END USER: Seeger Präzisionsdrehteile GmbH, +49 7553-8258282, www.seeger-salem.de.
CHALLENGE: Increase flexibility and repeatability when machining high-volume auto parts.
SOLUTION: A hydraulic stationary clamping system.
SOLUTION PROVIDERS: Hainbuch America Corp., (800) 281-5734, www.hainbuchamerica.com; Hainbuch GmbH, +49 7144-907-0, www.hainbuch.com.
For 15 years, Wilhelm Seeger led a double life. In addition to working as production supervisor at a large manufacturer, he ran his own contract manufacturing operation. Seeger’s business, Seeger Präzisionsdrehteile GmbH, Salem-Neufrach, Germany, progressively grew and, in 2005, he became entirely his own boss. It was easier to make this decision because Seeger’s two sons, Moritz and Manfred, would soon join his company after training and university studies and help grow the family business together.
Fast forward to the present, where his two sons share management responsibilities, including handling new orders and negotiating customer contracts. The company employs nearly 100 people, operates three shifts and delivered nearly 49 million turned parts in 2012. “Although my father is no longer the owner, he is the undisputed boss,” Moritz Seeger joked.
Seventy percent of the company’s customers are suppliers to the automotive industry, 25 percent are in the machine tool industry and the remaining 5 percent are from other industries. To produce the parts, such as gears and other round parts for transmissions, their shop has 65 sliding-headstock automatic lathes from Star, 25 fixed-headstock automatic lathes from Miyano and three Haas machining centers. All the machines are equipped with FANUC controls so parts can be transferred from one machine to another, if needed. “There is no mishmash,” Moritz Seeger said. “All employees are thoroughly familiar with all the machines. That is the flexibility we need here.”
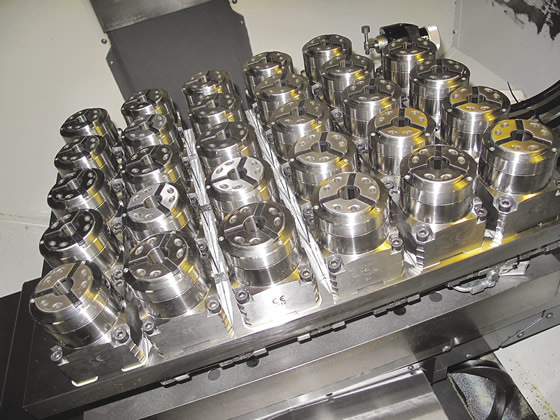
Thirty 32mm-capacity Hydrok 32 hydraulic stationary chucks fit on the machine table of a Haas machining center at Seeger Präzisionsdrehteile.
Four years ago, the company received an order for a component for the timing gear in gas and diesel engines and envisioned delivering 300,000 parts per year. To accommodate production of this part family, Seeger needed a new workpiece clamping system. It considered a separate clamping fixture manufactured for the part family or a flexible system in which part diameters can vary.
Although some in the company advocated for a dedicated clamping fixture that would have multiple part positions and sequential part loading, the fixture would become “worthless” from one day to the next when a workpiece diameter changed by as little as 1mm, according to the company. To change over between part models, the entire tombstone would need to be removed from the machine and replaced. In addition, because a tombstone can weigh 200 to 300 kg (441 to 661 lbs.), the company would need to purchase a crane to remove and replace the tooling.
While reading a trade magazine, Moritz Seeger learned about the Hydrok hydraulic stationary clamping system from Hainbuch GmbH, Marbach, Germany. (Hainbuch America Corp. is located in Germantown, Wis.) With the Hainbuch system, only a clamping head weighing a few pounds needs to be removed and replaced. The rest of the fixture stays on the machine. According to Hainbuch, users can replace each clamping head in less than 30 seconds, compared to several hours when changing and requalifying a standard fixture.
Uwe Fischer, a technical consultant in outside sales at Hainbuch, introduced the modular system to the Seegers. “What counted for them were flexibility and fast changeover,” Fischer said. “The smallest stationary chuck in this system, the Hydrok 32, enables multiple clamping where space is at a premium.” (The Hydrok 32 has a 32mm capacity.)
When turning and drilling the timing gear component, which has three different diameters, the clamping system enables Seeger Präzisionsdrehteile to achieve the required 5µm position and guide bore accuracies. In addition to achieving the flexibility and accuracy requirements, Moritz Seeger said the Hydrok chucks met the contract manufacturer’s space requirements on its Haas DT-1 machining center.
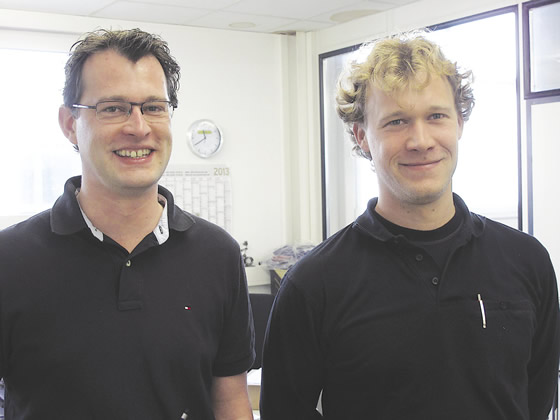
Brothers Moritz (left) and Manfred Seeger share management responsibilities at Seeger Präzisionsdrehteile, while Moritz also focuses on machining and Manfred is the automation specialist.
“Precisely 30 size-32 Hydroks fit on the machine table plus traverse distances, and the space is optimally utilized,” Moritz Seeger said. “The base plate with the Hydroks remains stationary in the machine and we only change the clamping heads, depending on the diameter.”
Fischer added: “Today, the intelligence of the system is in the clamping heads. The individual segments of the clamping head are vulcanized together and hardened. Thus, we achieve this consistent clamping force and repeatability.”
Seeger Präzisionsdrehteile continues to meet demanding customer requirements and is growing. “Large customers want you to grow with them,” Moritz Seeger said. “Starting in 2014, instead of the 300,000 parts we deliver today, we should deliver one million parts.”
Related Glossary Terms
- centers
centers
Cone-shaped pins that support a workpiece by one or two ends during machining. The centers fit into holes drilled in the workpiece ends. Centers that turn with the workpiece are called “live” centers; those that do not are called “dead” centers.
- chuck
chuck
Workholding device that affixes to a mill, lathe or drill-press spindle. It holds a tool or workpiece by one end, allowing it to be rotated. May also be fitted to the machine table to hold a workpiece. Two or more adjustable jaws actually hold the tool or part. May be actuated manually, pneumatically, hydraulically or electrically. See collet.
- fixture
fixture
Device, often made in-house, that holds a specific workpiece. See jig; modular fixturing.
- machining center
machining center
CNC machine tool capable of drilling, reaming, tapping, milling and boring. Normally comes with an automatic toolchanger. See automatic toolchanger.
- turning
turning
Workpiece is held in a chuck, mounted on a face plate or secured between centers and rotated while a cutting tool, normally a single-point tool, is fed into it along its periphery or across its end or face. Takes the form of straight turning (cutting along the periphery of the workpiece); taper turning (creating a taper); step turning (turning different-size diameters on the same work); chamfering (beveling an edge or shoulder); facing (cutting on an end); turning threads (usually external but can be internal); roughing (high-volume metal removal); and finishing (final light cuts). Performed on lathes, turning centers, chucking machines, automatic screw machines and similar machines.