END USER: Volkswagen AG, +49 5341-230, www.volkswagen.de.
CHALLENGE: Minimize lubricant for a mass-production cylinder head line.
SOLUTION: Switch to minimum quantity lubrication.
SOLUTION PROVIDER: bielomatik inc., (248) 446-9910, www.bielomatik.com.
Volkswagen AG’s site in Salzgitter, Germany, is one of the largest engine plants in the world. Covering 2.8 million sq. meters, the plant manufactures about 7,000 engines in more than 370 variants every day, including ones for Volkswagen, Audi and Bugatti brands.
The plant has become the world’s first mass-production line for cylinder heads that uses minimal quantity lubrication (MQL), or near-dry machining, according to the company. A mixture of compressed air and tiny droplets of oil provide the needed lubrication, replacing the coolant lubricants previously used.
From the start, Michael Knauf, head of tool planning, was involved in incorporating the technology. Since 2008, he has been responsible for testing MQL technology at the Salzgitter plant and merging it into the operation’s most demanding processes.
The beginnings of MQL use at the plant go back to the late 1990s. Later, in the 2000s, the plant moved from machining steel and cast parts via MQL to also machining simple aluminum parts with MQL. Even at that time, the plant was using MQL systems from bielomatik Leuze GmbH + Co. KG, Neuffen, Germany. (The U.S. subsidiary is bielomatik inc., New Hudson, Mich.)
The next milestone was the “innovative” MQL production line at the Salzgitter plant for dry machining of aluminum cylinder heads. The line was installed in 2009 and entered into series operation in 2010.
A key motivating factor for using MQL is that it offers clean production. The swarf is dry, the machine tools only require cleaning once every 2 to 3 weeks, machine operators do not need any special clothing or gloves, and there are no oily, slippery work surfaces.
A second motivating factor is reducing the cost of lubricant use as well as preparation, maintenance and disposal costs.
Using conventional lubricants, VW found approximately 81 to 99 gal. per minute (305 to 375 l/min.) of lubricant is in circulation for a twin-spindle GROB G 320 machining center. Therefore, when 20 machines produce, for example, 2,000 cylinder heads a day, about 2,113 gpm (8,000 l/min.) of lubricant is required from the corresponding fluid circuit.
Previously, lubricant consumption, including evaporation and carryover, of 1.1 to 1.4 gal. (4.2 to 4.3 l) per cylinder head was the norm. Now, no more than 0.002 to 0.003 gal. (7 to 10 ml) of lubricant per cylinder head is required.
Notably, in a machine tool with two spindles, only slightly more than 0.004 gal. (17 ml) of lubricant is used per spindle per hour.
Because the supply of lubricant is only on when the machine is cutting and is switched off when traversing and between operations, VW has reaped additional operational savings. Water consumption has also been significantly reduced. Only one washing process is required where previously two were necessary.
The previous lubrication system used filter media to clean the lubricant. This filtration process risked feeding minute swarf particles to the tool and recutting them, causing scratches and affecting the part’s finish. Because MQL technology always uses virgin oil, this risk is eliminated.
Knauf stated: “With MQL, we are making a ‘quantum leap’ toward reducing operating costs across the entire process. The use of lubricants decreased by approximately 98 percent per cylinder head thanks to MQL machining. In comparison to wet machining, savings of around 90 percent have been made with respect to the water required per cylinder head, and CO2 emissions have been reduced by 54 percent.”
The GROB G 320 machine allows tool changes of 4.2 seconds (chip-to-chip time). This is not a problem because bielomatik’s MQL 2-channel system transports the lubricant directly to the cutting edge of the tool with an MQL on/off reaction time of 0.1 second.
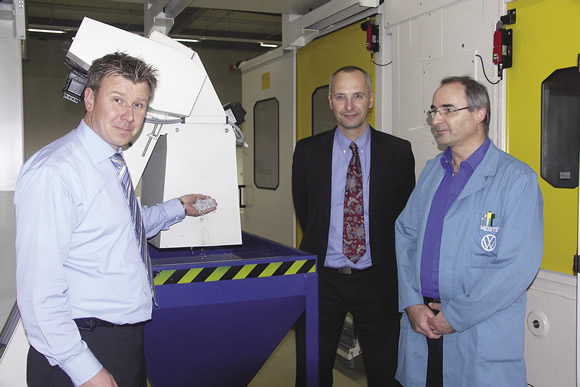
Michael Knauf, head of tool planning (left), Matthias Haug, sales manager for lubrication technology at bielomatik (center), and Bernd Gasch, foreman responsible for cylinder head production, stand at a conveyor where dry swarf (inset) is transported.
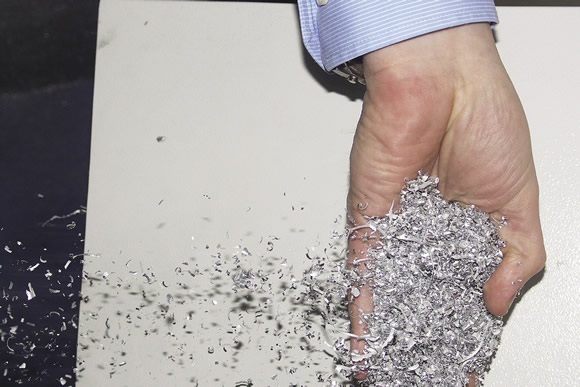
Tool changes also often require the oil quantity to be modified, and the MQL two-channel system is capable of this task: Oil and air are mixed in the toolholder close to the operation being performed.
In the case of the MQL two-channel system, an oil film is transported by air to the cutting edge. Oil dosing is performed using bielomatik’s valve technology. This reportedly results in accurate and reproducible oil dosing that is independent of environmental fluctuations. Exact dosing is possible for small and large tools alike.
In addition to the high level of dosing accuracy, another advantage of the dosing procedure being independent of the airflow is that tools that do require high levels of lubricant can always be supplied with a sufficient quantity.
One particular challenge with MQL is how to deal with the introduction of heat into the part. To precisely control heating of the part, the process parameters have to be considered individually. Optimization of work sequences when machining cylinder heads is essential.
Knauf stated: “To ensure the required accuracy, the process steps have to be thought out to improve part quality through targeted process control. Heat is ultimately no longer dissipated by the cooling lubricant, but primarily via the swarf. We know exactly how much heat is introduced into the part in each production step.”
The Salzgitter plant’s ultimate aim is establishing a complete MQL factory in line with Volkswagen’s sustainability strategy. The latest project at the plant involves grinding camshafts using MQL.
However, “There isn’t a switch to go from wet to dry,” Knauf said. “The process requires know-how and employees who are prepared to develop such know-how about MQL. You have to investigate the causes of tool failures and optimize procedures with respect to the machine, tools, toolholders, oil and MQL system. We have defined basic rules and take these into account from process to process.”
Related Glossary Terms
- coolant
coolant
Fluid that reduces temperature buildup at the tool/workpiece interface during machining. Normally takes the form of a liquid such as soluble or chemical mixtures (semisynthetic, synthetic) but can be pressurized air or other gas. Because of water’s ability to absorb great quantities of heat, it is widely used as a coolant and vehicle for various cutting compounds, with the water-to-compound ratio varying with the machining task. See cutting fluid; semisynthetic cutting fluid; soluble-oil cutting fluid; synthetic cutting fluid.
- grinding
grinding
Machining operation in which material is removed from the workpiece by a powered abrasive wheel, stone, belt, paste, sheet, compound, slurry, etc. Takes various forms: surface grinding (creates flat and/or squared surfaces); cylindrical grinding (for external cylindrical and tapered shapes, fillets, undercuts, etc.); centerless grinding; chamfering; thread and form grinding; tool and cutter grinding; offhand grinding; lapping and polishing (grinding with extremely fine grits to create ultrasmooth surfaces); honing; and disc grinding.
- machining center
machining center
CNC machine tool capable of drilling, reaming, tapping, milling and boring. Normally comes with an automatic toolchanger. See automatic toolchanger.
- process control
process control
Method of monitoring a process. Relates to electronic hardware and instrumentation used in automated process control. See in-process gaging, inspection; SPC, statistical process control.
- swarf
swarf
Metal fines and grinding wheel particles generated during grinding.
- toolholder
toolholder
Secures a cutting tool during a machining operation. Basic types include block, cartridge, chuck, collet, fixed, modular, quick-change and rotating.