END USER: A German parts manufacturer.
CHALLENGE: Eliminate applying two countersink tools and a tap to complete a machining operation.
SOLUTION: A combination tool that countersinks and thread mills.
SOLUTION PROVIDERS: Johs. Boss GmbH & Co. KG, + 49-7432-9087-0, www.johs-boss.de; J.M. Sales USA, (248) 321-6170, www.jmsales-usa.com.
A cutting tool dedicated to producing one part feature is all well and good, but one that performs multiple operations is often more cost-effective—even if it’s a special. A German supplier to the automotive engineering industry found that to be the case and now needs just one tool instead of the three previously required to manufacture an aluminum crash box, a device that absorbs energy in case of an accident, with a towing hook fixture.
The extruded aluminum profile is supplied to the manufacturer complete with a core hole, which in the previous tooling setup had to be precisely predrilled to produce the threaded hole. Next, the chamfers were countersunk using two tools, and a tap cut the thread.
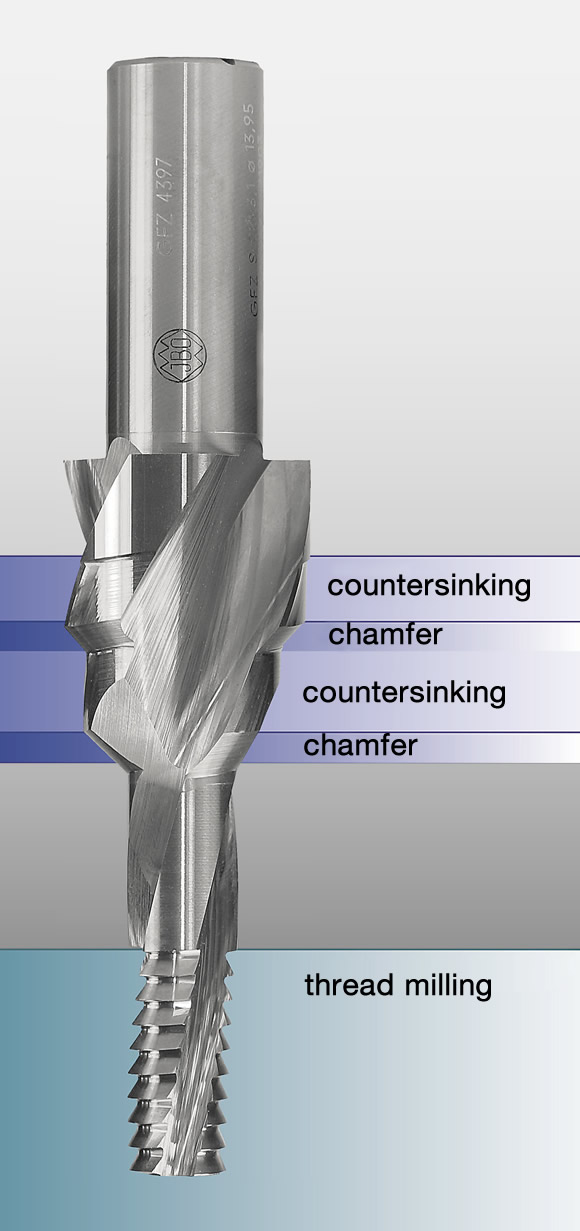
The combination tool performs two countersinking and one thread milling operation in one clamping.
In addition to the drill, three different tools, therefore, were needed to complete the machining operation, which consumed time for changing tools between steps. To optimize this operation, the manufacturer turned to Albstadt, Germany-based Johs. Boss GmbH & Co. KG—JBO for short. (J.M. Sales – USA, Troy, Mich., is the U.S. sales representative.)
Within 3 weeks, JBO had designed, produced and supplied a new solid-carbide combination tool that performs the two countersinking and one threadmaking tasks in a single clamping. The hole still needs to be predrilled, but the accuracy requirements are not as high.
A closer look at the overall machining sequence using the combination tool reveals that countersinking at 1,200 mm/min. produces two chamfers before the tool is withdrawn from the hole to remove chips and then is applied for thread milling at 1,000 mm/min. Spindle speed is 6,000 rpm. The time savings achieved for each part compared with the previous process is 9 seconds. Two parts are produced for each clamping in a double-spindle vertical milling center.
With runs of 2,500 to 3,000 parts per week, this faster cycle time equals an overall time gain of 6.25 to 7.5 hours per run. Assuming an hourly machine rate of about $130.80, this adds up to cost savings of $3,270 to $3,924 per month. In addition, this time gain generates additional capacity for more orders or higher volumes.
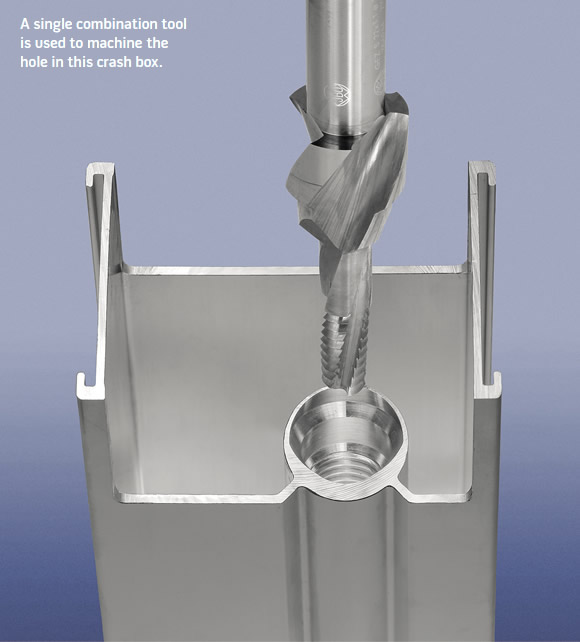
Milling rather than tapping a thread generally results in a higher-quality thread surface coupled with better dimensional stability of the thread. This machining method should always be considered, particularly for costly and complex parts, according to JBO. Taken together with the level of process reliability achieved, tangible cost savings can be realized and machining risks averted with thread milling.
JBO added that tapping frequently creates chip-removal problems, such as chip jamming, leading to tap breakage. When that occurs, the tool and workpiece are often consigned to the scrap heap.
Because a thread mill circular interpolates in the hole, chip loading is not a problem. Even a slightly out-of-center offset of the core hole will not cause tool breakage. However, if a thread mill breaks, threading can continue using a new tool. In addition, unlike a tap, a thread mill performs a single, uninterrupted cut, considerably simplifying chip evacuation, according to JBO.
JBO also assisted the manufacturer in programming the vertical milling machine used for the job and supported the shop during introduction of the combination tool, from the trial run through series production that began in October 2012.
Because the first tool is still operating, it is not yet possible to predict its service life. In case of tool wear, the machining program can correct the diameter of the circular movement.
The time savings achieved has improved capacity utilization. Simpler logistical procedures—reduced stock, less time spent in tool management—offer additional cost benefits.
Related Glossary Terms
- countersink
countersink
Tool that cuts a sloped depression at the top of a hole to permit a screw head or other object to rest flush with the surface of the workpiece.
- countersinking
countersinking
Cutting a beveled edge at the entrance of a hole so a screw head sits flush with the workpiece surface.
- fixture
fixture
Device, often made in-house, that holds a specific workpiece. See jig; modular fixturing.
- gang cutting ( milling)
gang cutting ( milling)
Machining with several cutters mounted on a single arbor, generally for simultaneous cutting.
- milling
milling
Machining operation in which metal or other material is removed by applying power to a rotating cutter. In vertical milling, the cutting tool is mounted vertically on the spindle. In horizontal milling, the cutting tool is mounted horizontally, either directly on the spindle or on an arbor. Horizontal milling is further broken down into conventional milling, where the cutter rotates opposite the direction of feed, or “up” into the workpiece; and climb milling, where the cutter rotates in the direction of feed, or “down” into the workpiece. Milling operations include plane or surface milling, endmilling, facemilling, angle milling, form milling and profiling.
- milling machine ( mill)
milling machine ( mill)
Runs endmills and arbor-mounted milling cutters. Features include a head with a spindle that drives the cutters; a column, knee and table that provide motion in the three Cartesian axes; and a base that supports the components and houses the cutting-fluid pump and reservoir. The work is mounted on the table and fed into the rotating cutter or endmill to accomplish the milling steps; vertical milling machines also feed endmills into the work by means of a spindle-mounted quill. Models range from small manual machines to big bed-type and duplex mills. All take one of three basic forms: vertical, horizontal or convertible horizontal/vertical. Vertical machines may be knee-type (the table is mounted on a knee that can be elevated) or bed-type (the table is securely supported and only moves horizontally). In general, horizontal machines are bigger and more powerful, while vertical machines are lighter but more versatile and easier to set up and operate.
- milling machine ( mill)2
milling machine ( mill)
Runs endmills and arbor-mounted milling cutters. Features include a head with a spindle that drives the cutters; a column, knee and table that provide motion in the three Cartesian axes; and a base that supports the components and houses the cutting-fluid pump and reservoir. The work is mounted on the table and fed into the rotating cutter or endmill to accomplish the milling steps; vertical milling machines also feed endmills into the work by means of a spindle-mounted quill. Models range from small manual machines to big bed-type and duplex mills. All take one of three basic forms: vertical, horizontal or convertible horizontal/vertical. Vertical machines may be knee-type (the table is mounted on a knee that can be elevated) or bed-type (the table is securely supported and only moves horizontally). In general, horizontal machines are bigger and more powerful, while vertical machines are lighter but more versatile and easier to set up and operate.
- tap
tap
Cylindrical tool that cuts internal threads and has flutes to remove chips and carry tapping fluid to the point of cut. Normally used on a drill press or tapping machine but also may be operated manually. See tapping.
- tapping
tapping
Machining operation in which a tap, with teeth on its periphery, cuts internal threads in a predrilled hole having a smaller diameter than the tap diameter. Threads are formed by a combined rotary and axial-relative motion between tap and workpiece. See tap.
- threading
threading
Process of both external (e.g., thread milling) and internal (e.g., tapping, thread milling) cutting, turning and rolling of threads into particular material. Standardized specifications are available to determine the desired results of the threading process. Numerous thread-series designations are written for specific applications. Threading often is performed on a lathe. Specifications such as thread height are critical in determining the strength of the threads. The material used is taken into consideration in determining the expected results of any particular application for that threaded piece. In external threading, a calculated depth is required as well as a particular angle to the cut. To perform internal threading, the exact diameter to bore the hole is critical before threading. The threads are distinguished from one another by the amount of tolerance and/or allowance that is specified. See turning.