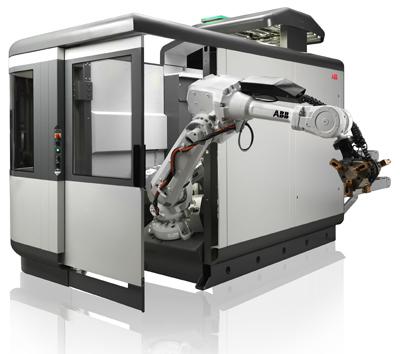
ABB Robotics has introduced the FlexMT, a flexible, pre-engineered system designed to load and unload machine tools using vision guided robotics. Designed for both small batch and high volume production, the FlexMT increases spindle utilization by up to 60 percent over manual machine tending. The system can handle most any size and type of part, and is compatible with a wide range of machine tools, including horizontal and vertical lathes, machining centers, 5-axis machines and grinders.
The FlexMT comes equipped with a choice between a two- or three-finger gripper, and both an infeed and outfeed conveyor. With six standard plug-and-play options, including two separate deburring tools, a re-grip table, a needle marking unit, a turn station, and an air cleaning box, the modular system is capable of handling a variety of additional manufacturing operations.
Available in two variants: the FlexMT 20, which features an ABB IRB 2600 robot, with a 20kg payload and a 1.65m reach; and the FlexMT 60, which features an ABB IRB 4600 robot, with a 60kg payload and a 2.05m reach. The turnkey automation system comes complete with a robot controller inside its fully integrated control cabinet, providing easy and precise control of the robot, vision, conveyors and machine tool.
"ABB puts a lot of effort into creating solutions which are truly innovative and address the real needs of our customers," says Frank-Peter Kirgis, global business line manager for ABB. "With the FlexMT we've hit many of our customers leading concerns. The solution is easy, fast and flexible to set up and program; all things our customers demand. The FlexMT can also give small and medium size companies a higher degree of automation. By facilitating a steady and predictable machine tool utilization of up to 90 percent, the FlexMT increases the approximate 50 percent spindle utilization of manual machine tending by as much as 60 percent. This provides a sustainable competitive advantage and a ROI in many cases of less than a year."
Additional system benefits include:
• Reduced operational cost and complexity: The vision guidance component reduces operational cost and complexity by allowing the FlexMT to recognize variations in part size and geometrical shape, and enabling it to pick and place parts that are presented on the conveyor in differing positions. The FlexMT can be used with existing machine tools and can run free from operator supervision for up to eight hours.
• Easy system set-up and programming: Control and communications with the robot are tightly integrated into the software, providing a very simple and intuitive set-up and teach-in. With one of the easiest to use operator interfaces on the market, teaching of a new part is possible in less than 10 minutes.
• Improved health and safety: The self-contained nature of the FlexMT improves working conditions by drastically reducing workplace injury related to heavy lifting, exposure to hazardous conditions including the presence of coolants, sharp edges, burrs, tooling and other dangers.
Related Glossary Terms
- centers
centers
Cone-shaped pins that support a workpiece by one or two ends during machining. The centers fit into holes drilled in the workpiece ends. Centers that turn with the workpiece are called “live” centers; those that do not are called “dead” centers.
- payload ( workload)
payload ( workload)
Maximum load that the robot can handle safely.
- robotics
robotics
Discipline involving self-actuating and self-operating devices. Robots frequently imitate human capabilities, including the ability to manipulate physical objects while evaluating and reacting appropriately to various stimuli. See industrial robot; robot.