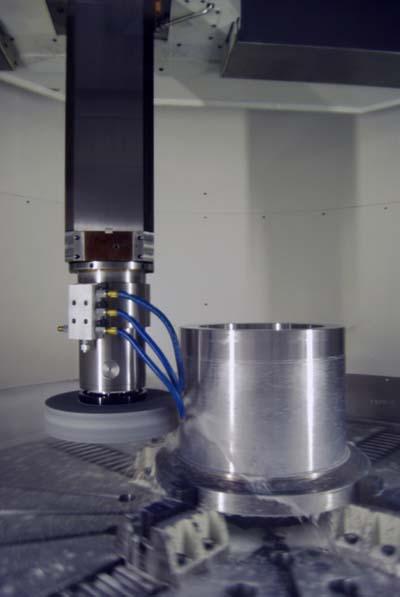
A new automatically changed grinding attachment adds surface finishing to the one-stop processing capabilities of MAG's vertical turning centers, allowing finishing of ID, OD and plane surfaces on parts up to 4700mm (185 inches) diameter. The system is ideal for large bearings and gearboxes used in machinery for the mining, construction, marine and energy industries. VTC's equipped with the new 22/33 kW (29.5/44 hp) grinding attachment can produce better than 10 micro inch finishes and roundness of less than 60 micro inch, with diameter size control of 0.025mm (0.001 inches).
The grinding attachment can utilize wheel sizes up to 400mm (15.75 inches) and produces 400 Nm (295 ft lb) torque and a maximum speed of 3000 rpm. Equipped for grinding work, VTC's are enhanced with a modified coolant and filtration system, hand-held wash wand, stainless steel bowl enclosure with extra side flush, covers over the column ways, and a heavy duty chip conveyor to handle grinding swarf. Full X-axis travel on MAG VTC's provides room for a highly rigid dressing tool outside the work zone, allowing the machine to accept its maximum part size without restriction.
Normally stored in an off-line tool drawer, the grinding attachment joins live spindles, right-angle heads, horizontal adapters and other attachments that can be changed automatically on the VTC's for maximum machine uptime and single-setup part completion. One of the most versatile turning systems for large parts, MAG's VTC's in table size 1000mm to 4500mm (39.4 to 177 inches) can already perform standard and hard turning, as well as live-spindle machining, contouring and part probing operations on multiple sides and the full diameter of a part. Ideal for grinding applications, these machines are FEA-designed for maximum strength-to-weight ratio, stiffness and rigidity, with heavily ribbed cast iron or robust steel weldments used for major components, such as base, column and cross slide, depending on the machine size.
The adjustable cross slide, with MAG's unique leveling technique and patented rail clamping system, allows ram extension to be minimized during grinding for maximum system stiffness. A Wedge Lock tooling system with hydraulic clamping force of 150,000 N (33,000 lb) allows use of tools up to 700mm (27.5 inches) long. The 250mm-square (10 inches) hydrostatic ram resists torsion and vibration to produce superior surface finishes, and allows downward feed thrust up to 34,000 N (7,600 lb). Cross rail leveling with dual linear scales ensures parallelism between table and rail, with leveling accuracy of 10µm (0.0004 inches). Preloaded roller guideways enhance system stiffness and reduce friction for excellent contouring accuracy.
Tables are extensively supported with a combination of tapered roller and flat thrust bearings to handle constant use at maximum load ratings. The table design resists tipping with unbalanced loads, and superior accuracy is ensured with factory-specified maximum 0.005mm (0.0002 inches) table runout. Table drives are rated 84 kW (112 hp) to 108 kW (145 hp), and capable of producing maximum torque of 17,113 Nm (12,623 ft lb) to 111,116 Nm (81,955 ft lb). Full contouring with the table C-axis enables drilling, tapping or mill turning of features anywhere on the workpiece with contouring/positioning by 360,000-position table.
A standard 26-position tool changer accommodates six Wedge Lock and 20 modular tools. Various options for the VTC line include expanded tool capacity, part and tool probing systems, pallet changer and fourth axis. Fanuc 310i or Siemens 480D controls are standard.
Contact Details
Related Glossary Terms
- centers
centers
Cone-shaped pins that support a workpiece by one or two ends during machining. The centers fit into holes drilled in the workpiece ends. Centers that turn with the workpiece are called “live” centers; those that do not are called “dead” centers.
- coolant
coolant
Fluid that reduces temperature buildup at the tool/workpiece interface during machining. Normally takes the form of a liquid such as soluble or chemical mixtures (semisynthetic, synthetic) but can be pressurized air or other gas. Because of water’s ability to absorb great quantities of heat, it is widely used as a coolant and vehicle for various cutting compounds, with the water-to-compound ratio varying with the machining task. See cutting fluid; semisynthetic cutting fluid; soluble-oil cutting fluid; synthetic cutting fluid.
- dressing
dressing
Removal of undesirable materials from “loaded” grinding wheels using a single- or multi-point diamond or other tool. The process also exposes unused, sharp abrasive points. See loading; truing.
- feed
feed
Rate of change of position of the tool as a whole, relative to the workpiece while cutting.
- flat ( screw flat)
flat ( screw flat)
Flat surface machined into the shank of a cutting tool for enhanced holding of the tool.
- grinding
grinding
Machining operation in which material is removed from the workpiece by a powered abrasive wheel, stone, belt, paste, sheet, compound, slurry, etc. Takes various forms: surface grinding (creates flat and/or squared surfaces); cylindrical grinding (for external cylindrical and tapered shapes, fillets, undercuts, etc.); centerless grinding; chamfering; thread and form grinding; tool and cutter grinding; offhand grinding; lapping and polishing (grinding with extremely fine grits to create ultrasmooth surfaces); honing; and disc grinding.
- hard turning
hard turning
Single-point cutting of a workpiece that has a hardness value higher than 45 HRC.
- inner diameter ( ID)
inner diameter ( ID)
Dimension that defines the inside diameter of a cavity or hole. See OD, outer diameter.
- milling machine ( mill)
milling machine ( mill)
Runs endmills and arbor-mounted milling cutters. Features include a head with a spindle that drives the cutters; a column, knee and table that provide motion in the three Cartesian axes; and a base that supports the components and houses the cutting-fluid pump and reservoir. The work is mounted on the table and fed into the rotating cutter or endmill to accomplish the milling steps; vertical milling machines also feed endmills into the work by means of a spindle-mounted quill. Models range from small manual machines to big bed-type and duplex mills. All take one of three basic forms: vertical, horizontal or convertible horizontal/vertical. Vertical machines may be knee-type (the table is mounted on a knee that can be elevated) or bed-type (the table is securely supported and only moves horizontally). In general, horizontal machines are bigger and more powerful, while vertical machines are lighter but more versatile and easier to set up and operate.
- outer diameter ( OD)
outer diameter ( OD)
Dimension that defines the exterior diameter of a cylindrical or round part. See ID, inner diameter.
- stiffness
stiffness
1. Ability of a material or part to resist elastic deflection. 2. The rate of stress with respect to strain; the greater the stress required to produce a given strain, the stiffer the material is said to be. See dynamic stiffness; static stiffness.
- swarf
swarf
Metal fines and grinding wheel particles generated during grinding.
- tapping
tapping
Machining operation in which a tap, with teeth on its periphery, cuts internal threads in a predrilled hole having a smaller diameter than the tap diameter. Threads are formed by a combined rotary and axial-relative motion between tap and workpiece. See tap.
- turning
turning
Workpiece is held in a chuck, mounted on a face plate or secured between centers and rotated while a cutting tool, normally a single-point tool, is fed into it along its periphery or across its end or face. Takes the form of straight turning (cutting along the periphery of the workpiece); taper turning (creating a taper); step turning (turning different-size diameters on the same work); chamfering (beveling an edge or shoulder); facing (cutting on an end); turning threads (usually external but can be internal); roughing (high-volume metal removal); and finishing (final light cuts). Performed on lathes, turning centers, chucking machines, automatic screw machines and similar machines.