END USER: Hitachi Metals Automotive Components USA LLC, (570) 724-5191, www.hmacusa.com.
CHALLENGE: Reduce insert costs and simplify insert reordering and stocking.
SOLUTION: Consolidate the number of ISO-standard inserts applied.
SOLUTION PROVIDERS: DCT Industrial Supply Co., (217) 423-3639, www.dctisc.com; Tungaloy America Inc., (888) 554-8394, www.tungaloyamerica.com.
Regardless of the business climate, part manufacturers continually seek to lower costs and Hitachi Metals Automotive Components USA LLC is no exception. Management at its Wellsboro, Pa., manufacturing plant requires quarterly cost reductions and that includes tooling, noted Todd Heggenstaller, manufacturing engineer for HMAC, which machines mostly ductile cast iron parts for automotive OEMs. (The company also has a plant in Effingham, Ill., as well as a casting foundry in Lawrenceville, Pa.)
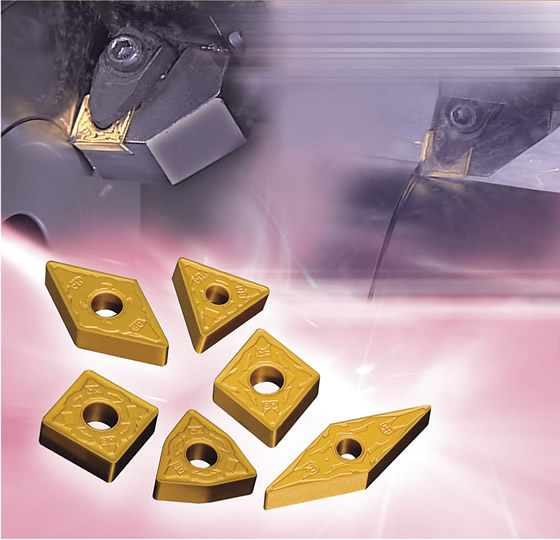
When consolidating its ISO-standards inserts, HMAC incorporated numerous inserts from Tungaloy, including T5100-grade inserts for machining ductile cast iron.
To reduce costs, Mike Moran, vice president of tooling integrator DCT Industrial Supply Co., Decatur, Ill., recommended HMAC consolidate its ISO-standard inserts. Heggenstaller explained that consolidation lowers the price per insert by allowing the company to buy larger quantities of each type of ISO-standard insert from one toolmaker rather than smaller quantities from multiple suppliers. The Wellsboro plant has a dozen production lines, managed by three manufacturing engineers. Numerous lines used the same type of insert but from different sources. For example, five lines applied SCMT inserts from four toolmakers.
In addition to saving money, insert consolidation streamlines the purchasing, inventory and distribution process. Inserts are dispensed from two DCT-owned AutoCrib vending machines. “It simplifies everything for team members in the toolroom and for the people on the shop floor,” said Jason McMullen, tooling coordinator for HMAC, noting Aaron Jacobus, account manager for DCT, is on-site 5 days a week to stock and maintain the vending machines.
To begin the consolidation effort, HMAC requested insert prices from current and potential suppliers based on usage. Heggenstaller noted HMAC tested the lowest-cost insert first but it needed to perform adequately before the company would purchase it.
Although HMAC previously hadn’t purchased inserts from Tungaloy America Inc., Arlington Heights, Ill., the toolmaker’s inserts that suit HMAC’s applications typically cost about 30 to 50 percent less than the competition. “Tungaloy won just about all those inserts on price,” Heggenstaller said, “and on all of the lines except one, they performed equal to or better than the inserts they replaced.”
In one application, for instance, a Tungaloy TNGG insert not only lasted 50 percent longer than the previous insert, completing 300 pieces instead of 200, it could also run at a 28 percent higher feed rate, increasing to 0.32 mm/rev. from 0.25 mm/rev., Heggenstaller noted. “There’s always a push to lower cycle time,” he said.
He explained that HMAC tested inserts in machines that have spindles equipped with microchips to monitor the tools while they cut. After cutting parts, Heggenstaller examined the tools with a digital microscope. “If the insert made the tool life requirement and still looked really good, we would increase its tool life, thus lowering our cost even more,” he said. “If it looked average, we would keep tool life at what we had.”
The examinations also enable troubleshooting. “If I see [the problem is] just heavy flank wear, we go with a harder grade,” Heggenstaller said. “If I see cratering, we go with a different coating. With edge deformation, we know we’re running it too fast.”
Sometimes, the tested grade met all the requirements except for the performance of its chipbreaker. An insert needs a “robust” chipbreaker to effectively cut ductile cast iron, according to Heggenstaller, as well as a slightly positive or neutral rake angle. In early tests, some Tungaloy inserts generated “weird” chips, so HMAC tested ones with different chipbreakers and achieved better results, he added.
HMAC found, for example, that Tungaloy’s CM chipbreaker on the T5115 grade is effective for semifinish boring. The chipbreaker has a relief surface that extends optimally close to the end of the cutting edge while avoiding direct impact from chips and suppresses vibration when cutting, according to the toolmaker.
Although HMAC operates three shifts at least 6 days and frequently 7 days a week, the company continues to test tools, even after completing the vast majority of the consolidation project in February. “It’s all about squeezing money out of the part,” Heggenstaller said. “I’ll test anybody’s anything if it can lower my cost.”
He added that Al Anelli, regional sales engineer for Tungaloy, continues to take advantage of that opportunity. “Al is still moving in and trying to replace some other companies and, based on past success, he’ll probably do that,” Heggenstaller said, noting about 15 percent of HMAC’s inserts are from Tungaloy. “Their inserts are priced very aggressively and they work.”
Related Glossary Terms
- boring
boring
Enlarging a hole that already has been drilled or cored. Generally, it is an operation of truing the previously drilled hole with a single-point, lathe-type tool. Boring is essentially internal turning, in that usually a single-point cutting tool forms the internal shape. Some tools are available with two cutting edges to balance cutting forces.
- chipbreaker
chipbreaker
Groove or other tool geometry that breaks chips into small fragments as they come off the workpiece. Designed to prevent chips from becoming so long that they are difficult to control, catch in turning parts and cause safety problems.
- cratering
cratering
Depressions formed on the face of a cutting tool caused by heat, pressure and the motion of chips moving across the tool’s surface.
- feed
feed
Rate of change of position of the tool as a whole, relative to the workpiece while cutting.
- flank wear
flank wear
Reduction in clearance on the tool’s flank caused by contact with the workpiece. Ultimately causes tool failure.
- rake
rake
Angle of inclination between the face of the cutting tool and the workpiece. If the face of the tool lies in a plane through the axis of the workpiece, the tool is said to have a neutral, or zero, rake. If the inclination of the tool face makes the cutting edge more acute than when the rake angle is zero, the rake is positive. If the inclination of the tool face makes the cutting edge less acute or more blunt than when the rake angle is zero, the rake is negative.
- relief
relief
Space provided behind the cutting edges to prevent rubbing. Sometimes called primary relief. Secondary relief provides additional space behind primary relief. Relief on end teeth is axial relief; relief on side teeth is peripheral relief.