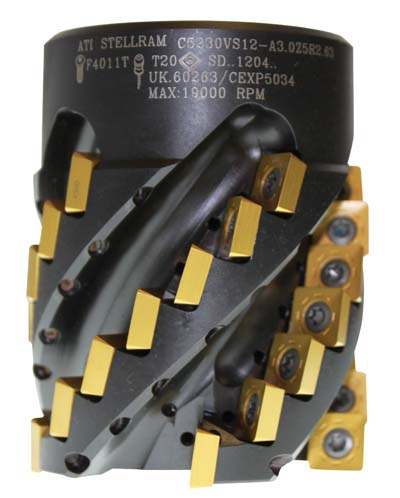
ATI Stellram introduces a new chevron-style milling cutter, the Stellram 5230VS12, designed specifically for machining titanium and other difficult to machine materials, such as nickel-based alloys ands cobalt-based alloys. In comparison studies, the Stellram 5230VS12 cutter achieved metal removal rates up to two times greater than comparable cutters on the market. This is vital in aerospace applications where part design often calls for up to 80 percent metal removal.
The 5230VS12 chevron cutter positions multiple inserts along the cutting edge of each helical flute. This advanced design of the insert placement provides smooth, progressive penetration and cutting action for extended tool life, lower power consumption and up to a 30 percent improvement in surface finish. Cutters range from 2.5 inches to 4.0 inches in diameter, with four to six flutes. Depending on flute length, from 6 to 14 inserts can be positioned along each flute.
Individual coolant jets to each insert provide constant chip evacuation and temperature stability in the cutting zone.
Two insert grades are available for the Stellram 5230VS12: Grade X500 is a member of ATI Stellram's high performance premium X-Grade Technology family of carbide inserts designed for the toughest applications in Nickel-based alloys, Cobalt-based alloys, Titanium and Titanium-based alloys. Grade SP6519 offers the combination of a tough substrate with the latest generation of TiAlN super nano coating. This versatile grade is equally suited for both High Temperature Alloys and Stainless Steels.
The Stellram 5230VS12 cutter represents a combination of advanced tool design and high technology insert grades, resulting in a tool capable of substantially increased productivity and surface finish quality.
Contact Details
Related Glossary Terms
- alloys
alloys
Substances having metallic properties and being composed of two or more chemical elements of which at least one is a metal.
- coolant
coolant
Fluid that reduces temperature buildup at the tool/workpiece interface during machining. Normally takes the form of a liquid such as soluble or chemical mixtures (semisynthetic, synthetic) but can be pressurized air or other gas. Because of water’s ability to absorb great quantities of heat, it is widely used as a coolant and vehicle for various cutting compounds, with the water-to-compound ratio varying with the machining task. See cutting fluid; semisynthetic cutting fluid; soluble-oil cutting fluid; synthetic cutting fluid.
- flutes
flutes
Grooves and spaces in the body of a tool that permit chip removal from, and cutting-fluid application to, the point of cut.
- gang cutting ( milling)
gang cutting ( milling)
Machining with several cutters mounted on a single arbor, generally for simultaneous cutting.
- milling
milling
Machining operation in which metal or other material is removed by applying power to a rotating cutter. In vertical milling, the cutting tool is mounted vertically on the spindle. In horizontal milling, the cutting tool is mounted horizontally, either directly on the spindle or on an arbor. Horizontal milling is further broken down into conventional milling, where the cutter rotates opposite the direction of feed, or “up” into the workpiece; and climb milling, where the cutter rotates in the direction of feed, or “down” into the workpiece. Milling operations include plane or surface milling, endmilling, facemilling, angle milling, form milling and profiling.
- milling cutter
milling cutter
Loosely, any milling tool. Horizontal cutters take the form of plain milling cutters, plain spiral-tooth cutters, helical cutters, side-milling cutters, staggered-tooth side-milling cutters, facemilling cutters, angular cutters, double-angle cutters, convex and concave form-milling cutters, straddle-sprocket cutters, spur-gear cutters, corner-rounding cutters and slitting saws. Vertical cutters use shank-mounted cutting tools, including endmills, T-slot cutters, Woodruff keyseat cutters and dovetail cutters; these may also be used on horizontal mills. See milling.
- stainless steels
stainless steels
Stainless steels possess high strength, heat resistance, excellent workability and erosion resistance. Four general classes have been developed to cover a range of mechanical and physical properties for particular applications. The four classes are: the austenitic types of the chromium-nickel-manganese 200 series and the chromium-nickel 300 series; the martensitic types of the chromium, hardenable 400 series; the chromium, nonhardenable 400-series ferritic types; and the precipitation-hardening type of chromium-nickel alloys with additional elements that are hardenable by solution treating and aging.
- titanium aluminum nitride ( TiAlN)
titanium aluminum nitride ( TiAlN)
Often used as a tool coating. AlTiN indicates the aluminum content is greater than the titanium. See coated tools.