Presented here are more tips and tricks to effectively perform finish work.
■ It’s a real pain when sanding discs are warped from improper storage or high humidity. Warped discs only cut on the high points, so it’s important that discs are fairly flat if you want to do decent finish work and get the most from your premium abrasives. Use a flattener to keep a little pressure on the discs as the humidity changes. Another trick to extend the life of sanding discs is to rotate them after you have used them for a while. When you rotate the discs slightly in relation to the backing pad, you can sometimes move the low point of the disc to an area on the backing pad that is higher.
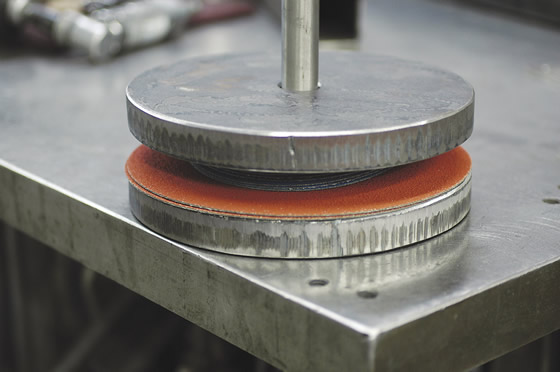
A simple shop-made flattener keeps a little pressure on the sanding discs to prevent warping as the humidity changes.
■ Wrap your abrasive around a stiff, flat bar with a small clamp to keep the abrasive from moving for better cutting action. The hard backing of a metal bar converts more of your elbow grease into removed metal. Flat bars sneak into gaps and openings where regular sanding pads won’t fit. It might be helpful to think of this idea as using a fine-grit file. The action is similar.
■ Tape abrasive paper to a surface plate to keep wrinkles out. I hate it when I get a nice, fresh sheet of silicon-carbide paper out to do a little flat lapping and the first thing that happens is I crinkle the paper and ruin it. This trick allows you to focus on the lapping job instead of concentrating on holding the paper steady.
■ Change the direction of sanding to give a balanced crosshatch pattern. I call this fake surface grinding. It’s not meant to deceive anybody; instead, it mimics a Blanchard ground surface. In some cases, it looks better than the standard figure-eight pattern normally created.
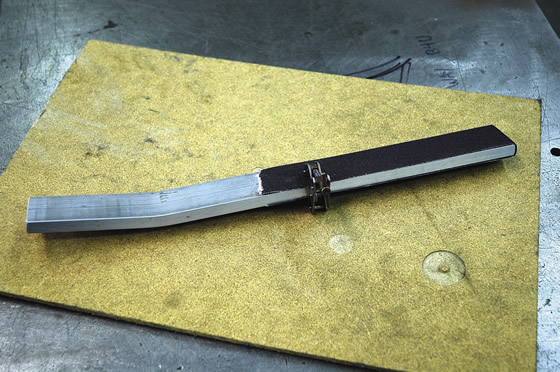
Wrap abrasive around a stiff, flat bar for better cutting action and use a clamp to secure the abrasive.
■ Change direction 90° each time you change abrasive grits. This makes it easy to see the scratch lines from the previous grit. There is nothing worse than trying to remove 100-grit lines with 600-grit paper.
■ Add a little light machine oil or WD-40 to make an abrasive act like a finer grit. This trick reduces the effective grit by about half. The kerosene in WD-40 keeps the abrasive clean and cutting.
■ Internal ball hones have saved my bacon quite a few times. These easy-to-use hones have a dozen uses around any shop. They work equally well on soft and hard materials when used with a common cordless drill. I have even applied them in a pinch to resize a commercial ball bearing bore to fit a slightly oversized shaft. They can deburr those nasty cross-drilled holes and steps in a bore, as well as improve the surface finish by an easy 10 points.
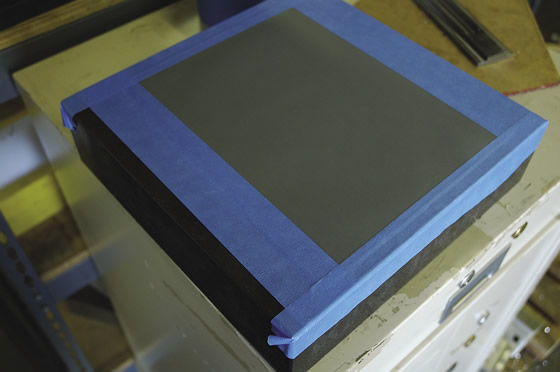
Tape abrasive paper to a surface plate to keep wrinkles out.
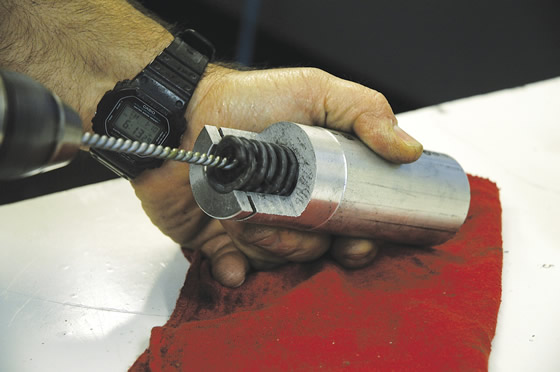
Ball hones can be used with a cordless drill to finish soft and hard materials.
■ An interesting deburring trick is to take steel or bronze wool and wrap it around a piece of threaded rod that’s held in a drill press. The wool’s mild cutting action is just the ticket for many delicate deburring jobs. The threaded rod has the right amount of tooth to retain the wool and keep it from spinning on the rod. The cutting action is similar to a nonwoven abrasive, but with a better polishing ability.
■ Square the table of a belt sander before starting a job. The table tends to droop downward during use if not checked. Therefore, if you want a finish squaring job to look nice, it only takes a second to check and adjust the table for perfect results. On this same note, the belt platens will need replacement or resurfacing every few years to maintain a decent flat backing for nice detailing work.
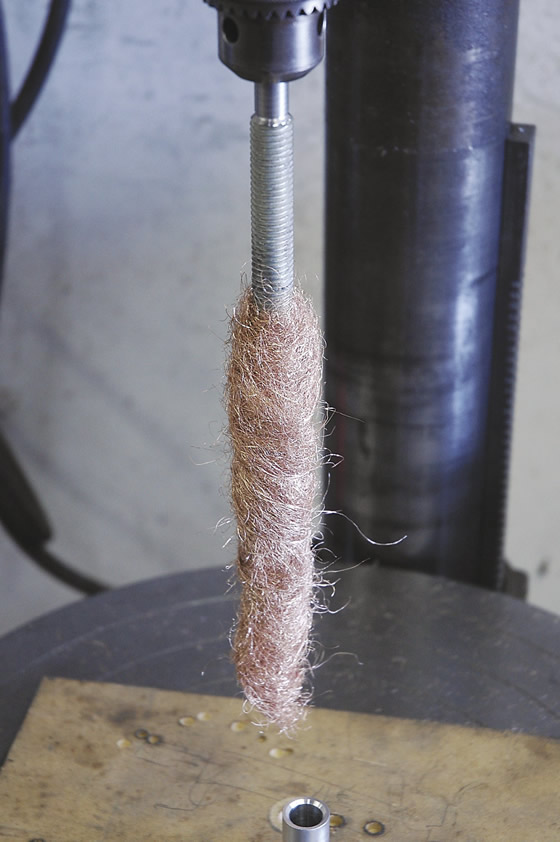
Wrap steel or bronze wool around a piece of threaded rod that’s held in a drill press for delicate deburring.
■ I have added replaceable front edges to belt sander tables. This allows me to keep the gap between the belt and table close and not have to replace the table casting every year. When you must detail very small parts, a handy trick is to use a piece of flat bar to reduce the gap between the belt or disc and the worktable. This prevents the tiny part or—worse—your finger from getting sucked into the gap and lost forever. CTE
About the Author: Tom Lipton is a career metalworker who has worked at various job shops that produce parts for the consumer product development, laboratory equipment, medical services and custom machinery design industries. He has received six U.S. patents and lives in Alamo, Calif. For more information, visit his blog at oxtool.blogspot.com and video channel at www.youtube.com/user/oxtoolco. Lipton’s column is adapted from information in his book “Metalworking Sink or Swim: Tips and Tricks for Machinists, Welders, and Fabricators,” published by Industrial Press Inc., South Norwalk, Conn. The publisher can be reached by calling (888) 528-7852 or visiting www.industrialpress.com. By indicating the code CTE-2014 when ordering, CTE readers will receive a 20 percent discount off the book’s list price of $44.95.Related Glossary Terms
- abrasive
abrasive
Substance used for grinding, honing, lapping, superfinishing and polishing. Examples include garnet, emery, corundum, silicon carbide, cubic boron nitride and diamond in various grit sizes.
- backing
backing
1. Flexible portion of a bandsaw blade. 2. Support material behind the cutting edge of a tool. 3. Base material for coated abrasives.
- drilling machine ( drill press)
drilling machine ( drill press)
Machine designed to rotate end-cutting tools. Can also be used for reaming, tapping, countersinking, counterboring, spotfacing and boring.
- flat ( screw flat)
flat ( screw flat)
Flat surface machined into the shank of a cutting tool for enhanced holding of the tool.
- grinding
grinding
Machining operation in which material is removed from the workpiece by a powered abrasive wheel, stone, belt, paste, sheet, compound, slurry, etc. Takes various forms: surface grinding (creates flat and/or squared surfaces); cylindrical grinding (for external cylindrical and tapered shapes, fillets, undercuts, etc.); centerless grinding; chamfering; thread and form grinding; tool and cutter grinding; offhand grinding; lapping and polishing (grinding with extremely fine grits to create ultrasmooth surfaces); honing; and disc grinding.
- lapping
lapping
Finishing operation in which a loose, fine-grain abrasive in a liquid medium abrades material. Extremely accurate process that corrects minor shape imperfections, refines surface finishes and produces a close fit between mating surfaces.
- polishing
polishing
Abrasive process that improves surface finish and blends contours. Abrasive particles attached to a flexible backing abrade the workpiece.
- surface grinding
surface grinding
Machining of a flat, angled or contoured surface by passing a workpiece beneath a grinding wheel in a plane parallel to the grinding wheel spindle. See grinding.