END USER: Suburban Manufacturing Co., (440) 953-2024, www.submfg.com.
CHALLENGE: Reduce downtime on three aging horizontal machining centers.
SOLUTION: Replace them with two new HMCs.
SOLUTION PROVIDERS: Gosiger Inc., (877) 288-1538, www.gosiger.com; Okuma America Corp., (704) 588-7000, www.okuma.com.
In business for more than 3 decades, Suburban Manufacturing Co. has a 30,000-sq.-ft. CNC machine shop, employs 65 workers and is doubling in size every 3 years.
As a result, the Eastlake, Ohio, company is quickly moving up the ranks in the Weatherhead 100, an index of northeast Ohio’s fasting growing companies. In 2011, Suburban ranked 69th, and moved to 41st last year. According to Rick Grice, company president and founder, the essential ingredients in keeping Suburban successful and competitive are its innovative people and that the company is employee-owned, which it has been for nearly 10 years.
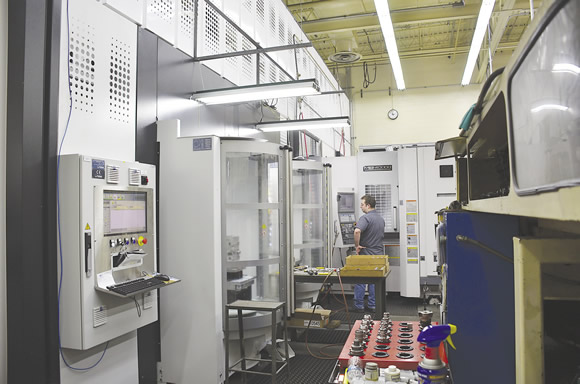
One of two new Okuma MB-4000H horizontal machining centers at Suburban Manufacturing.
In addition, Suburban’s equipment helps it handle whatever comes through the door. Vice President Brian Nuibe likes to call the company a “true job shop.” He said: “We have vertical and horizontal machining centers, single- and multiple-spindle CNC lathes, saws, hones, sand blasting, part marking—a huge array of operations. We run all grades of aluminum, stainless, brass, Hastelloy, Inconel and titanium. We run bar, plate, castings, forgings and extrusions. We tackle a mixture of prismatic and cylindrical parts. We do everything from prototyping to production.”
Three of the shop’s HMCs, however, were aging and needed a lot of repair, Nuibe noted. Although Suburban paid thousands of dollars for parts and labor, downtime was a more significant cost. “Toward the end, a couple of those machines were down about 20 percent of the time,” he said.
Suburban decided to shop for replacement machines. Nuibe said the company contacted several machine tool builders and examined machines at other shops’ facilities to determine which ones could achieve its tolerances and surface finish requirements, which are down to 0.0005" and 32 µin. Ra, respectively. The machines also had to be “lightning fast.”
Based on its previous experience with the MA-500 HMC from Okuma America Corp., Charlotte, N.C., and the Fastems flexible manufacturing system, Suburban purchased two new Okuma MB-4000H HMCs, replacing the three HMCs, and an Okuma PALLETACE FMS, which is integrated with both machines. Nuibe pointed out that the main difference between its MA-500 and the MB-4000H is the former is a 50-taper machine and accepts a 500mm pallet, whereas the latter is a 40-taper machine and accepts a 400mm pallet. “Other than that, they’re almost identical,” he said.
According to Grice, the additional reasons for selecting Okuma machines over the other brands include Okuma’s reputation for building long-lasting machines and the solid service and support provided by Okuma’s distributor, Gosiger Inc., Dayton, Ohio. “We have an Okuma MC-50 horizontal machining center with a 50-tool ATC, CAT 50 taper, 50-hp motor and multiple pallets,” Grice said. “We call it the ‘green monster.’ This CNC machine is more than 25 years old and it’s still running today, holding great tolerances.”
Grice added that the training from Gosiger, which included two machinists spending 3 days at the distributor’s facility and a similar amount of on-site training, was an important factor in purchasing the new machines. “They go to great lengths to fully understand the CNC machines and to make sure we do too,” he said.
Nuibe noted Suburban is leaning more on HMCs because idle spindle time is almost eliminated with the pallet system in place. “We put a fixture in and do all the loading and unloading outside the machine while the machine is running,” he said. “Further, we’re trying to combine operations at every turn. With the vertical machining centers and lathes, we may have to do three to four setups. With a horizontal machining center, we do a single setup, saving all that setup time.”
Not only is time saved with single setups, but costly setup variables are eliminated as well. Every time an operator fixtures or refixtures a part, he introduces the possibility—and likelihood—of process variability, which may result in out-of-spec parts that require rework or generate scrap. The fewer variables in the process, the greater the odds of the first part being a good part.
Related Glossary Terms
- centers
centers
Cone-shaped pins that support a workpiece by one or two ends during machining. The centers fit into holes drilled in the workpiece ends. Centers that turn with the workpiece are called “live” centers; those that do not are called “dead” centers.
- computer numerical control ( CNC)
computer numerical control ( CNC)
Microprocessor-based controller dedicated to a machine tool that permits the creation or modification of parts. Programmed numerical control activates the machine’s servos and spindle drives and controls the various machining operations. See DNC, direct numerical control; NC, numerical control.
- fixture
fixture
Device, often made in-house, that holds a specific workpiece. See jig; modular fixturing.
- flexible manufacturing system ( FMS)
flexible manufacturing system ( FMS)
Automated manufacturing system designed to machine a variety of similar parts. System is designed to minimize production changeover time. Computers link machine tools with the workhandling system and peripherals. Also associated with machine tools grouped in cells for efficient production. See cell manufacturing.
- flexible manufacturing system ( FMS)2
flexible manufacturing system ( FMS)
Automated manufacturing system designed to machine a variety of similar parts. System is designed to minimize production changeover time. Computers link machine tools with the workhandling system and peripherals. Also associated with machine tools grouped in cells for efficient production. See cell manufacturing.
- machining center
machining center
CNC machine tool capable of drilling, reaming, tapping, milling and boring. Normally comes with an automatic toolchanger. See automatic toolchanger.