END USER: Milwaukee Machine Works, (414) 476-3285, www.milwaukeemachineworks.com.
CHALLENGE: Machine larger and more complex parts for the energy industry.
SOLUTION: A horizontal boring mill for machining parts up to 10' long.
SOLUTION PROVIDER: Fives Machining Systems Inc., (920) 906-2860, www.fivesmsi.com.
As wind turbine builders help slake the world’s seemingly unquenchable thirst for power, they design progressively larger and more complex turbines. Those turbines, in turn, require part manufacturers serving the sector to have machine tools that can handle the turbines’ behemoth parts.
Milwaukee (Wis.) Machine Works has an extensive history of making large parts for the energy industry, such as gearbox and generator housings and fluid end manifolds made of cast iron and 4340 steel. It found the marketplace was demanding parts bigger than its largest machine tool could handle, according to General Manager Mike Manna.
To determine which machine to purchase, MMW compared six on a matrix of more than 20 machine features and benefits, including machining envelope, horsepower, quill length, quill diameter and way capability. “The analysis assured we were systematically reviewing all relevant features to make sure the machine is capable of doing the type of work we needed it to do,” Manna said.
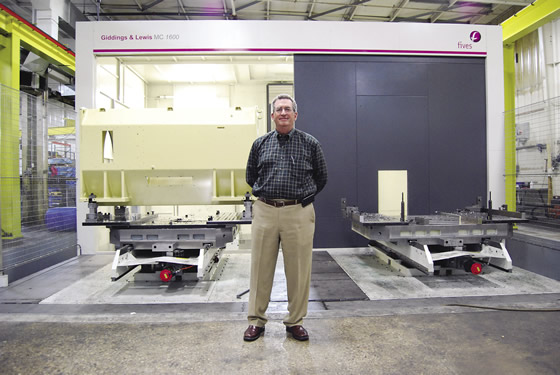
Mike Manna, general manager for Milwaukee Machine Works, notes the company’s new Giddings & Lewis MC 1600 horizontal boring mill enables automated large-part machining with its machining center capabilities.
Primarily based on that evaluation, MMW purchased a dual-pallet Giddings & Lewis MC 1600 horizontal boring mill from Fives Machining Systems Inc., Fond du Lac, Wis. In addition, MMW’s experience with its smaller G&L MC 1250 HBM influenced the decision, Manna pointed out. “The features and design of the two machines are very similar, shortening the learning curve for existing operators. Also, there are common components used in both machines, like the spindle assembly, which is a potential major spare part.”
The MC 1600 HBM is for 4-axis contour milling, boring, drilling and tapping. The shuttle system for the dual 63.0 "×63.0 " (1,600mm × 1,600mm) pallets ensures high spindle utilization, according to Fives. A built-in 360,000-position contouring rotary table with a programmable mechanical clamp handles parts weighing up to 55,000 lbs. (25,000 kg). The modular design allowed MMW to customize the machine with a four-speed, 3,500-rpm, 76-hp spindle and 120-tool magazine.
“Our primary business is large parts, some with more than 300 machined features, so the new boring mill not only expands our part capacity, it also boosts our efficiency with pallet changing and machining center capabilities,” Manna said. “Compared to the other machines on our list, we found the MC 1600 more technologically advanced. That’s important because our wind-gearbox customers are continually tightening tolerances as they look to extend the life of their finished systems.”
He noted MMW typically holds bore-to-bore centerline, perpendicularity and parallel tolerances of 0.001 " to 0.002 " (0.0254mm to 0.0508mm) over 20 " to 30 " (0.508m to 0.762m). “We expect this machine to hold this over the entire range of travel, even as our parts get larger. The extra capacity will allow us to expand our business and the machine’s advanced features allow us to increase our efficiency.”
According to Manna, those features include:
MMW began installation of the machine at its 70,000-sq.-ft., temperature-controlled facility shortly after Christmas. The machine foundation is more than 12 ' (3.7m) thick and contains 140 cu. yds. (128 cu. m)of cement—the equivalent of about 20 garage foundations—along with an extensive amount of rebar to enhance stability, Manna noted. The company started producing parts on the machine in April. “Installation was quicker than we’ve ever done before, primarily due to customer demand for the capacity,” he said.
Related Glossary Terms
- boring
boring
Enlarging a hole that already has been drilled or cored. Generally, it is an operation of truing the previously drilled hole with a single-point, lathe-type tool. Boring is essentially internal turning, in that usually a single-point cutting tool forms the internal shape. Some tools are available with two cutting edges to balance cutting forces.
- gang cutting ( milling)
gang cutting ( milling)
Machining with several cutters mounted on a single arbor, generally for simultaneous cutting.
- machining center
machining center
CNC machine tool capable of drilling, reaming, tapping, milling and boring. Normally comes with an automatic toolchanger. See automatic toolchanger.
- milling
milling
Machining operation in which metal or other material is removed by applying power to a rotating cutter. In vertical milling, the cutting tool is mounted vertically on the spindle. In horizontal milling, the cutting tool is mounted horizontally, either directly on the spindle or on an arbor. Horizontal milling is further broken down into conventional milling, where the cutter rotates opposite the direction of feed, or “up” into the workpiece; and climb milling, where the cutter rotates in the direction of feed, or “down” into the workpiece. Milling operations include plane or surface milling, endmilling, facemilling, angle milling, form milling and profiling.
- milling machine ( mill)
milling machine ( mill)
Runs endmills and arbor-mounted milling cutters. Features include a head with a spindle that drives the cutters; a column, knee and table that provide motion in the three Cartesian axes; and a base that supports the components and houses the cutting-fluid pump and reservoir. The work is mounted on the table and fed into the rotating cutter or endmill to accomplish the milling steps; vertical milling machines also feed endmills into the work by means of a spindle-mounted quill. Models range from small manual machines to big bed-type and duplex mills. All take one of three basic forms: vertical, horizontal or convertible horizontal/vertical. Vertical machines may be knee-type (the table is mounted on a knee that can be elevated) or bed-type (the table is securely supported and only moves horizontally). In general, horizontal machines are bigger and more powerful, while vertical machines are lighter but more versatile and easier to set up and operate.
- modular design ( modular construction)
modular design ( modular construction)
Manufacturing of a product in subassemblies that permits fast and simple replacement of defective assemblies and tailoring of the product for different purposes. See interchangeable parts.
- parallel
parallel
Strip or block of precision-ground stock used to elevate a workpiece, while keeping it parallel to the worktable, to prevent cutter/table contact.
- tapping
tapping
Machining operation in which a tap, with teeth on its periphery, cuts internal threads in a predrilled hole having a smaller diameter than the tap diameter. Threads are formed by a combined rotary and axial-relative motion between tap and workpiece. See tap.