END USER: Royal Master Grinders Inc., (201) 337-8500, www.royalmaster.com.
CHALLENGE: Provide centerless grinding machines that can produce parts with continually tightening size and surface finish requirements.
SOLUTION: Customized coolant filtration equipment.
SOLUTION PROVIDER: Losma Inc., (973) 300-1044, www.losma.com.
Of all the reasons to filter coolant, cost reduction usually tops the list. That’s because filtration extends the working life of coolant, so part manufacturers buy less and reduce disposal costs. For centerless grinding operations, however, coolant filtration plays an even more important role. “The cleanliness of the coolant affects part quality,” said John Memmelaar Sr., president of Royal Master Grinders Inc.
The Oakland, N.J., machine builder offers the Bedrock series of centerless grinders, which have a granite-topped machine base and routinely produce parts at customer locations with dimensional tolerances measured in the millionths of an inch and surface finishes as fine as 4µin. Ra.
Coolant cleanliness impacts part quality in two ways when tolerances and finish requirements are this tight. For one, clean coolant maintains a more uniform viscosity over time, which contributes to the grinding wheel’s ability to cut consistently by eliminating variations in the amount of heat the part is exposed to.
Second, clean coolant helps impart fine surface finishes. If there are particles in the coolant, they can migrate to the wheel and, eventually, turn up on the part surface, so having clean coolant helps avoid this. “If you have a 1µm particle in the coolant, you will get a 1µm scratch on the part,” Memmelaar said.
Therefore, grinding machines frequently require a coolant filtration system that removes particles finer than can be achieved with standard three-stage, settling-type tank filtration systems, according to Memmelaar. Royal Master Grinders turned to nearby Losma Inc. to supply coolant filtration systems for many of its machines.
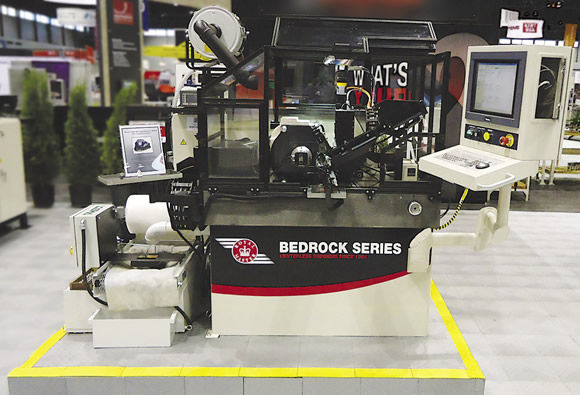
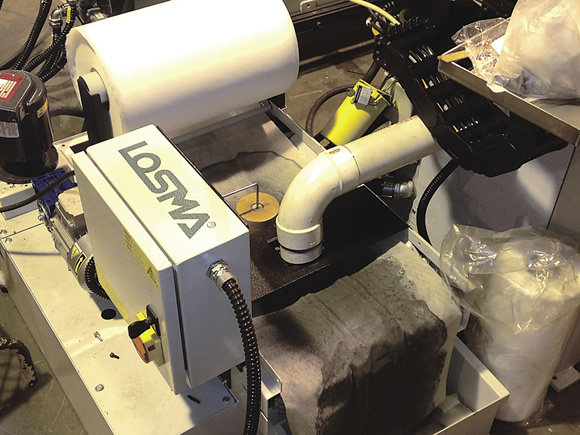
For Royal Master Grinders’ Bedrock series of centerless grinders, Losma customized coolant filtration equipment to match tank capacity to the machine.
“The Bedrock series, for example, uses one of our custom-designed filters capable of filtering mineral oil at 4 gpm,” said Ken Angie, strategic business manager for liquid filtration for the Sparta, N.J., company. “The Royal Master Grinders’ Bedrock series units come equipped with our DTE 30 filter beds, but we increased the tank capacity from 25 to 40 gallons so we could match the coolant volume of the grinder.”
Memmelaar noted the Losma coolant filtration systems are effective for the Bedrock series, in part, because they remove relatively large stock amounts, such as 0.001 " of material. As a side benefit, the large-capacity tank helps keep coolant temperature low, which helps extend grinding machine life and contributes, in a small way, to its accuracy. Ideally, coolant temperature should be kept as close to room temperature as possible, which might require a coolant chiller, according to Memmelaar.
In addition to the increased tank capacity, Royal Master Grinders’ coolant filtration equipment from Losma includes additional custom features. For example, a special mounting plate allows the machine builder to use its own high-pressure pump with the filter. The 2,500-psi pump forces coolant between the workpiece/wheel interface to increase wheel life, Memmelaar noted. He added that the pump can also be integrated as a pressurized wheel cleaner to blast away dirt and debris impregnated in the wheel bond.
The coolant filtration system also has custom-designed casters that allow the filter bed to fit partially under the grinding machines, saving space and providing flexibility when performing service.
Memmelaar pointed out that a high level of coolant filtration, with some applications requiring the removal of particles down to 1µm, is particularly critical when grinding nonmetals, such as plastic medical parts. “It’s desirable in the medical products fields to have parts that are absolutely clean,” he said.
Quality considerations aside, coolant filtration generates significant cost savings. Memmelaar noted an effective filtration system reduces the need for wheel dressing because there are fewer particles to cause wheel loading and allows part manufacturers to purchase less coolant. “You want the coolant to last a long time, but far bigger savings come from reducing disposal costs,” he said. “It costs a couple of dollars a gallon to dispose of used coolant, which is more than the price of new coolant.” CTE
Related Glossary Terms
- centerless grinding
centerless grinding
Grinding operation in which the workpiece rests on a knife-edge support, rotates through contact with a regulating or feed wheel and is ground by a grinding wheel. This method allows grinding long, thin parts without steady rests; also lessens taper problems. Opposite of cylindrical grinding. See cylindrical grinding; grinding.
- coolant
coolant
Fluid that reduces temperature buildup at the tool/workpiece interface during machining. Normally takes the form of a liquid such as soluble or chemical mixtures (semisynthetic, synthetic) but can be pressurized air or other gas. Because of water’s ability to absorb great quantities of heat, it is widely used as a coolant and vehicle for various cutting compounds, with the water-to-compound ratio varying with the machining task. See cutting fluid; semisynthetic cutting fluid; soluble-oil cutting fluid; synthetic cutting fluid.
- dressing
dressing
Removal of undesirable materials from “loaded” grinding wheels using a single- or multi-point diamond or other tool. The process also exposes unused, sharp abrasive points. See loading; truing.
- grinding
grinding
Machining operation in which material is removed from the workpiece by a powered abrasive wheel, stone, belt, paste, sheet, compound, slurry, etc. Takes various forms: surface grinding (creates flat and/or squared surfaces); cylindrical grinding (for external cylindrical and tapered shapes, fillets, undercuts, etc.); centerless grinding; chamfering; thread and form grinding; tool and cutter grinding; offhand grinding; lapping and polishing (grinding with extremely fine grits to create ultrasmooth surfaces); honing; and disc grinding.
- grinding machine
grinding machine
Powers a grinding wheel or other abrasive tool for the purpose of removing metal and finishing workpieces to close tolerances. Provides smooth, square, parallel and accurate workpiece surfaces. When ultrasmooth surfaces and finishes on the order of microns are required, lapping and honing machines (precision grinders that run abrasives with extremely fine, uniform grits) are used. In its “finishing” role, the grinder is perhaps the most widely used machine tool. Various styles are available: bench and pedestal grinders for sharpening lathe bits and drills; surface grinders for producing square, parallel, smooth and accurate parts; cylindrical and centerless grinders; center-hole grinders; form grinders; facemill and endmill grinders; gear-cutting grinders; jig grinders; abrasive belt (backstand, swing-frame, belt-roll) grinders; tool and cutter grinders for sharpening and resharpening cutting tools; carbide grinders; hand-held die grinders; and abrasive cutoff saws.