END USER: D&N Machining Co., (479) 996-2738, www.dnmachining.com.
CHALLENGE: Tap 100 2"-8 blind-holes without breaking the tap or scrapping a part.
SOLUTION: A tap engineered to effectively produce threads in holes more than ½" in diameter.
SOLUTION PROVIDER: OSG Tap & Die Inc., (800) 837-2223, www.osgtool.com.
A single mistake when tapping large, complex, expensive parts for the energy industry can make a job shop go dark. Finding a tap that can execute the job accurately, efficiently and affordably when threading a difficult-to-tap workpiece only adds to the challenge.
D&N Machining Co., Greenwood, Ark., faced this situation when machining two outer piston ring housings for a customer in the oil field industry. The housings are 4140 steel forgings that weigh up to 5,000 lbs. each, have a hardness of 32 HRC and feature a 30" bolt circle and 32" major OD. They required D&N to tap 50 2"-8 blind-holes 3½ " deep in each housing—100 holes total.
To ensure it had a tap for the job, D&N purchased the one tap the shop could find in stock from a toolmaker. “Purchasing the tap was basically done out of necessity,” said Matt Hankins, owner of D&N.
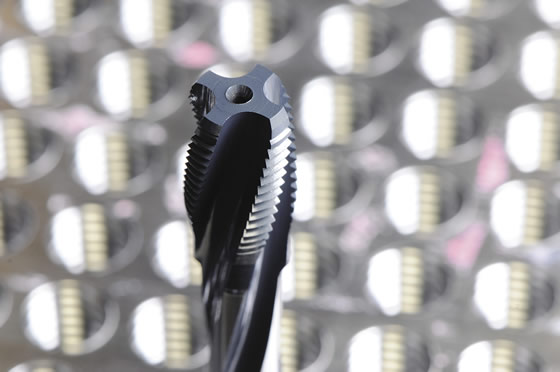
The HY-PRO HXL tap from OSG is for threading difficult-to-cut alloy steels, such as 4140 and 4130. Below: An HY-PRO HXL tap shows little wear after tapping 100 holes in 4140 at D&N Machining.
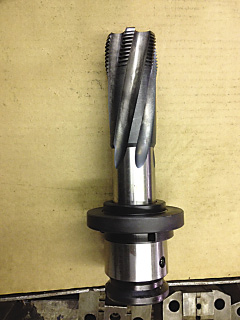
However, the toolmaker recommended tapping at 10 sfm, which seemed too slow and could possibly cause the tap to break during the cutting-force-intensive threading operation, according to Hankins. Because of the part size, he thought it would be problematic to locate an EDM large enough to remove a broken tap. Also, with multiple machining hours already invested in each expensive workpiece, scrap wasn’t an option. There was no room for error.
When the shop had nearly completed the job but had not yet tapped the holes, Ron Portwine, district manager for OSG Tap & Die Inc., Glendale Heights, Ill., visited D&N. Portwine evaluated the application and informed Hankins that OSG had the needed-size tap. Not only was OSG’s HY-PRO HXL HSS tap suitable for the job, but the toolmaker had 12 of the taps in stock and, at about $1,200 each, was 40 percent less than the competitor’s tool.
In addition, Portwine recommended running the tap at 25 sfm (48 rpm at 6 ipm) and even contacted his colleague Mike Brzezniak to confirm his recommendations based on the application details and Brzezniak’s success with the tap being applied by part manufacturers in the Houston energy market.
D&N purchased two of the taps from OSG and ran them the next day on the shop’s Haas HS-4R horizontal CNC mill, using flood coolant. The parts were held in a fixture D&N produced in-house that has large V blocks with hydraulic chains as the clamps, Hankins noted.
The tap ran in a tension-compression toolholder at the recommended speed and successfully threaded the 100 holes. The machine operator noted the tap provided effective chip control, generating straw-colored chips predominantly shaped like sixes and nines.
After the job, the tap still looked new, according to Hankins, who plans to use it for other applications and possibly for repeats of the initial job. “This was the first run on the part and our customer will dictate the return of the job,” he said.
As for the other tap, D&N promptly returned it.
Related Glossary Terms
- alloy steels
alloy steels
Steel containing specified quantities of alloying elements (other than carbon and the commonly accepted amounts of manganese, sulfur and phosphorus) added to cause changes in the metal’s mechanical and/or physical properties. Principal alloying elements are nickel, chromium, molybdenum and silicon. Some grades of alloy steels contain one or more of these elements: vanadium, boron, lead and copper.
- computer numerical control ( CNC)
computer numerical control ( CNC)
Microprocessor-based controller dedicated to a machine tool that permits the creation or modification of parts. Programmed numerical control activates the machine’s servos and spindle drives and controls the various machining operations. See DNC, direct numerical control; NC, numerical control.
- coolant
coolant
Fluid that reduces temperature buildup at the tool/workpiece interface during machining. Normally takes the form of a liquid such as soluble or chemical mixtures (semisynthetic, synthetic) but can be pressurized air or other gas. Because of water’s ability to absorb great quantities of heat, it is widely used as a coolant and vehicle for various cutting compounds, with the water-to-compound ratio varying with the machining task. See cutting fluid; semisynthetic cutting fluid; soluble-oil cutting fluid; synthetic cutting fluid.
- electrical-discharge machining ( EDM)
electrical-discharge machining ( EDM)
Process that vaporizes conductive materials by controlled application of pulsed electrical current that flows between a workpiece and electrode (tool) in a dielectric fluid. Permits machining shapes to tight accuracies without the internal stresses conventional machining often generates. Useful in diemaking.
- fixture
fixture
Device, often made in-house, that holds a specific workpiece. See jig; modular fixturing.
- hardness
hardness
Hardness is a measure of the resistance of a material to surface indentation or abrasion. There is no absolute scale for hardness. In order to express hardness quantitatively, each type of test has its own scale, which defines hardness. Indentation hardness obtained through static methods is measured by Brinell, Rockwell, Vickers and Knoop tests. Hardness without indentation is measured by a dynamic method, known as the Scleroscope test.
- high-speed steels ( HSS)
high-speed steels ( HSS)
Available in two major types: tungsten high-speed steels (designated by letter T having tungsten as the principal alloying element) and molybdenum high-speed steels (designated by letter M having molybdenum as the principal alloying element). The type T high-speed steels containing cobalt have higher wear resistance and greater red (hot) hardness, withstanding cutting temperature up to 1,100º F (590º C). The type T steels are used to fabricate metalcutting tools (milling cutters, drills, reamers and taps), woodworking tools, various types of punches and dies, ball and roller bearings. The type M steels are used for cutting tools and various types of dies.
- milling machine ( mill)
milling machine ( mill)
Runs endmills and arbor-mounted milling cutters. Features include a head with a spindle that drives the cutters; a column, knee and table that provide motion in the three Cartesian axes; and a base that supports the components and houses the cutting-fluid pump and reservoir. The work is mounted on the table and fed into the rotating cutter or endmill to accomplish the milling steps; vertical milling machines also feed endmills into the work by means of a spindle-mounted quill. Models range from small manual machines to big bed-type and duplex mills. All take one of three basic forms: vertical, horizontal or convertible horizontal/vertical. Vertical machines may be knee-type (the table is mounted on a knee that can be elevated) or bed-type (the table is securely supported and only moves horizontally). In general, horizontal machines are bigger and more powerful, while vertical machines are lighter but more versatile and easier to set up and operate.
- outer diameter ( OD)
outer diameter ( OD)
Dimension that defines the exterior diameter of a cylindrical or round part. See ID, inner diameter.
- tap
tap
Cylindrical tool that cuts internal threads and has flutes to remove chips and carry tapping fluid to the point of cut. Normally used on a drill press or tapping machine but also may be operated manually. See tapping.
- tapping
tapping
Machining operation in which a tap, with teeth on its periphery, cuts internal threads in a predrilled hole having a smaller diameter than the tap diameter. Threads are formed by a combined rotary and axial-relative motion between tap and workpiece. See tap.
- threading
threading
Process of both external (e.g., thread milling) and internal (e.g., tapping, thread milling) cutting, turning and rolling of threads into particular material. Standardized specifications are available to determine the desired results of the threading process. Numerous thread-series designations are written for specific applications. Threading often is performed on a lathe. Specifications such as thread height are critical in determining the strength of the threads. The material used is taken into consideration in determining the expected results of any particular application for that threaded piece. In external threading, a calculated depth is required as well as a particular angle to the cut. To perform internal threading, the exact diameter to bore the hole is critical before threading. The threads are distinguished from one another by the amount of tolerance and/or allowance that is specified. See turning.
- toolholder
toolholder
Secures a cutting tool during a machining operation. Basic types include block, cartridge, chuck, collet, fixed, modular, quick-change and rotating.