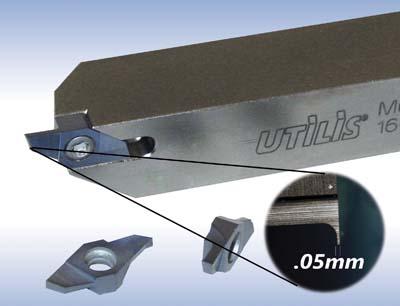
April 2011- Genevieve Swiss Industries has introduced UTILIS Multidec 1600 series thin grooving and micro turning tools capable of work under .125" in diameter utilizing insert widths from thickness of human hair (.0019") up to .108" with cutting edge repeatability within .0004". Ideal for high precision machining of 316 L stainless steel and 6AL4V titanium in orthopedic, medical tools and dental implants, the 1600 series is ground from premium carbide grades for enhanced tool life and is available with a variety of coatings.
The small holder shanks (down to 7mm) are designed to suit the smallest Swiss machines. Tool holders for larger machines are also available. Additionally these Swiss-type turning tools offer geometries that can be used for front turn, back turn, micro threading and cut-off work. "Full radius" grooving and turning tools are offered in standard increments as well. When combined with special ID working holders, the 1600 system handles axial (face) grooving and ID work on larger parts.
Contact Details
Related Glossary Terms
- grooving
grooving
Machining grooves and shallow channels. Example: grooving ball-bearing raceways. Typically performed by tools that are capable of light cuts at high feed rates. Imparts high-quality finish.
- inner diameter ( ID)
inner diameter ( ID)
Dimension that defines the inside diameter of a cavity or hole. See OD, outer diameter.
- precision machining ( precision measurement)
precision machining ( precision measurement)
Machining and measuring to exacting standards. Four basic considerations are: dimensions, or geometrical characteristics such as lengths, angles and diameters of which the sizes are numerically specified; limits, or the maximum and minimum sizes permissible for a specified dimension; tolerances, or the total permissible variations in size; and allowances, or the prescribed differences in dimensions between mating parts.
- threading
threading
Process of both external (e.g., thread milling) and internal (e.g., tapping, thread milling) cutting, turning and rolling of threads into particular material. Standardized specifications are available to determine the desired results of the threading process. Numerous thread-series designations are written for specific applications. Threading often is performed on a lathe. Specifications such as thread height are critical in determining the strength of the threads. The material used is taken into consideration in determining the expected results of any particular application for that threaded piece. In external threading, a calculated depth is required as well as a particular angle to the cut. To perform internal threading, the exact diameter to bore the hole is critical before threading. The threads are distinguished from one another by the amount of tolerance and/or allowance that is specified. See turning.
- turning
turning
Workpiece is held in a chuck, mounted on a face plate or secured between centers and rotated while a cutting tool, normally a single-point tool, is fed into it along its periphery or across its end or face. Takes the form of straight turning (cutting along the periphery of the workpiece); taper turning (creating a taper); step turning (turning different-size diameters on the same work); chamfering (beveling an edge or shoulder); facing (cutting on an end); turning threads (usually external but can be internal); roughing (high-volume metal removal); and finishing (final light cuts). Performed on lathes, turning centers, chucking machines, automatic screw machines and similar machines.