END USER: InovaTools (Eckerle & Ertel GmbH), 011-49-8467-8400-0, www.inovatools.eu, InovaTools USA LLC, (810) 444-8745.
CHALLENGE: Achieve tight-tolerance requirements when producing microtools.
SOLUTION: Grinding machines designed to produce microtools.
SOLUTION PROVIDER: Rollomatic SA, 011-41-32-752-17-00, www.rollomaticsa.com; Rollomatic Inc., (866) 713-6398, www.rollomaticusa.com.
Manufacturers of microscale cutting tools require a high level of precision from their grinding machines. They also need a great deal of trust in a grinding machine builder when purchasing its equipment to produce tool features that often require a microscope to see.
InovaTools (Eckerle & Ertel GmbH), based in Kinding-Haunstetten, Germany, makes cutting tools from 0.05mm to 6.0mm in diameter with tolerances as tight as 0.005mm for diameters and 0.003mm for radii. The products include step mills and other milling tools, profilers and step drills and other holemaking tools.
“Those tools cannot be ground on just any machine,” said Georg Eckerle, the company’s managing director. “It must be possible to produce the tools quickly and cost-effectively. Otherwise, a medium-size company such as ours cannot survive in the marketplace.”
The toolmaker found a solution in grinding machines from Rollomatic SA, Le Landeron, Switzerland. Eckerle’s initial contact in 2002 with the grinding machine builder was Dieter Furtwengler, head of sales in Germany. “Mr. Furtwengler introduced us to the GrindSmart 620XS tool grinder, but warned straight away that the machine’s precision can only be incorporated into the tool with correspondingly precise, cylindrically ground carbide rods,” Eckerle said. “After a few tests with standard carbide rods, we discovered he was correct.”
To grind the rods, InovaTools uses ShapeSmart P4, NP4 and NP5 cylindrical grinding machines from Rollomatic. In addition to its four cylindrical grinders, the toolmaker has one Nano6 and eight 620/628XS tool grinders.
Machine design is based on what is crucial in microtool production, according to Rollomatic. And Rollomatic should know because it started in the early 1950s as a manufacturer of micro-tools. “I worked in tool production myself in the 1980s,” said company CEO Michel Rollier. “Even back then, we used to manufacture our own machines. That is why I understand how a machine must be designed for it to be popular with tool manufacturers.”
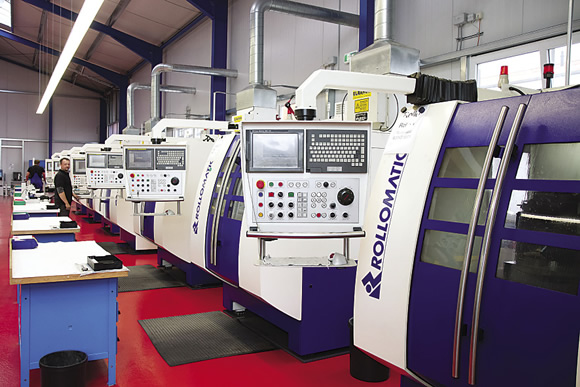
InovaTools produces cutting tools from 0.05mm to 6.0mm in diameter on GrindSmart 620/628XS and Nano6 grinding machines from Rollomatic.
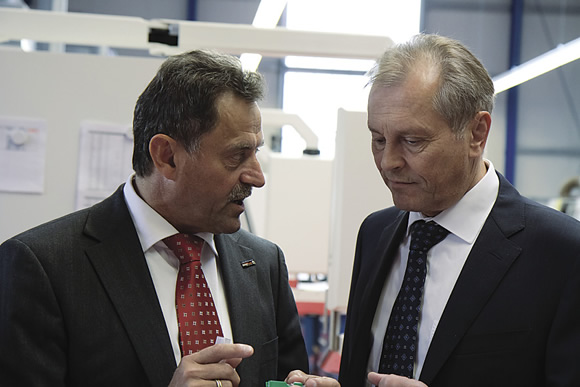
InovaTools Managing Director Georg Eckerle (left) converses with Rollomatic CEO Michel Rollier.
For example, the grinders are compact because long travel distances increase cycle time and develop considerably more heat than short travel distances. The X-axis travel for the Nano6 is 5.75 " and the X-axis travel for the 620XS is 12 ", which do not represent the actual tool lengths or flute lengths the machines are capable of grinding. The small footprint also reduces the requirements for expensive shop floor space.
Also, three of the six axes on the Nano6 grinder are hydrostatic to optimize damping, an absolute necessity when producing the smallest tools, according to Rollomatic. Another absolute necessity is a repetitive size accuracy of less than 0.003mm (0.00001 "), the company added.
Eckerle noted the grinding machines operate 7 days a week, including unattended operation when lots of up to 300 tools are produced. During weekend operation, an operator is only on-site twice a day to load the machines and measure the tools.
Rollomatic holds 1- or 2-week training courses for operating the machines on-site and at its factory in Le Landeron. “The finer points are explained in follow-up training courses on-site under production conditions,” Furtwengler said.
InovaTools recently launched Project Future, a restructuring of its production operations to meet the heavy demand for high-performance tools, including microtools. “We are very flexible and, with the aid of the Rollomatic control, are able to produce almost everything required on the market,” Eckerle said.
Depending on market conditions, Eckerle indicated InovaTools plans to purchase two to three Rollomatic grinding machines each year.
Related Glossary Terms
- cylindrical grinding
cylindrical grinding
Grinding operation in which the workpiece is rotated around a fixed axis while the grinding wheel is fed into the outside surface in controlled relation to the axis of rotation. The workpiece is usually cylindrical, but it may be tapered or curvilinear in profile. See centerless grinding; grinding.
- gang cutting ( milling)
gang cutting ( milling)
Machining with several cutters mounted on a single arbor, generally for simultaneous cutting.
- grinding
grinding
Machining operation in which material is removed from the workpiece by a powered abrasive wheel, stone, belt, paste, sheet, compound, slurry, etc. Takes various forms: surface grinding (creates flat and/or squared surfaces); cylindrical grinding (for external cylindrical and tapered shapes, fillets, undercuts, etc.); centerless grinding; chamfering; thread and form grinding; tool and cutter grinding; offhand grinding; lapping and polishing (grinding with extremely fine grits to create ultrasmooth surfaces); honing; and disc grinding.
- grinding machine
grinding machine
Powers a grinding wheel or other abrasive tool for the purpose of removing metal and finishing workpieces to close tolerances. Provides smooth, square, parallel and accurate workpiece surfaces. When ultrasmooth surfaces and finishes on the order of microns are required, lapping and honing machines (precision grinders that run abrasives with extremely fine, uniform grits) are used. In its “finishing” role, the grinder is perhaps the most widely used machine tool. Various styles are available: bench and pedestal grinders for sharpening lathe bits and drills; surface grinders for producing square, parallel, smooth and accurate parts; cylindrical and centerless grinders; center-hole grinders; form grinders; facemill and endmill grinders; gear-cutting grinders; jig grinders; abrasive belt (backstand, swing-frame, belt-roll) grinders; tool and cutter grinders for sharpening and resharpening cutting tools; carbide grinders; hand-held die grinders; and abrasive cutoff saws.
- milling
milling
Machining operation in which metal or other material is removed by applying power to a rotating cutter. In vertical milling, the cutting tool is mounted vertically on the spindle. In horizontal milling, the cutting tool is mounted horizontally, either directly on the spindle or on an arbor. Horizontal milling is further broken down into conventional milling, where the cutter rotates opposite the direction of feed, or “up” into the workpiece; and climb milling, where the cutter rotates in the direction of feed, or “down” into the workpiece. Milling operations include plane or surface milling, endmilling, facemilling, angle milling, form milling and profiling.