END USER: Conroe Machine LLC, (936) 494-2566, www.conroemachine.com.
CHALLENGE: Increase throughput and reduce scrap when machining thrust bearing races for down-hole mud motors.
SOLUTION: An automated gaging system integrated into a turning cell.
SOLUTION PROVIDER: Renishaw Inc., (847) 286-9953, www.renishaw.com.
Conroe (Texas) Machine LLC is doing what most machine shops only dream of—hard turning a family of parts around the clock in an unmanned cell that operates a “self-controlled” process. The finish-turning cell integrates a FANUC M20iA 6-axis robot with the Equator gaging system and EX-IO software from Renishaw Inc., Hoffman Estates, Ill., to provide 100 percent part inspection and automatically compensate the cutting tools on an Okuma 2SP-250H twin-spindle, dual-gantry lathe.
Founded by Murray “Tippy” Touchette in 2000, the job shop’s location near Houston results in a high percentage of business coming from the oil and gas industry, mainly for drilling components. One of its continuously running jobs for the industry is producing thrust bearing races for down-hole mud motors. Part ODs range from about 3 " to 6 " (7.62cm to 15.24cm), with tolerances as tight as ±0.001 " (0.025mm).
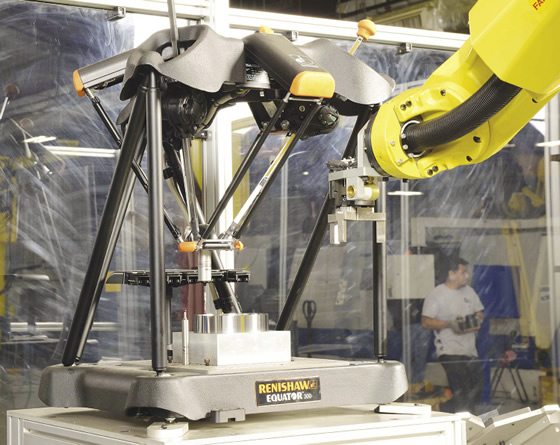
The Equator gaging system from Renishaw uses touch probing to find the center of a thrust bearing race and then scans the part surface to complete the measurement cycle.
Initially, the 150-employee company machined the races on two lathes, with one or two workers manning those machines and manually transporting parts back and forth as one lathe machined one side of a part and the other machined the other side, explained James Wardell, CNC programmer. Conroe Machine later purchased a FANUC robot to transfer the parts between machines and added a second robotic turning cell to increase throughput. The shop sends the semifinished parts to be case-hardened to 65 HRC at a depth of 0.070 " (1.7mm) before finish turning.
Measuring the parts, however, was done manually with calipers and a bore gage. “We weren’t even inspecting the ball radius because there was no way to do that manually,” Wardell said. In addition, because cycle time was as short as 98 seconds, the operator could inspect only every fifth part. “This scenario was not accurate enough,” he said. “We wanted 100 percent inspection on the races. We needed a more reliable system.”
To improve part quality, the company decided to rough the parts on the two existing turning cells but create a fully automated cell for finishing, including part loading, cutting tool compensation, post-process measurement, part engraving and boxing and palletizing the parts.
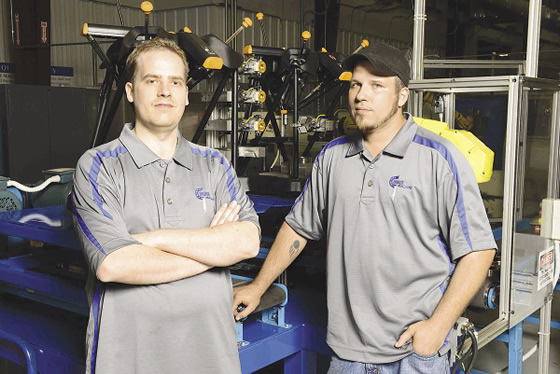
James Wardell, CNC Programmer, (left) and Jeff Buck, robotics technician, helped develop Conroe Machine’s hard turning cells with their integration, software and programming skills.
But selecting an appropriate part measurement system proved challenging. “Originally, we looked at white-light laser inspection because of its speed, but the parts are too reflective,” Wardell said. He added that Conroe Machine considered a shop-floor coordinate measuring machine, but determined it would be too slow; as for hard gaging, each race size needs a separate gage, which the company determined would have cost about $200,000, more than it wanted to spend. Changing gages would have consumed up to 2 hours, leading to unacceptable delays.
While working on other projects, Renishaw’s sales representative suggested the Equator gaging system as a possible solution for the part measurement problem. After reviewing it, Conroe Machine purchased its initial Equator for about $35,000, including the probes.
Wardell said: “With Equator, we increased our throughput tremendously. The Equator’s speed allows it to easily keep pace with the process. We’re doing about 600 parts a day and, at the price we’re charging for them, we ended up paying for the entire system—machine and all—in about 18 days.”
The Equator uses the comparison method of measuring, according to Renishaw. A master part, with known measurements taken on a CMM, is used to “master” the Equator, with all subsequent measurements compared to the master. Repeatability is 0.00007 " (0.002mm) immediately after mastering. “We remaster only once a day, because our shop is climate controlled to 72° F (22.2° C),” Wardell said, noting the process, which includes probe calibration, takes 5 to 10 minutes.
The Equator uses an SP25 probe for touch and scanning data collection at speeds up to 1,000 points per second. Probe styli are stored in an integral six-port changing rack. Although it can be used manually, the Equator’s EZ-IO software enables integration of the measurement system into automated work cells.
In practice, the Okuma lathe’s two part carousels are loaded with about 300 workpieces. The lathe’s dual-gantry loaders feed the spindles and place finished parts on a chute leading to a conveyor for robotic pickup. The robot places the part on the Equator for measurement and, if acceptable, transfers it to the engraving machine and boxes the finished part.
Tool compensation software is available, but Wardell explained that he developed his own tool compensation software to run on the Okuma’s OSP control, which has an open-architecture, PC-based operating platform. This was because the commercially available software is not designed for a dual-gantry machine and it would have taken more time and money to set up the software to run both gantries. “It’s almost acting like two different machines,” he said, adding that one gantry transfers a part to the other gantry at a turnover station on top of the lathe.
Related Glossary Terms
- calibration
calibration
Checking measuring instruments and devices against a master set to ensure that, over time, they have remained dimensionally stable and nominally accurate.
- computer numerical control ( CNC)
computer numerical control ( CNC)
Microprocessor-based controller dedicated to a machine tool that permits the creation or modification of parts. Programmed numerical control activates the machine’s servos and spindle drives and controls the various machining operations. See DNC, direct numerical control; NC, numerical control.
- family of parts
family of parts
Parts grouped by shape and size for efficient manufacturing.
- feed
feed
Rate of change of position of the tool as a whole, relative to the workpiece while cutting.
- hard turning
hard turning
Single-point cutting of a workpiece that has a hardness value higher than 45 HRC.
- lathe
lathe
Turning machine capable of sawing, milling, grinding, gear-cutting, drilling, reaming, boring, threading, facing, chamfering, grooving, knurling, spinning, parting, necking, taper-cutting, and cam- and eccentric-cutting, as well as step- and straight-turning. Comes in a variety of forms, ranging from manual to semiautomatic to fully automatic, with major types being engine lathes, turning and contouring lathes, turret lathes and numerical-control lathes. The engine lathe consists of a headstock and spindle, tailstock, bed, carriage (complete with apron) and cross slides. Features include gear- (speed) and feed-selector levers, toolpost, compound rest, lead screw and reversing lead screw, threading dial and rapid-traverse lever. Special lathe types include through-the-spindle, camshaft and crankshaft, brake drum and rotor, spinning and gun-barrel machines. Toolroom and bench lathes are used for precision work; the former for tool-and-die work and similar tasks, the latter for small workpieces (instruments, watches), normally without a power feed. Models are typically designated according to their “swing,” or the largest-diameter workpiece that can be rotated; bed length, or the distance between centers; and horsepower generated. See turning machine.
- robotics
robotics
Discipline involving self-actuating and self-operating devices. Robots frequently imitate human capabilities, including the ability to manipulate physical objects while evaluating and reacting appropriately to various stimuli. See industrial robot; robot.
- turning
turning
Workpiece is held in a chuck, mounted on a face plate or secured between centers and rotated while a cutting tool, normally a single-point tool, is fed into it along its periphery or across its end or face. Takes the form of straight turning (cutting along the periphery of the workpiece); taper turning (creating a taper); step turning (turning different-size diameters on the same work); chamfering (beveling an edge or shoulder); facing (cutting on an end); turning threads (usually external but can be internal); roughing (high-volume metal removal); and finishing (final light cuts). Performed on lathes, turning centers, chucking machines, automatic screw machines and similar machines.