
The new Tiger-tec Silver MP4,mm4 and MK4 are light cutting and universal positive geometries in both 7° and 11° positive rake angles along with precision-ground and precision-sintered cutting edges. The chip forming geometry features a 12° rake angle for excellent shearing action when cutting stainless or low-carbon steel, along with an additional 18° chip groove in the corner radius area for excellent chip control in light finishing cuts. The D- and V- style inserts also have a curved main cutting edge for reduced cutting forces and clearance in profiling operations.
Typical applications for the new geometries include boring operations of all types, profile turning, turning or boring of thin wall or unstable workpieces; internal machining with long overhangs; and on Swiss type machines or multi-spindle machines. The new Tiger-tec Silver MP4,mm4, and MK4 geometries are available in grades WPP10S, WPP20S, WMP20S, WKK10S, WKK20S.
Field tests have shown that these new geometries provide longer tool life, better chip control, greater reliability and performance increases of up to 75 percent thanks to their Tiger-tec Silver coating.
Contact Details
Related Glossary Terms
- boring
boring
Enlarging a hole that already has been drilled or cored. Generally, it is an operation of truing the previously drilled hole with a single-point, lathe-type tool. Boring is essentially internal turning, in that usually a single-point cutting tool forms the internal shape. Some tools are available with two cutting edges to balance cutting forces.
- clearance
clearance
Space provided behind a tool’s land or relief to prevent rubbing and subsequent premature deterioration of the tool. See land; relief.
- profiling
profiling
Machining vertical edges of workpieces having irregular contours; normally performed with an endmill in a vertical spindle on a milling machine or with a profiler, following a pattern. See mill, milling machine.
- rake
rake
Angle of inclination between the face of the cutting tool and the workpiece. If the face of the tool lies in a plane through the axis of the workpiece, the tool is said to have a neutral, or zero, rake. If the inclination of the tool face makes the cutting edge more acute than when the rake angle is zero, the rake is positive. If the inclination of the tool face makes the cutting edge less acute or more blunt than when the rake angle is zero, the rake is negative.
- turning
turning
Workpiece is held in a chuck, mounted on a face plate or secured between centers and rotated while a cutting tool, normally a single-point tool, is fed into it along its periphery or across its end or face. Takes the form of straight turning (cutting along the periphery of the workpiece); taper turning (creating a taper); step turning (turning different-size diameters on the same work); chamfering (beveling an edge or shoulder); facing (cutting on an end); turning threads (usually external but can be internal); roughing (high-volume metal removal); and finishing (final light cuts). Performed on lathes, turning centers, chucking machines, automatic screw machines and similar machines.